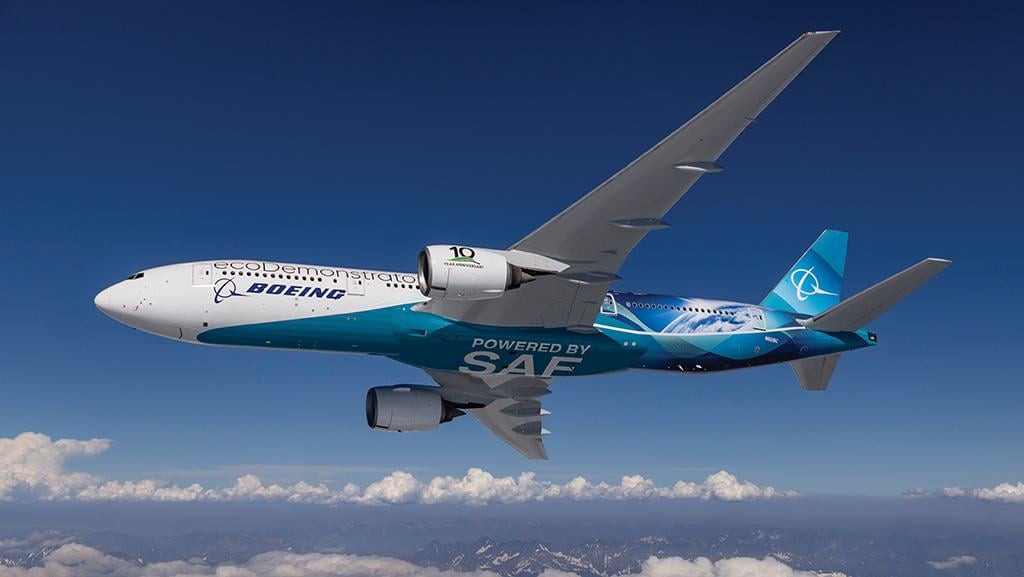
Boeing’s use of a dedicated ecoDemonstrator, the ninth in the program, will enable longer-term testing and more invasive modifications.
Bearing an image of Earth on the aft body and the words “powered by SAF” emblazoned beneath the fuselage, Boeing’s latest ecoDemonstrator—a 777-200ER—is poised to begin the next flight-test campaign in the OEM’s long-running program.
Set to begin just weeks after the International Civil Aviation Organization’s Oct. 7 adoption of the goal of achieving net-zero carbon emissions by 2050, the role of the new-look ecoDemonstrator has taken on fresh significance as part of the company’s recently unveiled approach to decarbonization dubbed “Everything for Zero.”
- 777-200ER trials are planned to run through 2024
- New smart vortex generators are being tested
“We’ve got the world on the back of the aircraft, and I really wanted to get that on this ecoDemonstrator because we are now really a global asset,” says Rae Lutters, ecoDemonstrator program manager. On top of its role as a tool for testing and proving out potential new technologies, the ecoDemonstrator is seen by Boeing as a flagship for “showing how we are leaders in sustainable aviation,” she adds.
Beginning in 2012 with a relatively modest test campaign involving a leased 737-800, the decade-old ecoDemonstrator program now forms a major pillar of Boeing’s research and development portfolio at a vital time for the manufacturer. Despite unparalleled challenges and financial headwinds since 2019, the company has continued to invest in the initiative, recently acquiring the 777-200ER for conversion into a dedicated flying technology testbed for at least the next two years.
The first use of a 777-200ER variant in the program marks only the second time that Boeing has acquired a widebody test asset devoted specifically to the ecoDemonstrator campaign. Aside from 2019, when Boeing bought a used 777-200 for the program, every other ecoDemonstrator has been flown in partnership with an airline—or, in the case of the 2016 campaign, with Embraer using a modified E170 regional airliner. In addition to a 737-800, the program has included a 737-9, 777F, 787-8, 787-10 and a 757-200 that had been operated by a former charter airline and withdrawn from commercial service.
Having a dedicated airframe “enables us to be able to test a lot more things on our own time, where we don’t have to give the airplane back to the operator,” Lutters says. In addition, the aircraft does not require refurbishment after the end of the ecoDemonstrator campaign and can be configured for more invasive test equipment or modifications.
The 777-200ER, like previous ecoDemonstrators, will operate on “some blend of sustainable aviation fuel,” Lutters says. “The highest blend that is available to us is up to 50%, which is the certified limit. This year we’re flying typically on a 30-70 blend because that is the highest ratio we can get right now due to the limitations of the current production system.”
