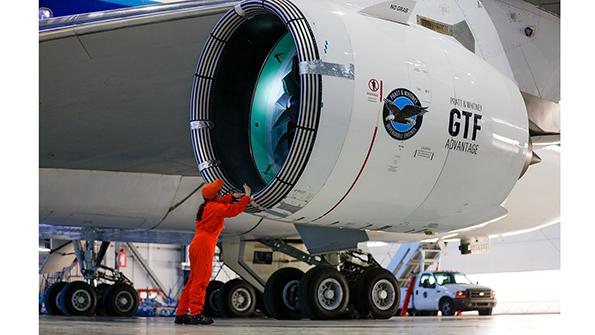
Seventy years after playing a leading role in the use of water injection to boost the power of early jet engines, Pratt & Whitney is revisiting an updated version of the idea as part of a high-efficiency, hydrogen-fueled turbine engine study.
The Hydrogen Steam-Injected, Intercooled Turbine Engine (HySIITE) concept is designed to exploit the full potential of hydrogen by going beyond its use as a fuel to also maximize its cryogenic properties to lower emissions and improve thermodynamic performance.
- ARPA-E work will focus on heat exchanger designs
- Water byproduct is key to combined-cycle concept
Supported by $3.8 million in funding from the U.S. Energy Department’s Advanced Research Projects Agency–Energy (ARPA-E), the initial two-year study will focus on integrated system evaluation, notional component design and component feasibility tests. Pending successful completion of this phase, Pratt says HySIITE could be tested in an accelerated ground demonstration as a potential follow-on program, possibly targeting development of an engine for commercial service in the mid-2030s.
“We’re really bullish on this right now. What we’re seeing is up to 35% improvement in mission energy over today’s geared turbofan engines,” says Michael Winter, senior fellow for advanced technology at Pratt & Whitney. “It works because you can take advantage of things like the additional water [produced as a byproduct of hydrogen combustion] in the exhaust, and because you have this huge cold source [from the cryogenic fuel]. It’s an integrated system that allows us to bring forward this entire cycle.”
Pratt also says the concept solves several potential problems associated with converting gas turbines to run on hydrogen. These include the challenges of integrating the cryogenic liquid at -253C (-423F) into engine fuel systems, preheating the fuel prior to injection and excessive production of nitrogen oxides (NOx)—a greenhouse gas that forms at hydrogen’s higher combustion temperatures. In addition, burning hydrogen produces 2.6 times more water vapor on an equivalent thrust basis compared with jet fuel, a factor that could contribute to significant contrail formation.
“We looked at those concerns and issues and said, maybe there’s an opportunity here. What if we take all of this and turn it into a solution?” Winter says. The proposed HySIITE cycle therefore integrates a hydrogen-fueled gas turbine with a steam-injection-and-recovery system. Some of the water generated by hydrogen combustion is collected in the exhaust and condensed in a heat exchanger, which simultaneously warms the hydrogen fuel prior to its injection into the combustor.
The liquid water from the condenser is fed into an evaporator that turns it into steam. This is then split, with some steam injected into the combustor and some fed into an intercooler upstream-—most likely interposed between the low- and high-pressure compressors.
“Everybody knows that on stationary gas turbine engines one of the ways to abate NOx production is to introduce water somewhere upstream of the combustor, and different companies do it in different places,” Winter says. “We also saw the whole enthalpy balance in warming up the fuel by condensing some of the water in the back of the engine. Finally, we also have known—going all the way back to the B-52—that if you fog the inlets by putting water vapor upstream you get more thrust out of the engine.”
“This is essentially a combined cycle with a steam-bottoming cycle on it, where we evaporate the water in the evaporator,” says Brent Staubach, associate director for advanced concepts and innovation at Pratt & Whitney. “That recovers the waste heat as steam, which then gets injected into the burner. The water comes from condensing water out of the exhaust. So that condensing heat exchanger is a critical piece of the technology.”
Under the ARPA-E project, Pratt will focus on several key enabling technologies as well as researching the complex gas dynamics and combustion stability issues associated with gaseous hydrogen and steam injection. In particular, the work will look at designs for practical evaporators, condensers and related heat exchanger configurations. “Can we make those heat exchangers small so they will fly in an airplane? So it is about getting the volumes and the flight weight characteristics down,” says Staubach, who adds that additional studies will focus on integrating the elements into a working system.
“This program is initially focused on the system-level analysis and the risk reduction of a number of the key components. If we were successful, we would look for mechanisms to continue the technology maturation,” Winter says. “We welcome public-private partnerships to accelerate the insertion of this technology into making it available in advance of hydrogen being a potential solution and available on the platform.”
Comments