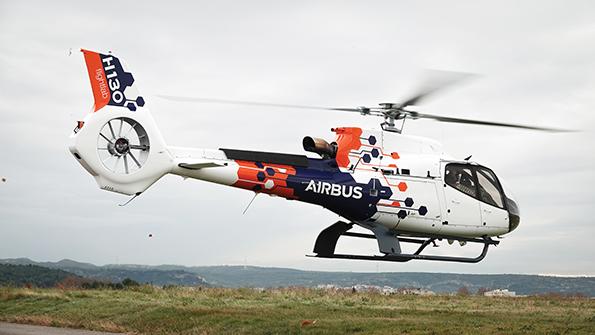
Airbus Helicopters has developed a flying laboratory that could help bring new innovations to market three times faster.
Flying since last April, the company’s single-engine H130 Flightlab has already tested several so-called technology bricks to improve safety and to pave the way for the company’s urban air mobility ambitions.
- Trials of 100-kW electrical backup system for safe autorotation taking place in 2021
- Airbus plans to introduce lidar-based obstacle warning system to market this year
“We want to move from ideas to flight-testing applications very quickly—this is at the heart of the Flightlab,” explains Tomasz Krysinski, Airbus Helicopters head of research and innovation.
“We are working together with other Airbus divisions,” he says. “We are integrating partners, startups, and that is how we are preparing for the future.”
Flightlab is an Airbus-wide research and technology initiative. The H130’s equivalent in the commercial business is the prototype Airbus A340 airliner used for the BLADE laminar-flow-wing experiments.
So far, the H130 Flightlab has been used to mature Airbus’ Rotor Strike Alerting System (RSAS), which uses lidar sensors fitted on each side of the aircraft to provide detection of obstacles that could present a collision risk to the main or tail rotor.
RSAS development flights took place in December, and the company plans to begin offering the system on its family of light helicopters by the middle of this year.
To support urban air mobility efforts, the Flightlab has also undertaken flight trials in conjunction with the French civil aviation regulator, the DGAC, to gauge the perception of helicopter sound in urban areas and to better understand noise propagation.
During 2021, Flightlab will be used to further develop the company’s EAGLE project—which stands for Eye for Augmented Guidance for Landing Extension—an electro-optical, gimbaled camera system that aims to support enhanced flight automation (AW&ST Oct. 16-29, 2017, p. 38). Previous trials had already enabled automated landings using imaging data. The next step will involve EAGLE technology matured for low-altitude navigation, automatically identifying obstacles.
A more significant research effort to support urban air mobility activity is planned for 2022: The installation of a hybrid fly-by-wire control system will aim to modify the ergonomics of the flight controls to make flying the aircraft more intuitive, and inceptors will be fitted to the mechanical control linkages in the helicopter to provide more authority and a level of envelope protection. Airbus says the trial will study several combinations of inceptors and control laws to define the most optimized configurations.
“Several possibilities will be tested on stick inputs with regards to aircraft response, such as speed hold and automatic return to hover,” a company spokesman tells Aviation Week.
The combination of both the flight control system and EAGLE is designed to reduce the workload of the pilot by providing “full autonomous assistance so that the pilot only needs to make decisions if the system is failing,” says Nicolas Damiani, autonomy expert at Airbus Helicopters.
Airbus will also test a new health and usage monitoring system (HUMS) technology that it hopes will become cost-effective for use on light helicopters. Until now, the weight of wiring, systems and black boxes associated with such systems has been too heavy and costly to install on light helicopters, but the new lightweight HUMS integrates the analysis software into the five sensors that monitor the H130’s dynamic systems.
“The accelerometers in the system will feature software [that] will pre-analyze the data before it is sent to the global computer on the aircraft,” says Alexandre Gierczynski, Flightlab project leader.
The HUMS system will also enable owners to undertake rotor track and balance without the need for an external device to measure it.
The Flightlab will also be the platform with which Airbus will test a refined electrical backup system. It will use a Thales-supplied 100-kW electric motor powered by a battery developed by Airbus Defense and Space, in what Krysinski has previously called a mild-hybrid architecture, to act as a safety device in the event of an engine failure. As rotor speed falls, the electric motor will kick in and give the pilot more time to find somewhere to make a smoother and safer autorotation landing.
The trials will build on flight testing carried out with an AS350 Ecureuil/Squirrel/AStar platform in 2011. A later phase will expand the capability of the system, connecting two motors in parallel to the dynamic system and allowing the aircraft to make 2 min. of electric flight in a low-power setting.
Krysinski believes that in addition to safety benefits, the hybrid technology, even in this early stage of development, could increase the payload capacity of the light helicopter, although the systems themselves will come with weight penalties (AW&ST Feb. 25-March 10, 2019, p. 68).
Hybridization will also be a “lever” for reducing rotor speeds and reducing noise and could open up a path to hydrogen-based propulsion, Krysinski suggests.
Gierczynski says the company plans to test a road map of technology on Flightlab through 2024. Some of these technologies will be tested in parallel, and others in isolation, notably the EBS, he says.
“Having a dedicated platform to test these new technologies brings the future of flight a step closer and is a clear reflection of our priorities at Airbus Helicopters,” said Airbus Helicopters CEO Bruno Even.