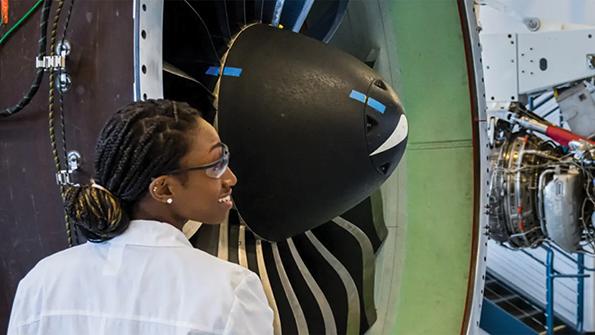
Diversity, equity and inclusion is one tool to boost future workforces, but just as important—or more so—is adapting to changing generational priorities.
Kristen Kucko is a robotics lab technology teacher at Thomas Jefferson High School for Science and Technology in Alexandria, Virginia—one of the most sought-after, elite public magnet schools of its kind in the U.S. In November, as part of the SpaceX-CRS-26 space station resupply mission, NASA launched the TJ Reverb cubesat, which was designed, built and programmed by her TJ Space students.
- Relief from labor shortfalls is anticipated
- Industry faces generational change in worker priorities beyond the “great resignation”
- The sector’s need to attract new, unfamiliar workers and skills will only grow
The cubesat was not even the first by TJ high school students—in 2013, a cohort saw their TJ3 satellite launched, establishing the high school as the first known to launch a satellite. Kucko, who took over TJ Space in 2019, is trying hard to give her students hands-on experience, in turn possibly hooking them for life into an industry that says it desperately wants their talent and labor. But she keeps running into the same problem: the aerospace and defense industry itself.
“I had students who actually built cubesats, and they did not get internships. That is crazy,” Kucko says. “Something is wrong.”
A lot seems wrong these days when it comes to human resourcing in the aerospace and defense sector. Workforce shortages dominate business news headlines worldwide, and this industry is no different. In recent quarterly teleconferences and investor conferences, Western executives continued to blame labor challenges for financial and programmatic shortfalls, with complaints voiced from original equipment manufacturers on down through Tier 4 suppliers.
Still, it is unclear just how bad the situation is for aerospace and defense. Managers of large defense primes, airframers, engine-makers and their Tier 1 suppliers recently indicated during investor events that, generally, the worst of the COVID-19 pandemic-era workforce shortages are behind them. Executives from subtier suppliers, however, still frequently complain of scarce labor availability, as many did before the pandemic.
The good news is that talent issues finally seem to be gaining in priority. The bad news is that there are few easy answers—and the question remains whether industry can get out of its own way when trying to attract and retain skilled workers. Fresh surveys from trade associations and consultants, as well as interviews with and public comments from executives and others, show that the industry has a lot more work to do to woo and keep workers.
“People still kind of stumble their way into it,” says Quincy Brown, director of space science, technology, engineering and math (STEM) and workforce policy at the National Space Council. “The opportunity and responsibility to fix some of these things is on industry.”
A March report from McKinsey & Co. consultants found that the aerospace and defense industry lags behind its technology and automotive peers on many touchstone perceptions of what potential employees value. The industry trails on culture and values, diversity and inclusion, leadership and speed. It only leads in motivation.
For a sector that still basks in the glory of the 1969 Moon landing and winning the Cold War, that is both unsurprising and unsatisfying. Even before the pandemic—and the subsequent “great resignation” of job switching and tsunami of early baby boomer retirements—the industry knew its mission alone was not enough to generate pipelines of workers. Engineers, computer science graduates and others can choose a variety of competing industries that seem more lucrative, modern or spiritually rewarding—and they have been doing so for a generation. Before smartphones and social media companies, oil and gas giants were seen as the vampires sucking away engineering talent.
Yet the new McKinsey workforce report, “Navigating the Gray-to-Green Transition in Aerospace and Defense,” underpins that headwinds are only strengthening. Industry faces a multipronged challenge, including simultaneous demographic turnover and new expectations about working conditions.
“A wave of retirements are on the horizon, reflecting the fact that about a third of industry employees are aged 55 or older,” the report says. “Another powerful factor shaping the [aerospace and defense] jobs market since the COVID-19 pandemic is increased employee willingness to switch.”
