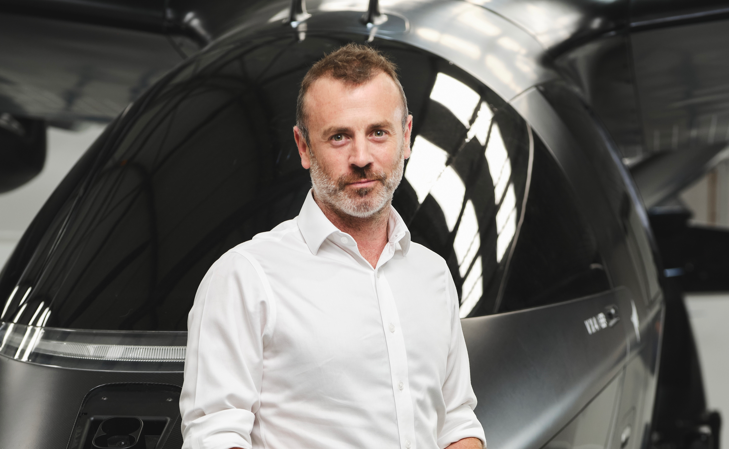
Stephen Fitzpatrick is founder and CEO of Vertical Aerospace.
Vertical Aerospace is a Bristol, UK-based startup seeking to certify a piloted, four-passenger electric-vertical-takeoff-and-landing (eVTOL) vehicle with the UK Civil Aviation Administration (CAA). Stephen Fitzpatrick, the company’s founder and CEO, recently sat down with the AAM Report to share his thoughts about the VX4 program and the rapidly evolving advanced air mobility (AAM) sector. A partial transcript follows:
AAM Report: Unlike other eVTOL startups, Vertical Aerospace has insisted on flight testing with piloted, full-scale prototypes from the onset of its certification efforts. What is the rationale behind this approach to testing?
Fitzpatrick: When we were in the early stages of exploring the unpiloted or remotely piloted prototype, we began to analyze the increase in weight that would come from building a survivable cockpit and crash structure, adding extra flight test instrumentation, and other piloted systems. And what we found was that the weight increase when moving to a piloted version was so substantial that it really became an entirely different aircraft with different handling characteristics and different power requirements. We found the form factor–the ideal aircraft–was very different in a certification context than it was as a prototype, so we thought it was a bit pointless building an unpiloted or remotely piloted aircraft that didn’t reflect the aircraft we actually needed to build to certify.
The company recently pushed back its certification target date to late 2026 from 2025 previously. Do you expect to see more delays announced across the AAM sector?
I do. In theory, electric aircraft should inherently be safer and easier to certify than a turbine-powered aircraft where there’s so many critical parts and single-point failures. However, this is novel technology and, in our experience, regulators and authorities don’t like to feel rushed. We expect other advanced air mobility businesses to start to see the challenges in bringing together their supply chains in such a short time. You can have just a few technologies that perhaps fall a bit behind schedule, and before you know it, the whole timeline is slipping. I think that as the deadlines start to loom very close on the horizon, we’ll see more delays across the industry.
When will Vertical have to raise more money? And why is it burning cash at a slower pace than most other leading eVTOL startups?
We will have to go and raise more sometime in the next 12 months. The burn rate that you mentioned is very interesting. I think it goes back to our early conviction that this journey would take longer than many other people thought. So we wanted to set up this model where we are sharing the risks of certification, production and technology development with our partners. Rather than doing everything in-house ourselves, we are working with some of the world’s largest aerospace companies, and in so doing, it reduces our risk and reduces our CapEx and OpEx. It leverages their capabilities and delivers us a lower-risk path to certification. Of course, there are benefits to vertical integration, but we think our model is the smarter way to do it because we require much less capital to bring a product to market.
But you are developing your own battery packs in-house at the Vertical Energy Center. What is the reason for that?
We have a partnership with a Taiwanese company, Molicel, on the battery cells, and they are a world leader in high-power performance cells. But the battery pack design is something that is almost unique for every airplane depending on the mission characteristics you want to fly. What we found early on was that in other areas—whether it’s structures, cockpit avionics, flight control software, actuators, motors, and so on—there were many other companies we could go to that had certified aircraft parts, production capacity, and were already doing an amazing job. But we didn’t find anyone in the aerospace world that was further ahead than we were in our own independent thinking around batteries. And so, because it’s such a novel area, we decided that rather than partner with someone else, the battery packs were something that we needed to develop our own capabilities on.
What are your thoughts on hybrid architecture? Have you considered moving to hybrid to improve the aircraft’s performance?
Yes, it’s something we’ve been working on for some time. Four years ago, we were already testing the jet turbine battery-hybrid system. I think that hybrid is definitely going to have a big impact. It’s going to take the useful range of our aircraft from 100 miles to 200 miles-plus. And whether that’s a turbine piston engine or a hydrogen fuel-cell hybrid, we’ve got lots of different opportunities. But the first step in all of that is the electrification of the powertrain. We think there’s enough novel technology to certify in the battery system and electric propulsion units without the additional complexity of the hybrid. So, the VX4 will be battery-only first, and then hybrid will follow. It doesn’t need to be a big delay; it could be three to four years post-certification of the battery-only variant that we see hybrids on the market.
What are your thoughts on finding a realistic production rate for eVTOL aircraft?
We’re expecting an explosion of demand for our aircraft all over the world as soon as it’s certified. But we also understand that it will take time for the other parts of the ecosystem to catch up, whether that’s passenger demand, local permitting, airspace management, air traffic control, infrastructure, and the like. We’ve designed our company around existing technology, regulations and infrastructure, and we’re expecting a relatively slower ramp-up in terms of our production. We’re not planning to go full tilt to building thousands of eVTOLs a year in year one. We don’t think it’s necessary or even realistic to go from zero to very high production rates unless you do that over a period of time.
You’ve said before that you think UAM aircraft should be certified to the same safety standards as commercial airliners.
I think it’s difficult to make the case that we should be adopting a lower safety standard just because it’s new. If this was an experimental aircraft category that was likely to be flying over rural areas, you could make the case that we should prioritize innovation over safety. But, we’re talking about urban air mobility—flying over schools and hospitals and homes—and I just can’t imagine that we end up doing that all with a lower safety rating. We can see already there’s a widespread call for convergence around safety standards across Europe and the U.S. And I think it’s really critical for the success of the industry to see agreement on what the appropriate level of safety is. And for our company, at least, because our aircraft are going to be flying over urban areas and people, we feel we need to certify to the very highest safety standards of commercial aircraft.