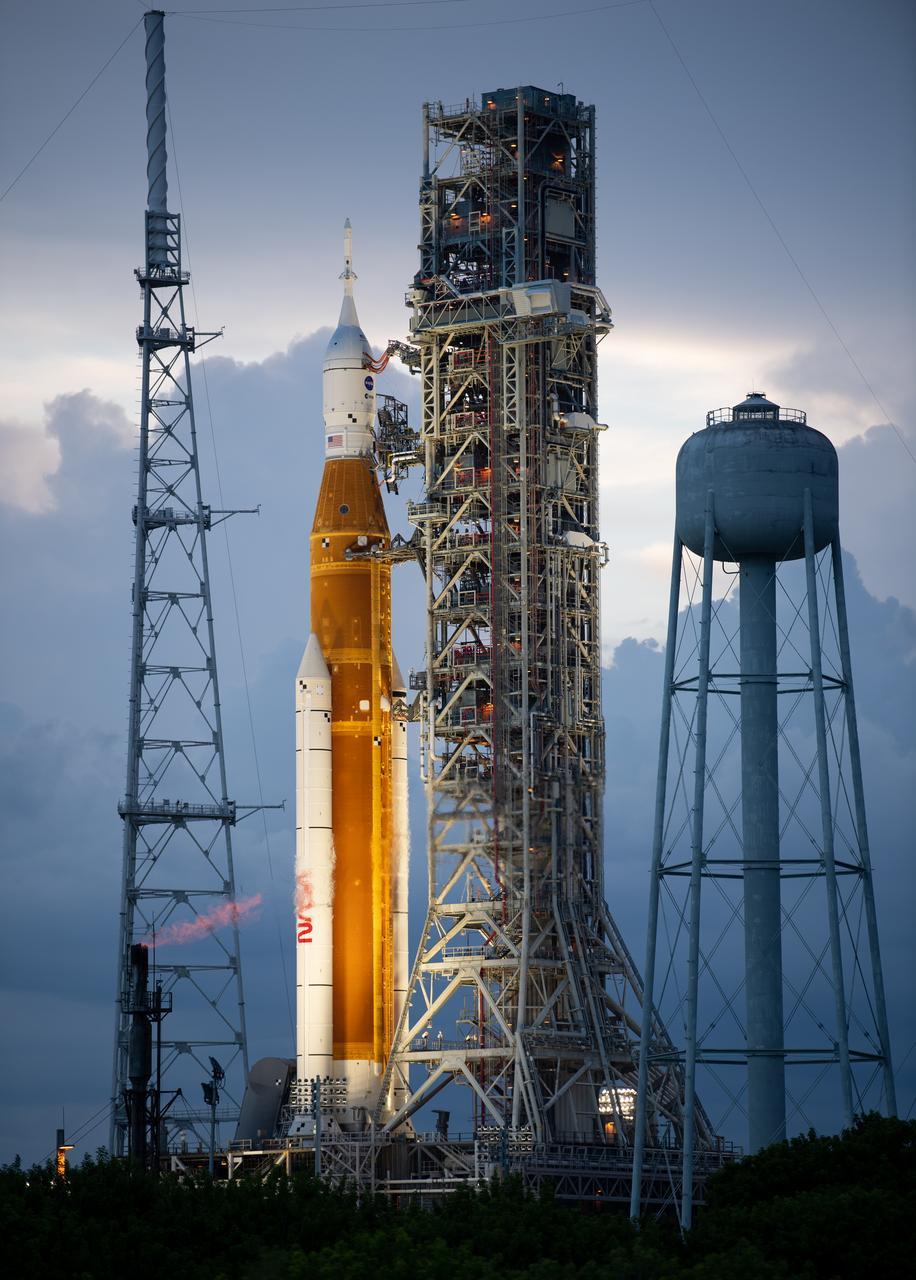
CAPE CANAVERAL—NASA decided late Sept. 6 to repair a hydrogen leak that scuttled its last attempt to launch the Space Launch System (SLS) rocket at the launchpad, then retest the line under cryogenic conditions.
Conducting the repair at Kennedy Space Center Launch Complex 39B could pave the way for a launch attempt later this month if the U.S. Space Force extends the 25-day certification for the SLS flight termination system. The certification expired on Sept. 6.
Without Space Force approval, the SLS will be returned to the Vehicle Assembly Building (VAB) so the flight termination system batteries can be retested and possibly replaced. A return to the VAB also is possible if staunching the hydrogen leak requires more extensive repairs.
NASA tried on Aug. 29 and again on Sept. 3 to launch the SLS, which carries an uncrewed Orion capsule, on the Artemis I flight test around the Moon. The first attempt was halted by a bad sensor that relayed incorrect data about the temperature of one of the four SLS core stage Aerojet Rocketdyne RS-25 engines.
Complicating efforts to troubleshoot the temperature issue was a hydrogen leak from a valve used to vent propellant from the core stage intertank. Given this problem, combined with a deteriorating weather outlook, the launch team ran out of time to vet the issues before the two-hour launch window closed.
After making a decision to bypass the bad sensor, NASA tried again on Sept. 3 to send the SLS on its inaugural flight, but scrubbed the countdown three hours before liftoff due to a large hydrogen leak in an 8-in. quick-disconnect fitting between the liquid hydrogen fuel feed line on the mobile launcher and the SLS.
NASA is investigating if a manual error that inadvertently commanded the wrong valve to open, momentarily over-pressurizing the liquid hydrogen feed line prior to the start of tanking on Sept. 3, was the cause of the leak.
“There was a sequence of about a dozen commands that were required and it was simply the wrong valve was commanded. It was identified after about 3-4 seconds and then it was rectified,”Artemis Mission Manager Mike Sarafin told reporters after the scrub. “We had planned [to reach] about 20 psi and it got up to about 60 psi. The flight hardware itself we know is fine—we did not exceed the maximum design pressure—but there’s a chance that the seal in the 8-in. quick disconnect saw some effects from that.
“We want to be deliberate and careful about drawing conclusions, because correlation does not equal causation,” Sarafin noted.
Replacing the quick-disconnect seal at the launchpad will require technicians to first set up an enclosure to protect the hardware from the weather and other environmental conditions. Once the seal is replaced, NASA plans to test the repair under cryogenic conditions.