The “great resignation” has become an established phenomenon, with studies showing that 46% of employees are thinking about changing jobs in the next 3-6 months—a proportion that has remained steady over the past year. Younger employees are twice as likely as veterans to move on, according to McKinsey.
Another report, conducted by the Aerospace Industries Association (AIA) and the American Institute of Aeronautics and Astronautics (AIAA) and carried out by Ernst & Young US (EY), found that the industry’s attrition rate rose to 7.1% in 2022 from 5% in 2020 and 4.3% in 2017 (see chart above).
Just a decade ago, attrition rates were worryingly low, according to past Aviation Week workforce studies. Not anymore. “Attrition rates are high,” Raytheon Technologies President and Chief Operating Officer Chris Calio said in January and February financial presentations. “Labor availability remains a constraint.”
The October AIA-AIAA-EY report, which surveyed 30 companies last year with 850,000 workers, echoed that. “Workforce and talent concerns remain top of mind for [aerospace and defense] companies as they look at an increasingly competitive marketplace for highly skilled employees, both today and into the future,” the report says. “With rising employee turnover compounding an industry-wide shortage of talent, many companies are considering, or beginning to implement, more comprehensive talent strategies to help their workforces meet increasing demand.”
Many companies also say they are trying to develop more supportive work environments for their workforces and new hires by adding programs around mental well-being, leadership and technical degree/apprenticeship opportunities. To further attract talent, companies also are looking into how to distinguish themselves with employee recognition, career development, “improved” compensation and flexible work arrangements.
Above all, there is a dawning realization that aerospace companies are becoming noteworthy waypoints for Generation Y and Z workers. In other words, these younger workers will boast to their friends, family and later employers that they once worked at Boeing or Aerojet Rocketdyne, as alumni of SpaceX, Amazon or others boast today.
These moves are welcome, but the response has been slow to meet the need. In the latest AIA-AIAA-EY survey, 69% of respondents reported that turnover increased in the last year. Moreover, aerospace and defense companies are competing not only with each other, but also with other industries as demand in aerospace and defense is soaring again.
“This talent shortage may be coming at an inopportune time for [aerospace and defense] companies,” the trade group study observes. “Many organizations are ramping up production to meet increasing demand caused by the rebound of air travel from the pandemic, the need for advanced defense capabilities due to rising geopolitical tensions and a renewed vision and prioritization of space travel and deep space exploration.”
Therein lies the rub. Numerous industry sources tell Aviation Week that many of the recruitment, retention and upskilling challenges they face have been around for decades. For example, it is nothing new that the few key forgings and castings providers need 6-12 months to turn a green new recruit into a productive artisan. But since core suppliers such as Precision Castparts laid off roughly 40% of their workforce during the height of the pandemic, the delay in catching up is exacerbated by an accelerated recovery.
This scenario has played out across industry. In the early months of the pandemic, many suppliers slashed their workforce, some by around 50%. In prior downturns, industry could win back the vast majority of its laid-off workers and bring on a modicum of new additions. Not now. Too much of the macro-environment has changed, while too few industry players have adapted.
“The companies that are complaining about not being able to hire are the same companies that complained a decade ago,” says one advisor who focuses on aerospace and defense. Whether the industry can do more to attract Gen Y and Z workers is debatable.
Meanwhile, as the “gray generation” of baby boomers retires and younger employees switch jobs more frequently, essential industry skills are being lost, the McKinsey report warns.
“The number of mechanical and electrical engineering roles is outweighed by more lucrative software opportunities, sometimes by as much as a factor of 13.” Industry companies pay entry-level software engineers about half as much as technology giants such as Facebook, Amazon and Google, so it is not surprising that tech talent outflows are potentially twice the rate of inflows.
As the industry falls behind its competitors in pay, graduate engineers are spreading their nets more widely, the report stresses. Fewer see their future in aerospace and defense. There has been an 8% decline in hiring of aerospace, aeronautical and astronautical engineer graduates over the past five years. Despite a doubling in the number of computer engineering graduates, the industry has seen a 7% drop in postgraduate employment over the same period.
At least some of that is a vestige of long-ingrained habits. Kucko can attest to this, and past Aviation Week workforce reports show it, too. Since the Cold War, this industry has preferred to poach experienced personnel from large rivals than recruit and train substantial cohorts of “green” undergraduate hires. And suppliers have shrunk with the contraction of U.S. manufacturing across the board. The mindset of consolidation—reinforced by decades of downsizing that climaxed with the pandemic—is slow to change.
