
The NRC’s converted Cessna 337G testbed is helping the Canadian aerospace industry develop and validate electrified propulsion systems.
Canada’s National Research Council is expanding work with its Cessna 337G Skymaster Hybrid-Electric Aircraft Propulsion Testbed into new areas under the nation’s recently launched Low-Emission Aviation Program.
Aimed at accelerating the Canadian aviation industry’s transition to net-zero carbon emissions, the Low-Emission Aviation Program (LEAP) is designed to position the country as a clean tech leader by derisking and speeding up development of high-impact technologies as well as fostering a collaborative low-emission aviation ecosystem.
- Emrax electric motor is in aft position
- Vehicle is powered by 84-kWh battery modules
The Hybrid-Electric Aircraft Propulsion Testbed (HEAT), which has its rear piston engine replaced with a high-power-density electric motor, a battery module and high-voltage electrical system, first flew in February and is intended to develop know-how to help the Canadian aerospace industry develop and validate electrified propulsion systems. The data gathered by the National Research Council (NRC) is being shared with aviation regulator Transport Canada to inform certification criteria for future electric and hybrid aircraft.
Work on the HEAT testbed is contributing to three of four “master” projects under LEAP that cover aircraft technology integration, electrical systems and battery safety. Future planned studies also include further potential modification of the “push-pull” Cessna to include a hydrogen fuel cell. This would enable it to contribute to the fourth key project, which is evaluating various technologies associated with hydrogen-related safety, storage and combustion challenges.
Like other hybrid propulsion development programs, including VoltAero in France and U.S. startup Ampaire, the NRC selected the twin-boom, twin-engine Cessna 337G because its centerline-thrust propulsion configuration makes it easier to replace one of the aircraft’s two piston engines with an electric motor while retaining the other for safety.
The modification involved removing the rear seats, the 400-lb. rear piston engine and its two-blade propeller and replacing them with 16 battery modules collectively weighing over 1,000 lb. The batteries were incorporated into an 18g crashworthy support structure along with a 210-kw-max (282-hp) continuous-rated Emrax 348 electric motor. Both the front and rear engines were refitted with three-blade propellers, the rear unit being electrically actuated.
The battery modules collectively contain more than 84 kWh of energy. “It’s an 800-volt battery, so higher voltage than some of the other small retrofits that we’ve seen so far,” says Natesa MacRae, NRC Control system engineer. “In terms of containment, instead of preventing thermal runaway propagation from cell to cell, because these were off-the-shelf modules, we actually had to do our own containment at the module level.”
Although the NRC declines to specify details of the materials in the containment system, MacRae says that after several versions were tested to failure in a newly developed battery performance and abuse laboratory the final configuration enabled full containment of a thermal runaway far in excess of the research group’s 5-min. goal. “Any thermal runaway gases that are emitted from the cells are vented up the back safely away from the pilots,” she says. “The containment system was fire-tested, destructively tested and pressure-tested. We did every possible thing to make sure that the pilots were going to be safe.”
As well as basic functional test flights and a recent noise test in Ottawa, Ontario, involving characterization overflights using only electricity to power an acoustic array, the HEAT testbed has also been involved in preliminary tests related to the dynamic aeroelastic stability phenomenon of whirl flutter. First recognized as the cause of disastrous accidents to Lockheed L-188 Electra aircraft in 1959-60, whirl flutter is driven by motion-induced unsteady aerodynamic propeller forces and moments acting on the propeller plane.
