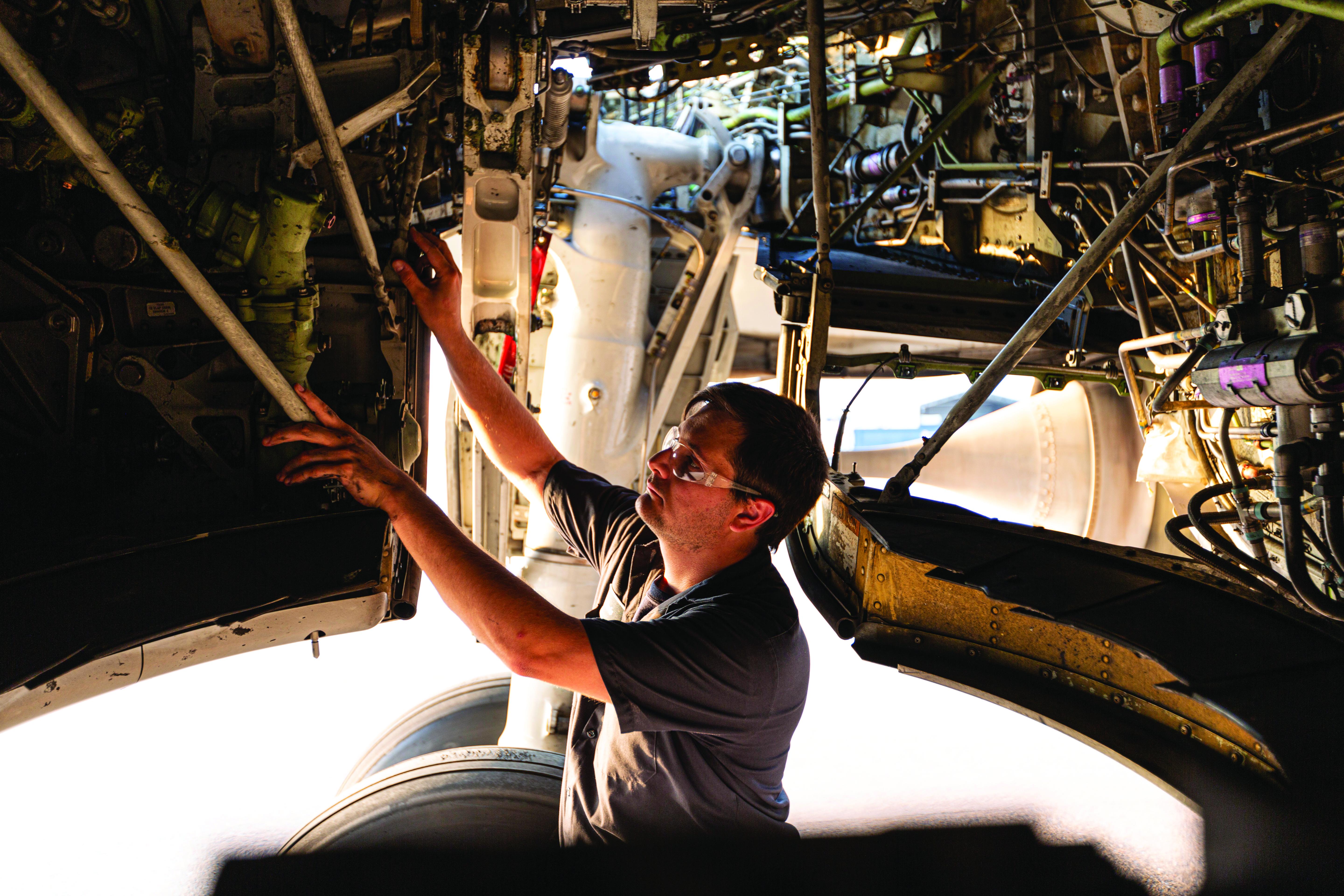
Future histories of the aircraft MRO sector will probably cite as a pivotal moment the ongoing novel coronavirus crisis—and the changes its aftermath will force upon the industry. Yet writers of those histories would also do well to reflect on the factors that have shaped the aftermarket up to this point, some of which are now an entrenched part of its dynamics and some whose influence is only starting to play out.
