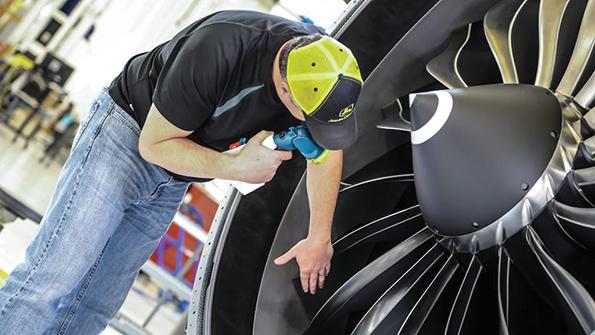
As commercial aerospace business pressures mount in the form of growing inflation, worker shortages and dubious production rate increases—in addition to its own corporate-specific challenges—GE Aviation is doubling down on lean manufacturing to help it meet customer orders and shareholder expectations.
During a March 10 investor briefing in Greenville, South Carolina, General Electric (GE) leaders—from Chairman and CEO Larry Culp, Jr., to relatively new GE Aviation boss John Slattery—emphasized that cost takeouts, process improvements and improved quality of life for workers through lean exercises will be the backbone of a plan to meet robust performance and financial goals ahead of the corporation’s breakup. Around 2024, GE will comprise just GE Aviation and a few other heritage offices.
- Can a CFM high-pressure turbine blade be made in only 10 days?
- New GE Aviation chief says no corner is immune to improvements
“My priority and the priority of my team is to deliver on the ramp,” Slattery said. “The ramp not only on the original equipment [manufacturer] side to support Boeing and Airbus, and indeed our airline customers around the world, but also the ramp on the services side of the business. And I’m confident we can execute that ramp, principally by deploying lean right across the organization.”
Lean “refers to a production principle stating that any component of a business enterprise that fails to directly benefit a final product is superfluous,” according to Investopedia. Lean manufacturing methodology focuses on value creation while eliminating waste and nonessential processes. The trend became widely known in the Western business world in the 1990s from the Toyota Production System.
One key example is the goal to cut CFM International high-pressure turbine (HPT) fan blade manufacturing time to just 10 days, from 35 days in 2019, as well as to achieve zero defects in each blade and on-time delivery. CFM is the 50-50 joint venture between GE Aviation and Safran Aircraft Engines.
In Greenville, GE Aviation produces HPT blades for LEAP, GE90, GEnx, GE9x, Passport 20, various CFM engine types and HondaJet engines. The site also supports certain military engine product types, including T700, F414 and CF34. On average, the site—with roughly 250 employees—ships 1,000 parts per workday in support of the GE Aviation engine portfolio.
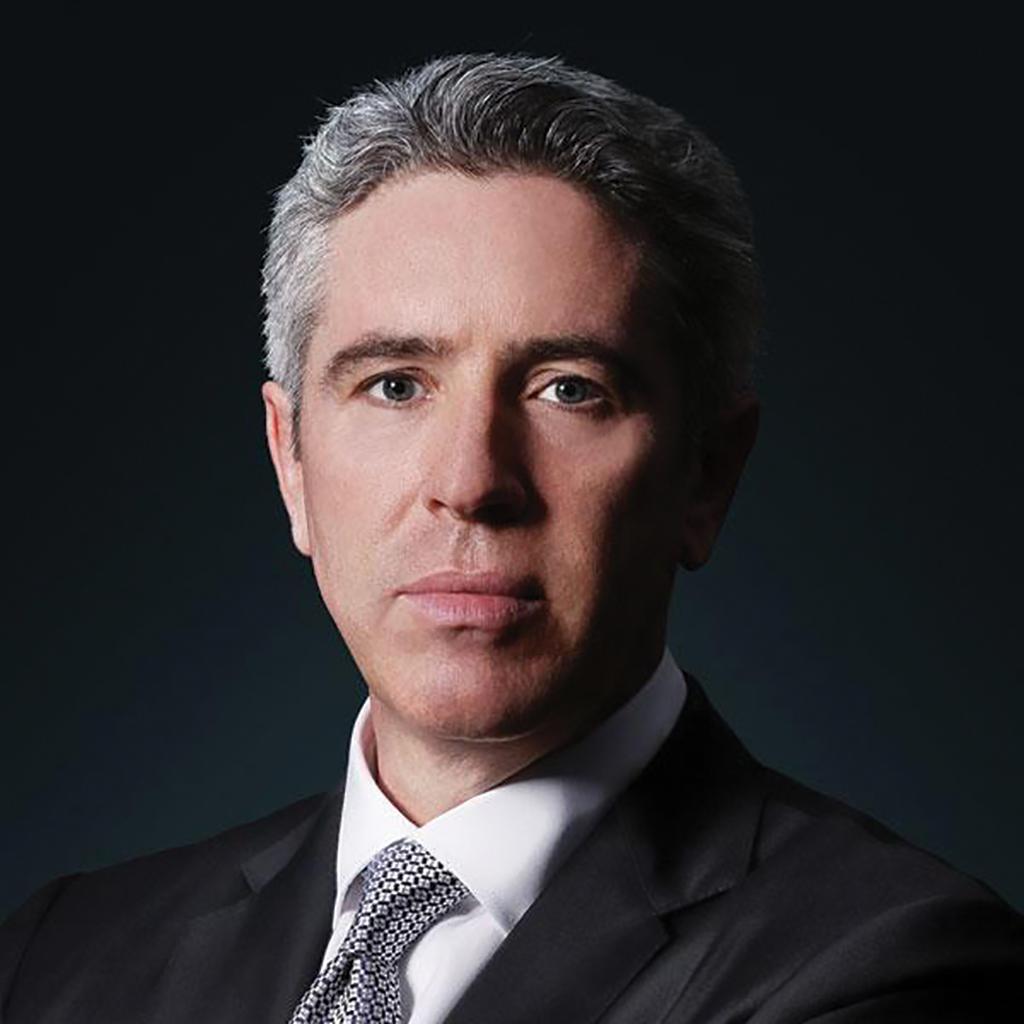
The decision to target a 10-day blade operation was based on known capabilities, both on-site and with suppliers, according to company representatives. “We knew from tracking time that we could complete on-site manufacturing processes in a total of three days between our pre-coat and post-coat operations,” GE Aviation officials said. “We also knew we could get blades from our suppliers in seven days. With lean, we smoothed out the process with our supplier to ensure they were getting a steady flow of parts so that we could receive a steady flow of parts aligned with customer demand.”