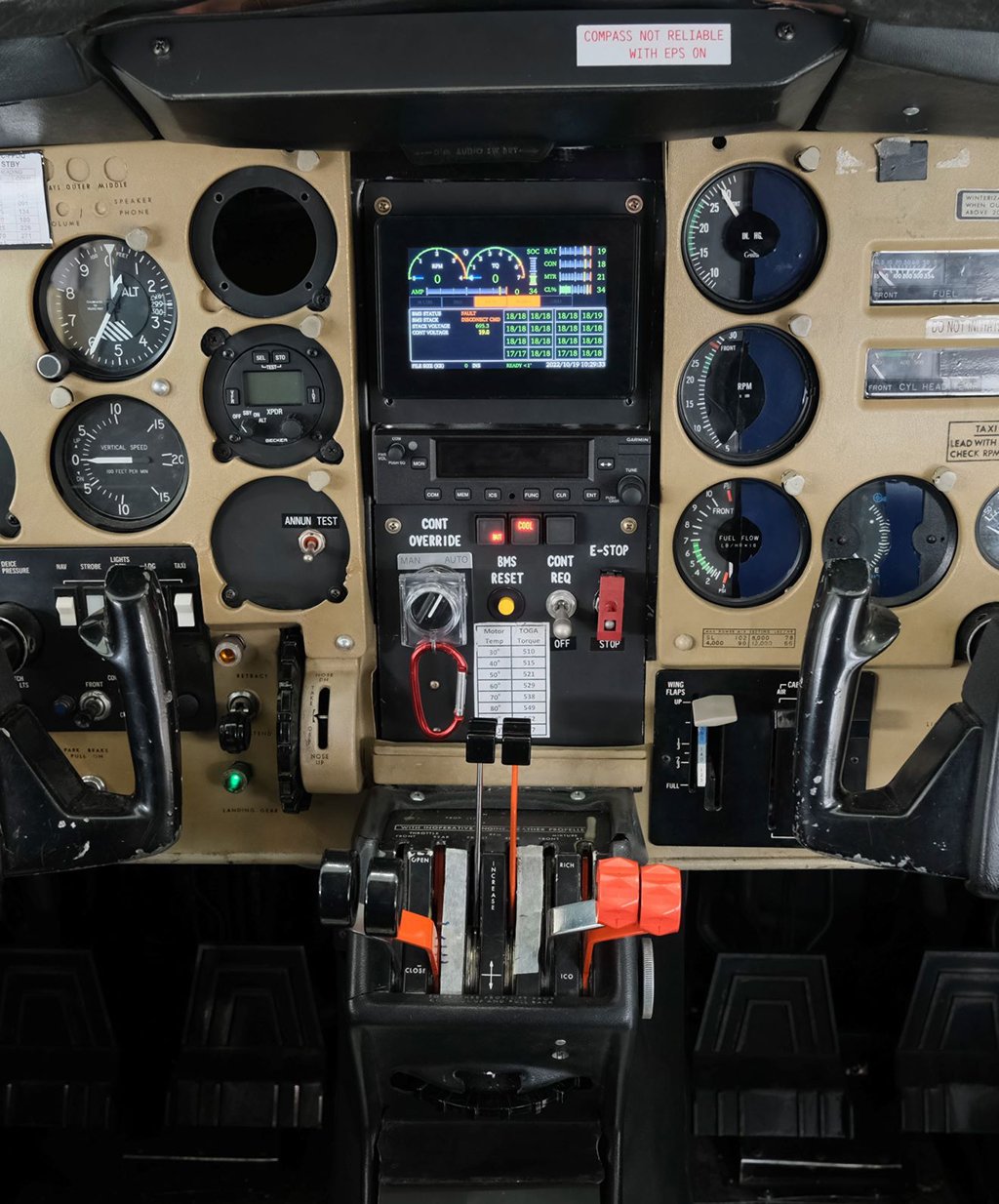
With the potential to cause unstable vibration, which can lead to failure of an engine installation or an entire wing, the issue could be of particular concern to the emerging generation of multimotor, tiltrotor electric vertical-takeoff-and-landing aircraft.
“When we took out the combustion engine, we put in a big mass in a cantilever. So, there’s all kinds of interesting modes that you have to look at here,” says Alex Crain, an NRC research officer who is the HEAT technical lead. “One of the flights that we’re doing now is for whirl mode, as that was something Transport Canada raised relatively early on.”
Rather than risk the safety of the testbed and its crew, the flights approached—but never went beyond—Vne (velocity never exceed) speed and collected accelerometer data for validation of whirl flutter mode models created by NRC researchers. “We’re currently building a second instance of this motor mount, and we will put that with the same motor and prop in the 3 X 6-m (10 X 20-ft.) wind tunnel here at Ottawa,” says Patrick Zdunich, principal research officer for HEAT.
“We will soften the elastomeric mounts to bring the whirl mode boundary to a lower speed, and we will creep up to the whirl node in the wind tunnel, where we’re not putting people at risk,” Zdunich says. The work, which is aimed at further validation of the whirl flutter mode model “may prove to be interesting to the electric community.”