Industry leaders want things to change. The AIA-AIAA-EY study reflects that at the highest levels. As turnover spikes, many companies have made a concerted effort to respond, the report says, offering differentiated benefits such as work-from-home flexibility and newer, faster career progression opportunities. Meanwhile, the industry is replete with examples of companies partnering with community colleges, high schools and even middle schools on aerospace-related activities or minority worker recruitment.
But middle managers who carry out corporate policy still may have doubts. For instance, while 65% of respondents say they successfully operationalized more flexible work arrangements, many admitted there is still institutional unease about these arrangements, the AIA-AIAA-EY study finds.
Also, industry leaders are sending mixed messages. “It turns out we beat our hiring goals last year; [we] hired 15,000 people, largely engineers and mechanics,” Boeing Chief Financial Officer Brian West told a Bank of America investor conference in March. “We’ll pick our spots, but I feel like there’s plenty of innovation. And by the way, our development pipeline is full.”
Boeing said it expects to hire 10,000 more workers this year but plans to also lay off a couple of thousand, mostly in corporate and support services. Airbus said it will hire 13,000 people and Thales, 5,500. But overall, job postings were down as a percentage of head count in January from June 2022, according to Melius Research. Job postings as a percentage of head count decreased to 5.1% from 6% at defense hardware companies, 4.7% at hybrid aerospace and defense companies and plateaued at 2.3% at commercial aerospace companies.
“Is [aerospace and defense] labor availability getting better?” financial analysts at Melius asked in a January report.
Not surprisingly, industry leaders want to grow the pipeline of potential workers. Part and parcel to that, they are doubling down on diversity, equity and inclusion efforts to broaden the sociocultural makeup of their staff. This comes after decades of trying but hardly making a difference in minority participation rates.
While there is not necessarily a crisis when it comes to aerospace and defense writ large, some niches are flashing proverbial warning lights. Trade associations for commercial space and the maintenance, repair and overhaul sectors have been spotlighting their concerns for years. Interestingly, it is not that those sectors lack skilled engineers, but rather that they struggle to attract enough workers overall.
The headwinds cited range from the esoteric—loud repair shops or remote launch complexes are not everyone’s ideal workplace—to the pragmatic. A young worker unaffiliated with the industry may see becoming an air conditioning repairperson as both economically safer and more quickly financially rewarding than specializing in business aircraft. If you are a computer scientist graduate, do you aim for the nascent space industry or the proven technology and financial sectors?
“[To] a normal aircraft or space or aviation enthusiast, we don’t have to explain why—of course they come to Airbus,” says Marco Wagner, human resources director of Airbus Commercial Aircraft in Germany. “When we look for [information technology] experts, cybersecurity experts, they are not naturally interested in aviation.”
Nevertheless, when it comes to the quality of young skilled graduates, industry has little concern. “In general, I think we’re in a strong position,” The Aerospace Corp. CEO and President Steve Isakowitz tells Aviation Week. “The quality of the students is really just absolutely remarkable in terms of what we’re bringing in. The way we’re teaching our students has, frankly, greatly improved since my day.”
Executives at OEMs and large Tier 1s say they expect the labor crunch to ease this year. Those companies have the financial wherewithal to pay what they need to hire whom they want. But they know that if their subtier suppliers have labor issues, final deliveries to end-market customers such as airlines, lessors or government agencies remain at heightened risk.
And that is where the hurdles are greatest. “Adding direct labor is one of the first steps to increasing throughput,” says Alex Krutz, founder and managing director of Patriot Industrial Partners, which works with many subtier suppliers. “This sounds overly simple, but many companies plan their direct labor staffing levels based upon budgeted earnings before interest or other financial goals,” he tells Aviation Week. “Many of these same companies have data that shows the planned hours they need to produce and knowingly don’t actively staff to that plan.”
Krutz, who works everyday at restructuring small and midsize enterprises, says these companies simply must step up and institute robust onboarding processes to cut turnover. Also, they must pay market rates and create stay-on incentives to get employees over the 90-day mark. “It is a big impact to the business to choose between cost and not delivering,” he says.
In the end, industry can make many improvements in how it recruits and retains workers, but the challenges are likely to endure, if only because of classic business practices or generational changes. Industry leaders see it as part of their risk management. “It is a problem, but we have faced this before,” Isakowitz says.