From the 1990s and into the 2000s, the MRO sectors of successive regions had to adapt to the huge upheaval in the airline business caused by the rise of low-cost carriers (LCC). Lean, efficient and operating at aircraft utilization rates that had been unheard before that point, these new players were willing to outsource much or all of their maintenance. At the same time, they demanded stiff discounts and rapid turnarounds for fleet-wide support deals.
Pricing pressure was significant enough to cause a reconsideration of operations at SR Technics (which in the mid-1990s was the technical department of Swissair), recalls Jakob Straub, senior vice president of aircraft services, line maintenance and training services at SR Technics. “Some of our base maintenance activities were moved to Ireland, and we also had to offshore part of our services to low-cost countries, primarily to the [Asia-Pacific] region,” he says.
Adapting to the new market demand also meant big changes to standard maintenance procedures.
“I remember when one of the new LCCs was entering the market and tendering their line and light maintenance services, they were asking for zero downtime in order to not cut out any operating hours,” recalls Robert Gaag, Lufthansa Technik senior vice president of sales for Europe, the Middle East and Africa. “We thought, ‘These guys are nuts!’ But when you think about it, you can use all the time at night for maintenance, just not during the day. So you can design a maintenance program around it. Of course, today, that is standard practice in the industry.”
Added Flexibility
Driven by the aircraft availability requirements of LCCs, aircraft maintenance programs drifted away from traditional letter-check intervals toward a more flexible approach endorsed by aircraft manufacturers. Thus, some elements of a traditional C check were incorporated into a work package equivalent to an overnight A check.
“We went away from letter checks and introduced a usage-parameter-based maintenance program, which allows a lot of flexibility in how you structure and schedule your maintenance,” says Bert Stegerer, head of maintenance and commonality marketing for Airbus. “You can optimize it for maintenance cost or for aircraft availability, so you can influence either the cost side or the revenue side.”
At the same time, the OEMs sought to extend maintenance intervals and eliminate unnecessary tasks without compromising safety. These efforts have resulted in huge changes to maintenance scheduling over the past 25 years or so. For example, Airbus A320 A check intervals have gone from 350 hr. at entry into service to 1,000 hr. for the equivalent check today, while C check intervals have gone from 15 months to 36.
The effects upon MRO were not just felt from the LCCs themselves: Network carriers were forced to rethink their operations to compete, and often this meant a reduction of in-house maintenance capacity and the outsourcing of maintenance tasks such as engine overhauls and widebody heavy checks. Together with the rapid growth in the commercial aviation sector caused by LCCs, this resulted in a booming third-party MRO market.
“Growth of the global aircraft fleet and enlightenment among carriers to outsource their maintenance needs over the past two decades are [among] the key trends I have seen impacting the industry,” says ST Engineering President Lim Serh Ghee.
Gaag notes that today’s airlines have a mature, deep MRO market to which to outsource, but 25 years ago not all aftermarket incumbents had the scale to respond to the burgeoning opportunities for third-party work, paving the way for extensive consolidation over the following decades.
“Major airlines want to have major players behind them,” notes Brian Loomer, vice president and general manager of aircraft services at AAR. “In the ’90s, there were a lot of small private MROs providing services, and they have been bought up by large corporations delivering a much better service.”
Engine Maintenance
The last 25 years have also seen a thorough transformation of the engine maintenance business, as product design, materials, OEM strategy and data analysis have coalesced into a unique ecosystem that almost operates on a standalone basis within the aftermarket.
By and large, airlines have seen the reliability of engines shoot up. CFM says that time on wing for CFM56 engines has doubled since 2004, while unscheduled engine removals for the most popular -5B and -7B models have declined by 25%.