The modified cockpit was designed to keep the controls as common as possible, says Reagh Sherwood, HEAT test pilot. “The rear throttle is modified to set the torque for the rear motor through a rheostat instead of a standard linkage,” he adds. “Similarly, the front propeller governor is hydraulically linked while the rear propeller governor is controlled via a rheostat. Idle cutoff disengages the rear motor.
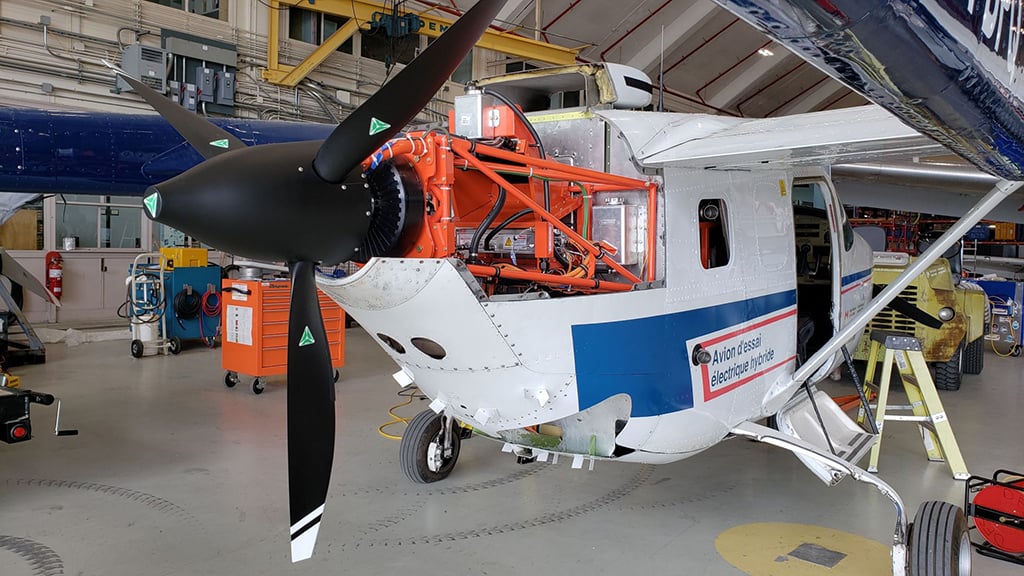
“If we have a failure, then it’s got a manual switch, which my flight-test engineer holds down for the 90 sec. it takes to feather,” he notes. “Obviously, if we had wing-mounted engines that would be much more of a concern.”
For monitoring and operating the electric motor, the NRC developed a special touch-screen display. Any engine rpm exceedance is indicated in yellow or red, while the state of the battery charge is shown in green, changing to red if it drops to zero. “We set the torque much like a turboprop with a set number while power rating is almost analogous to fuel flow—the amperage we’re drawing out of the back end,” Sherwood says.
A big question facing all-electric aircraft programs is how best to indicate to the pilot the remaining range available. “That’s the next change,” Sherwood says. “Right now, we have this state of charge in percentage, and I’m leaning more toward putting that as either kWh remaining or amps per hour. So if I’ve got 120 amps and I’m burning 240 amps, then that’s half an hour remaining. We haven’t gotten there yet, but that’s the way we’re leaning.”
The status page on the bottom of the display indicates the highest and lowest temperatures in each of the battery modules. Although individual modules cannot be disabled, the temperature reading enables overall troubleshooting. “If they’re all hot, I’ve been using the system hard and maybe then I’d just bring the power back,” Sherwood says. “But if I got one of them hot and it’s still getting hotter, then maybe I’ve got a damaged battery. So you’d want to think about shutting it down. I might climb and get myself back to gliding distance.”
The power response is very quick, he adds.
“I did some throttle slams early on to check some of the safety interlocks,” Sherwood says. “We’re controlling the rear propeller rpm with the governor, but the motor controller also has an overspeed protection, which is similar to what the Pratt & Whitney Canada PT6 has. The PT6 will cut the power and cut the fuel, and if we overspeed it cuts the torque to the motor. We started artificially low, and I was absolutely abusive on this lever. And we watched as the propeller tried to govern and the motor came around and made sure that we weren’t going to damage anything.”