Flying with sustainable aviation fuel (SAF) blends not only helps prove out day-to-day operability using alternative fuels, but the advent of the technology also will help add momentum to the growth of SAF refining capability on the industrial scale required for its wholesale adoption over the coming years, Boeing says. The ecoDemonstrator also forms part of ongoing studies with NASA to measure particulate emissions that will inform research on contrail formation and the associated sensitivities connected with the use of different SAF.
Technologies to be evaluated over an initial six-month flight-test program on the 777-200ER include several all-new features as well as the latest evolutions of technologies tested on earlier campaigns. The latter includes an actively actuated set of retractable vortex generators (VG) developed with NASA under the SMART (shape memory alloy reconfigurable technology) program, which builds on work performed during the 2019 test program.
Vortex generators reenergize flow and improve aerodynamic performance, but they generally are needed only for slower speeds at lower altitudes rather than during cruise, when the static vanes are a source of drag. The SMART program developed a set of experimental VGs that could be passively deployed and retracted to be flush with the wing by using phase-transforming shape memory alloys (SMA) that react to changing temperature.
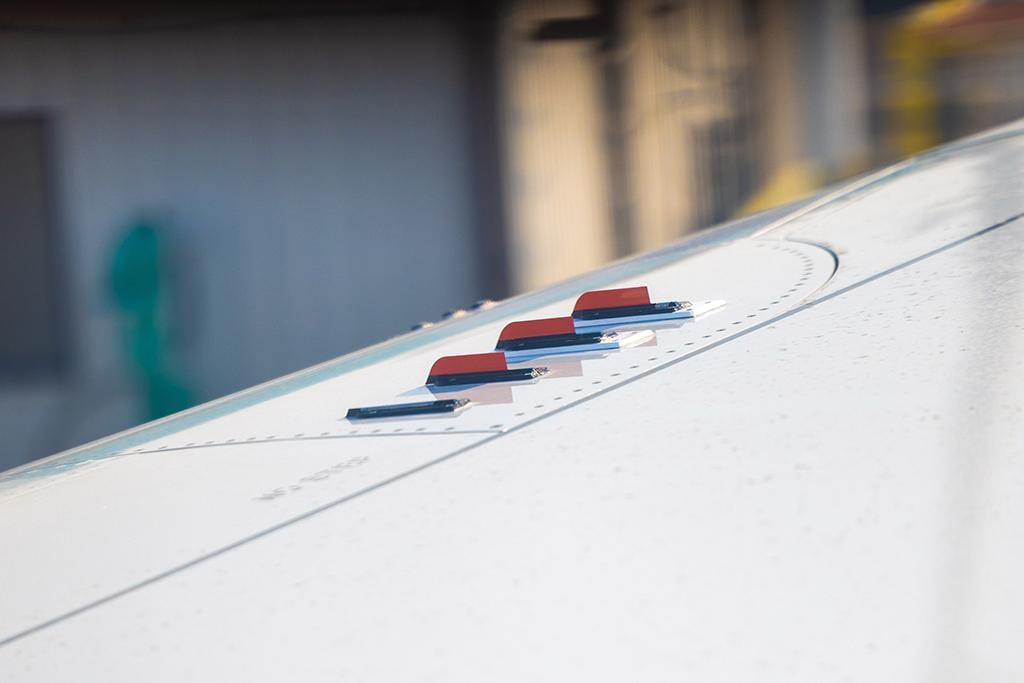
Although tests of the VGs with an SMA rotary actuator demonstrated that the units could be integrated into a 777 wing and would passively retract in colder upper-atmospheric temperatures, the reaction time for extension was slow, particularly after the wing had cold-soaked in cruise conditions. “This year, we’re adding a test with a heater mechanism that would enable the flight crew to actively deploy or retract them,” Lutters says. The experimental VGs are mounted close to the wing’s leading edge in a section dubbed the piano panel, where they can be filmed from a camera mounted in the cabin.
All the other technologies to be tested in the upcoming campaign are inside the aircraft’s cabin, cargo holds or flight deck. The 777 will continue a long campaign of testing new fire-extinguishing agents intended to replace ozone-depleting Halon 1301, which is no longer being produced. Although non-Halon solutions have been found for cabins and lavatories, the industry is still forced to recycle Halon until effective replacements can be developed for the unique challenges of fire suppression at altitude in engines, auxiliary power units and the cargo hold.
