
Life has never been so complicated, or promising, for engine-makers aiming to power more than 30,000 new single-aisle airliners that Airbus and Boeing forecast will be delivered over the next two decades.
Why is it complicated? The push to reduce fuel burn, emissions and noise still drives civil jet engine development, as it has over much of the past 70 years, but a wave of emerging technologies is changing how these goals might be achieved. Pathways to the future are quickly diverging from the familiar linear exploitation of bigger bypass and higher-pressure ratios into unknown territory.
- Electric and hybrid options add to the power puzzle
- Future focus: open rotor and gears
Spurred by urgent new sustainability targets, civil turbofan developers face a technology sea change and, consequently, are no longer relying solely on traditional aero-mechanical approaches to gaining greater propulsive and thermal efficiency. Instead, in addition to continuing to pursue advances in conventional gas turbine design, powerplant-makers are embracing a bewildering variety of new efficiency options, ranging from geared and open fans to smaller cores, hybrid-electric power, novel cycles, new materials and alternate fuels.
Uncertainty over how aircraft manufacturers will meet market demand in the next decade also adds to the engine-maker’s challenge. Beyond the next round of predictable midlife upgrades planned for CFM’s Leap 1 and Pratt & Whitney’s PW1000 geared turbofan (GTF) families in the mid-2020s, there are no clear signs yet about the aircraft that will replace today’s Airbus A320 and Boeing 737 workhorses. Even the likely thrust demands of future single-aisles are unknown. Will they fall within the familiar 25,000-35,000-lb.-thrust sweet spot of the past 50 years?
If so, how much of that thrust will be produced directly by the gas generator and how much—perhaps—will be augmented by alternative sources such as electric or hybrid-electric means? Will hydrogen fuel be a realistic factor for the next generation, either directly combusted gas or in a fuel cell?
Evidence of the range of new forces at play in the single-aisle propulsion sector was clear at the recent Farnborough International Airshow, where the overarching theme of sustainability once again dominated. General Electric and Safran joint venture CFM revealed an agreement with Airbus to flight-test on an A380 the open fan propulsion system being developed under the engine-maker’s Revolutionary Innovation for Sustainable Engines (RISE) program. Meanwhile, Pratt outlined key elements of a broad-based next-generation GTF technology plan to develop an engine with at least 10% better fuel efficiency over current engines by the end of the decade.
The new options facing the airframers also add to the puzzle. Particularly for the 2030s, by which time Airbus hopes to field the first of a family of zero-emission, hybrid-hydrogen-powered airliners under its ZEROe sustainable airliner plan. Boeing’s next-generation single-aisle plans remain more of an unknown, particularly as the manufacturer continues to weigh where to delineate the boundaries of the replacement gap between the 787 and today’s 737 family.
Despite these questions, lessons learned from the company’s Transonic Truss-Braced Wing (TTBW) research program—a candidate for NASA’s Sustainable Flight Demonstrator—are expected to play a key role in whatever replaces the 737—and the engines that will power it. The TTBW is “not science fiction,” says Mike Sinnett, vice president and general manager of product development for Boeing Commercial Airplanes. “We’ve been in the wind tunnel on that for 10 years, looking at that configuration. When I think about 2030-40, a configuration like that with advanced material and advanced propulsion systems could be 30% more efficient than what we have today, so we’re very bullish.”
But even if Boeing’s futuristic TTBW configuration is by now closely defined, questions over what will power it remain unanswered. Until now Boeing has shown the TTBW with generic turbofans but, for the first time, displayed at Farnborough a concept powered by a RISE-like open fan. Meanwhile, behind the scenes, the manufacturer quietly met with Pratt to discuss powering the potential NASA demonstrator with a version of the GTF.
