Airbus, Boeing Face New, Old Production Challenges And Shifted Powers
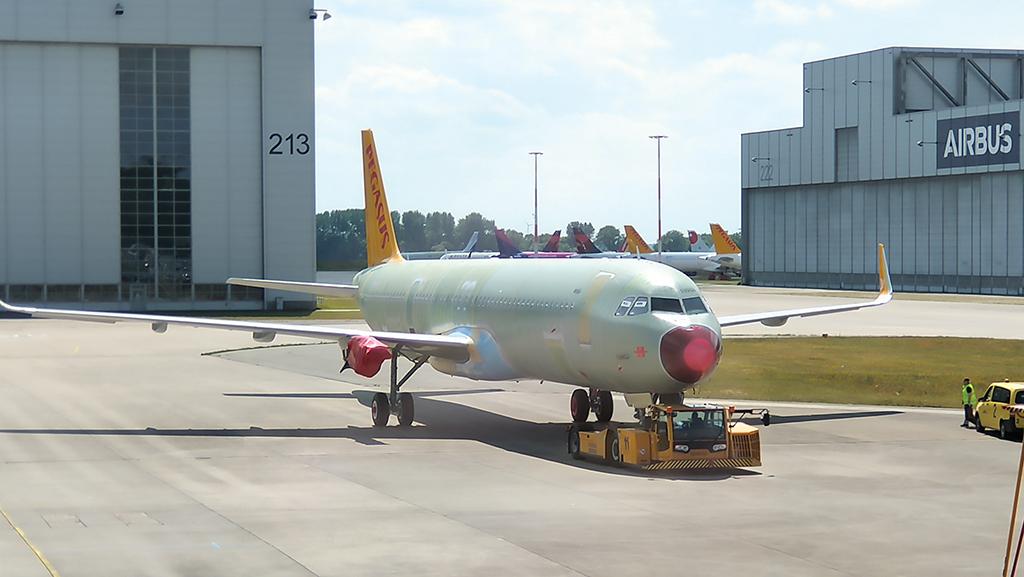
At the last Farnborough Airshow, four years ago, the familiar Airbus-Boeing single-aisle order race and delivery ramp-up problems made the headlines. In that sense, on the surface at least, it would seem little has changed.
- Airbus struggles with planned single-aisle output increase
- Boeing 737-7/-10 certification remains uncertain
- Supplier delays affect production plans for both OEMs
Just as in 2018, this year’s Farnborough will once again see Airbus and Boeing playing the order number game while also stressing the supply chain and production challenges each faces as ramp-up plans continue.
The parallels end there, however. While both manufacturers were equally affected by the industry devastation caused by the COVID-19 pandemic, the longer-lasting impact of the 737 MAX accidents on Boeing’s fortunes has dramatically changed the picture since the heady days of 2018. The result is a study in contrasts.
Airbus will come to Farnborough 2022 boosted by the recent test-flight debut of the long-range A321XLR and ongoing plans to build a remarkable 89 single-aisle A320neo and A220 aircraft per month starting in 2025. Boeing, on the other hand, has yet to formally achieve a rate of 31 737 MAXs per month as it wades through a transformed regulatory landscape to rebuild its reputation, achieve production stability and complete certification of the final two members of the narrowbody family-—the 737-7 and the 737-10.
Despite being battered on all fronts—including missteps and cost overruns on key defense programs as well as debilitating revenue hits and delays on the 787 and 777-9—Boeing is keeping faith with the MAX. Signs of a sustained 737 program renewal are emerging, with more than 630 737-8/-9s now in service, recent hints of an imminent return to service in the critical Chinese market and an unfilled order backlog of almost 4,100 that continues to be boosted by what Boeing CEO David Calhoun calls “robust demand.”
Efforts to stabilize production at 31 per month, meanwhile, continue at Boeing’s Renton, Washington, facility, where the company is building 737s on the west and center lines—two of the three final assembly lines in the factory. “We’ll be activating the east line here at some point once we make sure that we’ve got all of the trained personnel necessary to successfully start that line for our production requirements,” says Dennis Eng, director of 737 program business operations.
Although Boeing does not provide specific employment numbers, Eng says the company is aggressively recruiting new personnel. “We’ve had job and recruiting fairs recently with a lot of success. We’ve been making offers on the spot for engineers and mechanics, logistics, transportation, supply chain-—and all areas because we are going up in rate,” he says.
“The heart or the density of the market still is in the 737-8 and -9 space in terms of size,” says Darren Hulst, Boeing’s commercial marketing vice president. “But it’s very important for us to complete that family both on the entry level and the low end of the market, as well as the growth side of the market, to provide even more efficiency to our customers who continue to need the growth in that space.”
Despite the accidents and program delays, Hulst says Boeing has taken 1,015 gross orders for the MAX family since its return to service in late 2020. Since that time, more than 410 have been delivered, over 70 of which are high-capacity 737-8-200s for low-cost carrier Ryanair. “This reflects the diversity of demand around the world for the 737 as well as the value of the variance of the family that make up the 737 MAX,” Hulst says.