The latest efforts build on tests from 2019 of a new blend of bromotrifluoropropene (2-BTP) developed by fire-suppression specialist Meggitt, which showed promise for use in cargo holds. Tests on an Alaska Airlines 737-9 in 2021 evaluated an agent dubbed CF3i (iodotrifluoromethane) for extinguishing engine-bay fires. In 2022, these tests are focused on the discharge performance of Meggitt’s 2-BTP agent—called Verdagent—for the cargo compartment.
“Testing will focus on the dispersion rate and how big an area it will go to and whether that compares to what we would see with typical Halon,” Lutters says. “There’s no fire or anything that we’re going to be testing—that’s all done in a controlled lab. But what we’re going to be testing in the cargo bay is really critical because we have a mandate that we need to adhere to [in order to] find a new type of agent by 2040.”
Meanwhile, last year’s tests of the CF3i point to the need for additional work. “We’re continuing our learnings,” Lutters says, adding that the exercise proved the value of the ecoDemonstrator. “I think it was really good that we tested [the Halon replacement candidate] on the airplane because we test in a real environment rather than in a lab. We are able to see how it actually performs.”
The program also will test several flight-deck technologies aimed at improving operational efficiency, including a system developed using Jeppesen airport maps that will enable optimized taxiing operations before takeoff and after landing. The Taxi Time Information and Taxi Clearance applications will be tested with electronic flight bags and use automatic dependent surveillance-broadcast positioning data and aircraft connectivity to estimate required taxi time. “It will give pilots and operations teams an idea of what’s really going on so they can choose to be on one engine,” Lutters says. It also will let them know that they have time to “spool up that engine before they take off,” she notes.
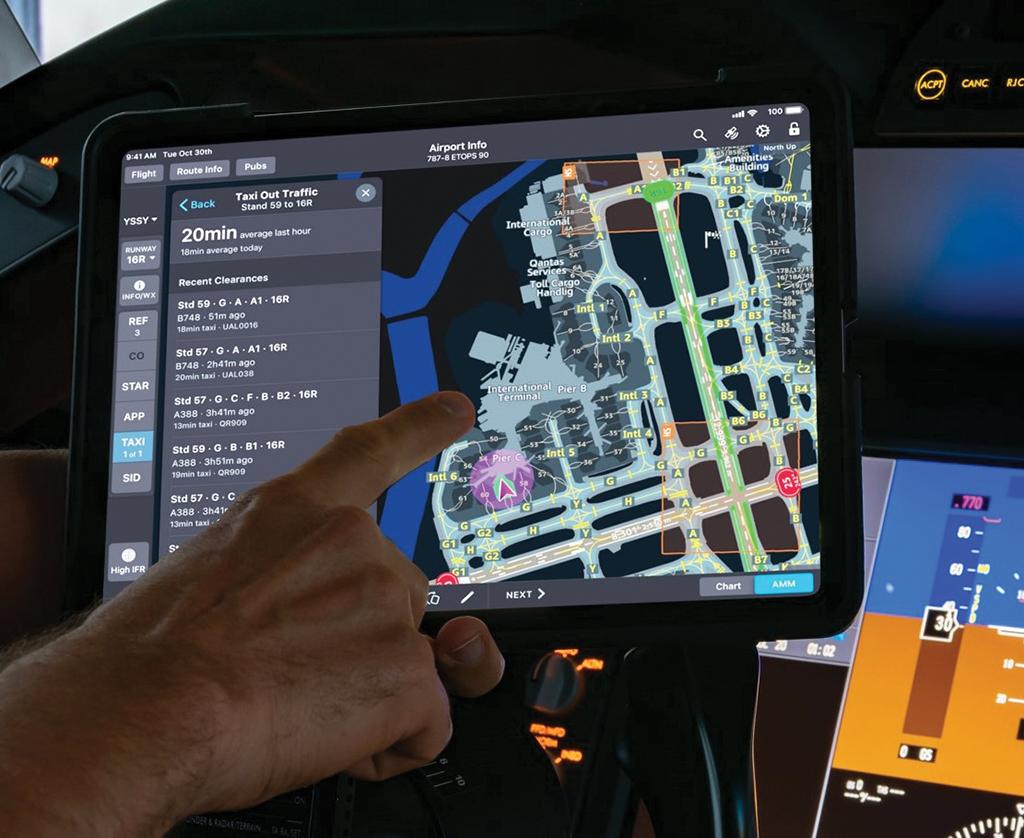
The next phase of ecoDemonstrator tests in 2023 are slated to evaluate a more advanced head-mounted portable enhanced vision system (EVS)—a version of which was initially tested in 2019. Developed by Universal Avionics, the SkyLens head-up display (HUD) system will integrate aircraft data with imagery from a nose-mounted camera. The EVS system is designed to provide improved situational awareness to the flight crew, particularly in low-visibility conditions, while saving the weight and complexity associated with conventional cockpit-mounted HUDs.