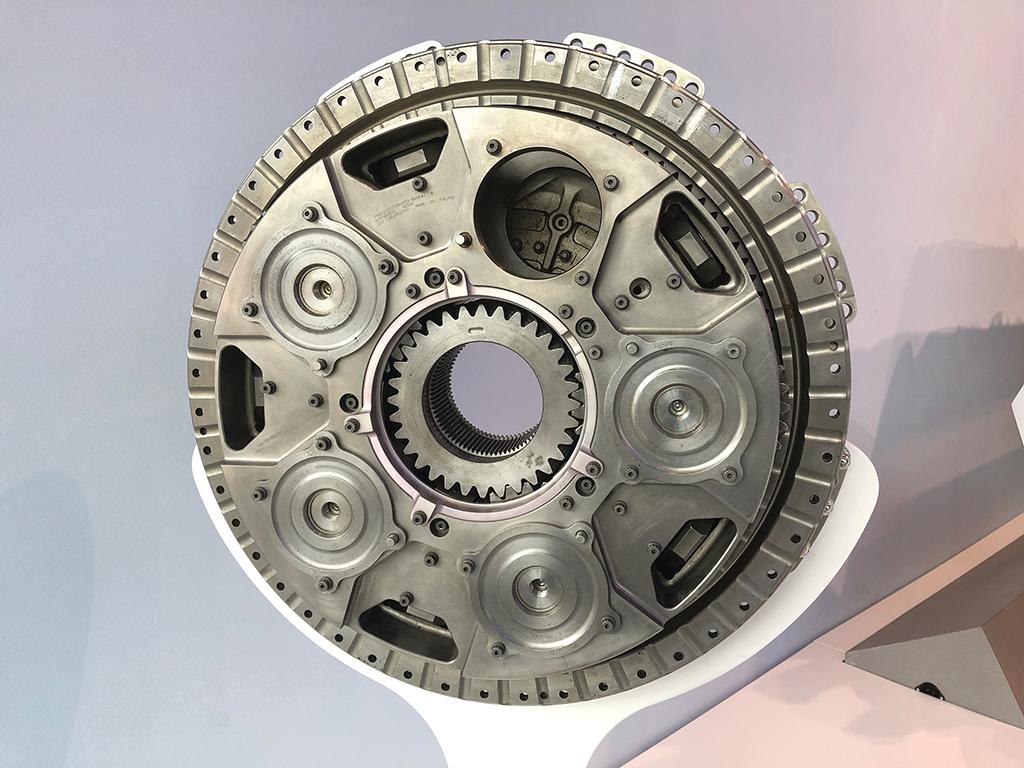
Until recently, Pratt has only discussed the potential evolution of the GTF in vague terms. But at Farnborough it outlined a development plan to carry the engine into the 2030s. The road map builds on a wide range of propulsive and thermodynamic efficiency improvements—many of which are already underway. Ultimately these options also include novel cycle adaptations based on more electric and hybrid power developments under study, both internally and with Pratt’s long-term partner in Germany, MTU.
These concepts include Pratt’s Hydrogen Steam-Injected Intercooled Turbine Engine concept, which is designed to exploit the full potential of hydrogen by going beyond its use as a fuel, to also maximize its cryogenic properties to lower emissions and improve thermodynamic performance. MTU is also studying the Water-Enhanced Turbofan (WET) to build on an improved version of the GTF by 2035. The WET engine adds a condenser to collect water from the GTF’s exhaust gas and a heat exchanger to vaporize the water into steam, which is injected into the combustor.
Pratt & Whitney Chief Sustainability Officer Graham Webb says that in the near term proposed propulsive efficiency improvements include plans to increase “the bypass ratio of the GTF engine beyond where we are today.” Fan diameter will be increased beyond the existing 81 in. to push the bypass ratio from the 12.5:1 of today’s GTF toward 14:1. “So we are working lightweight structures technologies,” he adds. “The composite fan blade is a key element of it as well as the composite fan case. We will also have to increase the fan-drive system gear ratio.”
The GTF family is currently configured with an aluminum and titanium fan, but the next-generation design will be based on a 3D-woven composite material. “That will enable us to hit those higher bypass ratios,” Webb says.
Although the focus is on bypass ratio, “The actual physical parameter of interest for us thermodynamically is fan pressure ratio, so we’re going to lower fan-pressure ratios,” Webb says. “We’ve demonstrated those in a recent program that was funded by the FAA [Continuous Lower-Energy, Emissions and Noise] program. That enabled us to demonstrate the ability to go to the lower fan-pressure ratios that we would require for the next generation of GTF engines.”
“We’ve also been working with funding from NASA on a variety of small-core technologies focusing on improving the compressor—the aerodynamic efficiency and the sealing of the compressor,” Webb says. “Also, we’re working on the turbine in a similar fashion. We’re advancing our cooling capabilities in the turbine using some advanced-core technologies that we’re going to first deploy with the Advantage engine,” he adds, referencing an upgraded PW1100G variant currently going through certification tests.