In two years, from 2019 through 2021, workers cut the lead time by nearly half on the CFM line. “These [measures] have had a direct impact on the business, reducing significant overhead costs while strengthening its ability to deliver according to customer demand,” GE Aviation said, declining to provide more details. Other lean transformation results to date include:
• 90% reduction of in-line inventory.
• 40% line utilization increase.
• 30% reduction in shop footprint.
• 50% reduction in part travel time.
• 30% total shop inventory reduction.
The goal this year is to reduce lead time to 18 days on the GEnx and 15 days on most other parts and processes.
Another target area is services, said Rafael Aymone, general manager of GE’s Brazil Technology Center—a GE Aviation maintenance, repair and overhaul shop. “Back in 2019, we were working extremely hard trying to fulfill our customer expectation on turnaround time,” Aymone told attendees at the GE investor conference. “No matter how hard we tried, our on-time delivery was below 20%. We decided to take a step back and reassess our processes using a different perspective,” he continued. In 2020, the CFM56 assembly line was certified, and on-time delivery climbed to 78%, up from 10% a year earlier. The following year, the site did more than 40 weeklong events based on kaizen—a Japanese business philosophy of continuous improvement—and more than 2,000 just-do-it improvement projects.
Apparently, no corner of GE Aviation will be immune from the streamlining initiatives. Slattery promises lean will be pushed through the whole division, not just shops; for instance, the chief financial officer’s department will improve on-time delivery of financial results reporting.
While bringing obvious cost improvements, the new emphasis on lean manufacturing has been billed as good for workers, too. “It’s ringing the cash register, [making] it more productive,” Slattery explained. “But you’ll also see it’s making the environment more respectful to each of our employees.”
Still, the new push comes after decades of GE Aviation already implementing continual process improvements under lean applications. Asked by an analyst during the investor day why the renewed push was expected to produce dramatic new results—and more pointedly, whether GE had been pursuing “fake” or “inadequate lean” in the past—Slattery responded affirmatively. “I’m looking directly at Larry,” Slattery said. “You weren’t far off base.”
Many examples show how GE Aviation had become good, but “very few where we’re great,” Slattery added. “I think the first step in lean is the humility to recognize that.”
Comments