Technology tests in the cabin include a “gray” water recycling system that collects and filters washbasin water for later use in flushing toilets. Developed by Diehl Aviation, Boeing says the system has the potential to save around 50 gal. or more than 400 lb. of weight per flight. “This is a really cool concept,” Lutters says. “This apparatus will cycle through about every 10 min. during flight tests to represent average passenger use.”
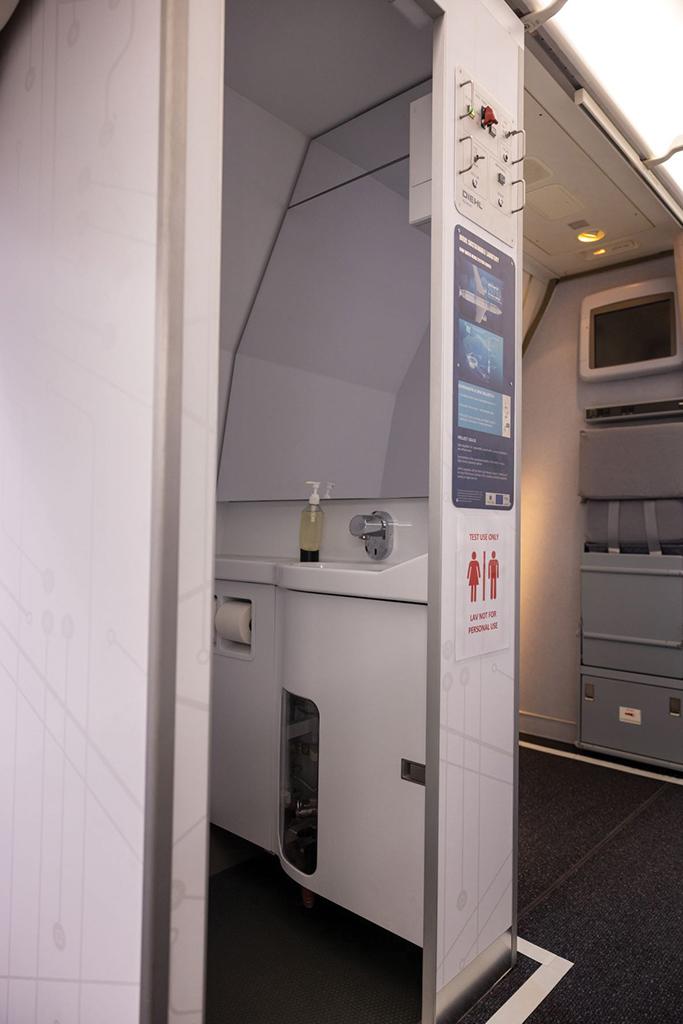
Another experimental toilet cubicle developed with interior specialist Jamco and Japan-based All Nippon Airlines incorporates a hands-free door opening-and-latching design, while a third lavatory unit—also developed in collaboration by Boeing and Jamco—will be used to evaluate an automated ultraviolet (UV) disinfecting system. UV irradiation deactivates viruses and kills bacterial organisms by destroying their DNA. “The idea is that after someone uses the restroom, they would exit, the door would shut, and a sensor would sense no one was in there,” Lutters says. “It would activate the system, go through its cycle, disinfect it, and then be ready for the next person.”
Other cabin technology tests include evaluation of UV cabin lights and a new air chiller in partnership with Collins Aerospace. The UV light, which for the tests is located in the galley of the 777, could be featured in cabin configurations to help disinfect them during turnarounds between flights. The new air chiller uses Opteon R-1234yf, an environmentally preferred refrigerant agent based on hydrofluoroolefin—a molecule that, if accidently released, has an average atmospheric lifetime of 11 days, compared with the roughly 12-year life of a typical hydrofluorocarbon-based refrigerant.
“It literally looks like something you would do in a high school laboratory, but we’re collecting data by putting thermocouples in bottled water in different areas [of the galley,]” Lutters says. “We’re going to be collecting data over time to see that it performs how we would expect it to and to see if it is similar to the ones that we currently utilize.”
Boeing also is using the ecoDemonstrator to test wider applications of additive manufacturing, including a part made from recycled aluminum, a complex engine bracket made from Inconel and an auxiliary power unit duct panel crafted from titanium—the largest Boeing-made additively manufactured part yet built and flown by the company.