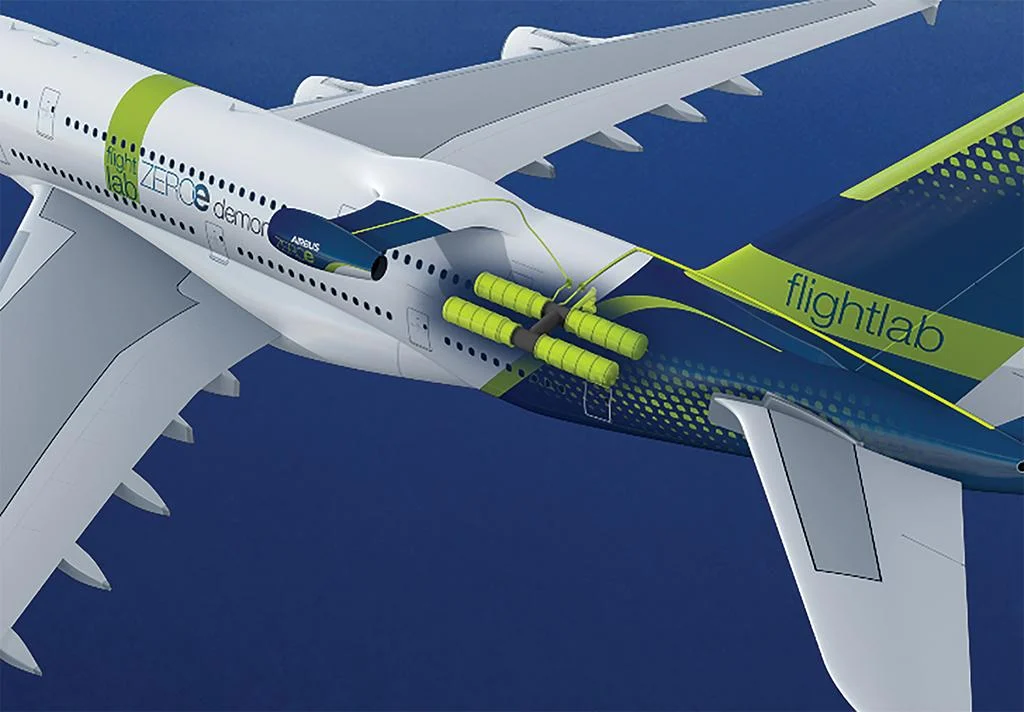
Major changes to the new standard, which will be introduced into service on the Airbus A320neo in 2024, include increased core airflow, particularly through aerodynamic modifications to the three-stage low-pressure compressor, which boosts available thrust and provides a 1% fuel-consumption benefit, Pratt says. In addition, the package rematches the flow with the turbines by changing the frontal area of the two-stage high-pressure turbine and the three-stage low-pressure turbine.
Key portions of the advanced-core improvement work centers on the use of ceramic matrix composites, the focus for which is taking place at a research and development center in Carlsbad, California. “That’s enabling us to actually produce airfoil components, which we’re now doing. We have some proprietary technology, in terms of the coatings that are required for that, that we’re also embodying, and we want to start doing the engine testing of that in 2025,” Webb adds.
CFM, which revealed the RISE technology plan in 2021, is not yet providing updates on specific tests, but points out that the initiative covers a broad swath of new technology beyond open fans. “We have more than 1,000 engineers who are working on 300 different tests across 150 test vehicles, rigs, modules, and later in the program, on full engines,” says CFM President and CEO Gael Meheust. “There’s a flow of optimism within CFM to see all the validation happening with these design solutions that we only imagined a few years back, and which are now progressively turning into reality. This is going to redefine the future of aviation propulsion.”
RISE is targeting a 20% reduction in fuel consumption and CO2 emissions compared with current single-aisle engines, and is aimed at the 20,000-35,000-lb.-thrust class. In addition to the 13-ft.-dia. blades of the open fan propulsor, the demonstrator will include a high-power transmission system and a new compact high-pressure core to boost thermodynamic efficiency. It will also include a recuperating system to preheat combustion air with waste heat from the exhaust. The demonstrator will also include a swath of advanced materials such as ceramic matrix composites in the hot section and resin-transfer-molded composite fan blades.
Hybrid-electric power for single-aisle engines is also under study by GE as part of a closely aligned effort with RISE. As part of these efforts, GE recently completed simulated altitude tests of a modified hybrid-electric CT7 turboprop in NASA’s Electric Aircraft Testbed facility in Sandusky, Ohio, under the agency’s Electrified Powertrain Flight Demonstration project.
Tests of the high-power, high-voltage system included two sets of electric motor/generators, power converters, power transmission and power control systems, and successfully demonstrated performance and operation of the components in a replicated flight environment up to 45,000 ft. As well as validating the baseline system architecture, the tests paved the way for hybrid-electric propulsion system flight tests with NASA later this decade.
Targeting entry into service in the mid-2030s, the technology is aimed at both commercial hybrid-electric turboprops for future regional transports as well as the mildly hybridized RISE turbofan family.