“As we move through 2022, I think some of that initial demand that we saw last year in North America will move into Europe and other markets, as they see recovery and demand for their own fleet replacement and growth rates, and even the startup market as we look at new airlines emerging through this period,” he adds.
Given its already dominant position in the space, demand is the least of Airbus’ worries about its narrowbody product line. But as in 2018-19, everything is now about turning orders into deliveries. The numbers for the first five months indicate how difficult the task already is. And the complaints customers are raising sound very familiar to that period four years ago, when resources were stretched beyond limits and production delays went through the roof.
Airbus is targeting 720 commercial aircraft deliveries this year. A350s, A330neos and A220s will account for roughly 120-130 deliveries, based on current and planned production rates. Airbus therefore needs to hand over around 600 A320neo-family aircraft to meet its own goals, roughly an average production rate of 50 aircraft per month in 2022. Until May, Airbus was delivering an average of only 36 aircraft per month—a big increase in output will be necessary. For reference, Airbus is measuring the rate at station 40, where the wings are joined to the body, not by the number of actual deliveries.
There are few indications that things will improve quickly. Important supplier items, including engines, are arriving late at the final assembly line. Deliveries are routinely 6-8 weeks late, industry sources say. “Things will get worse before they get better,” the sources say. “There is a great deal of concern in the customer base.”
Not only should the rate be at around 50 aircraft per month already, it must also be close to 60 by year-end for the road map to 75 by mid-2025 to remain realistic.
Airbus A320neo-family program chief Michael Menking is not revealing details, but he concedes that a lot more work must be done to get to where Airbus wants to be. Rate increases will happen in steps, therefore current levels should not be taken as indicators of ramp-up issues, he says.
Key elements of Boeing’s recovery plan are completing the MAX family and beginning deliveries of the 737-7 and -10, particularly since the initially slow sales of the smallest and largest members of the family have now grown collectively to almost 1,000 aircraft—constituting a significant slice of the MAX orderbook.

But getting there is proving to be a long, hard slog for Boeing which, particularly in the case of the -10, urgently needs the higher-capacity aircraft to shore up its portfolio against the highly successful A321neo, A321LR and A321XLR offerings. As of mid-June, neither the 737-7—which first flew in March 2018—nor the 737-10, which began its test campaign almost exactly a year ago, were thought to be close to certification.
The certification process, which has already been slowed to a deliberate crawl as part of the doubling down on regulatory scrutiny and safety by both Boeing and airworthiness authorities, has been further challenged by U.S. government legislation passed in 2020 in the wake of the MAX accidents. Under the Aircraft Certification, Safety and Accountability Act (ACCSA), the FAA is prohibited from approving any new air transport aircraft without flight crew alerting systems after the end of this year.
Since the formerly agreed certification basis for the MAX was derived from the 737 Next Generation—which does not have an Engine Indicating and Crew Alerting System (EICAS) of the sophistication now required—the clock is ticking for both derivatives. Although the 737-7 is closer to approval, having completed flight tests, Boeing appears quietly confident of meeting the deadline—a sign underlined by the appearance of several 737-7s on the current production line.
The 737-10, which introduces several design changes, will not be approved in 2022 and is targeted at deliveries starting next year. The extended test schedule means Boeing must therefore either develop an EICAS for the aircraft, which it argues would potentially add risk, find an alternative system-based compromise or seek an extension.
“We’re all well aware of the timeline that’s in the ACCSA legislation,” says Mike Fleming, Boeing senior vice president for 737 MAX return to service, commercial customer support and commercial derivative programs. “But I will tell you from a Boeing standpoint and from the FAA standpoint, we’re working to certify the airplanes through the regulations that we have in place, and what we believe is the right approach to demonstrate that the airplane is safe.”
Engineering test flights of the 737-10 are “nearly complete,” Fleming says. The two -10 development aircraft have flown over 500 flight hours on more than 600 sorties. Performance testing has “recently wrapped up,” he notes, and the company is pleased with the test results of the new semilevered landing gear design and associated brake system, he adds.

A key focus for the -10 test program has been the enhanced angle-of-attack (eAOA) system, an addition required by the European Union Aviation Safety Agency as part of its agreement to approve the 737 MAX’s return to service. Consisting of a synthetic sensor that collects data from five different aircraft parameters, the new system cross-checks derived AOA against inputs from the two standard AOA sensors mounted on either side of the aircraft’s nose.
The system, likely supplied by Collins Aerospace, has been installed on both 737-10 test aircraft and “is going very well,” Fleming says. “The pilot response from both our pilots and the customers has been very positive,” he adds. “It is designed to eliminate any of the erroneous indications that we think could happen on the airplane, and it significantly reduces the pilot workload associated with any kind of erroneous indication.”
Comments