“The improvements in time on wing, coupled with thoughtfully designed and managed [life-limited part] lives, have enabled scheduled maintenance event timing to be pushed out, resulting in fewer shop visits over the life of the asset,” says Aileen Barton, CFM marketing manager.
Widebody engine reliability has also improved, but unlike for narrowbody engines, this trend was accompanied by a reduction in maintenance provider choice as OEMs took over much of the aftermarket. This model, pursued most aggressively by Rolls-Royce, has driven further consolidation as MRO providers and airlines pursue OEM partnerships as the most economical method of adding new engine capabilities.
“For new-technology engines, you have to somehow cooperate with the OEM, or you are out,” says Gaag.
CFM argues that this is not the case universally and that it remains committed to an open maintenance model that respects third-party providers.
“When there are competing MROs, such as in the CFM model, it drives not only lower maintenance cost but also improvements on intangibles, such as service quality, slot availability and ease of doing business or customer service,” says Barton.
That said, it is undeniable that in recent decades, manufacturers of a range of aircraft components have emerged as significant competitors to MRO providers. “Competition was less [25 years ago], as nowadays the after-sales market has become attractive to the OEMs, which tend to regulate the spare-parts market with high parts prices and the proprietary rights with licence and royalty fees,” says Straub.
“In 1995, the airframe manufacturers were clearly focusing on building airplanes,” Gaag says. “Now they are getting in the turf of MROs. On the other hand, system OEMs are getting more independent from airframe OEMs. So there are more selected partnerships between MROs and system OEMs possible.”
Risk Transfer
For engine and aircraft support, consolidation among MRO providers and more outsourcing by airlines were allied to the growth of full-service maintenance deals and a reduction of time-and-materials contracts in favor of support billed according to equipment use—on a dollar-per-flight-hour basis.
For airlines increasingly focused on their core operations of transporting passengers, simplicity was vital. As such, many preferred to outsource maintenance to a single company rather than manage numerous providers, a trend that has endured. “Many smaller MROs have been bought up, as you need to be able to offer a one-stop-shop solution for the current customers,” says Loomer.
At the same time—starting in the mid-1990s—OEMs such as Rolls-Royce were pioneering full-service contracts billed on a per-flight-hour basis, the popularity of which boomed as they transferred the risk of unscheduled maintenance from operator to maintenance provider. And since the OEM was also the maintenance provider—at least in Rolls-Royce’s case—such contracts also incentivized it to improve the reliability of its products.
Per-flight-hour support deals were quickly picked up by other component OEMs, while MRO providers, encouraged by the trend toward better reliability, also started offering them, particularly for component support.
“We tend to think that Lufthansa Technik invented the [cost-per-flight-hour] program for full component support of a commercial aircraft fleet in the second part of the 1990s,” notes Gaag. “For the first time, a complete integration of all required spare and MRO services for all line replaceable units was established.”
Besides transferring risk, another attraction of comprehensive deals was guaranteed availability of spare parts. This was enabled by another big MRO trend of the last 25 years: a shift away from individual operators holding large inventories and toward participation in pooling programs.
Parts pooling is now a common feature of the engine and landing gear aftermarkets and is also used for other components, although its popularity varies, according to Gaag. “This was extremely successful in Europe but not so much in other parts of the world, for example in North America,” he says.
Other strategies to mitigate the cost of spare parts, prices of which have risen above inflation for many years, have included parts manufacturer approval (PMA) parts, designated engineering representative (DER) repairs and used serviceable material (USM). Although these are all important elements of the MRO story, it is possible that OEM maintenance contracts and lessor contracts have prevented PMA parts from proliferating as much as expected. USM, in contrast, has gone from strength to strength, although it is another also vulnerable to the COVID-19 crisis, which could flood the market with parts stripped from aircraft of failed airlines.
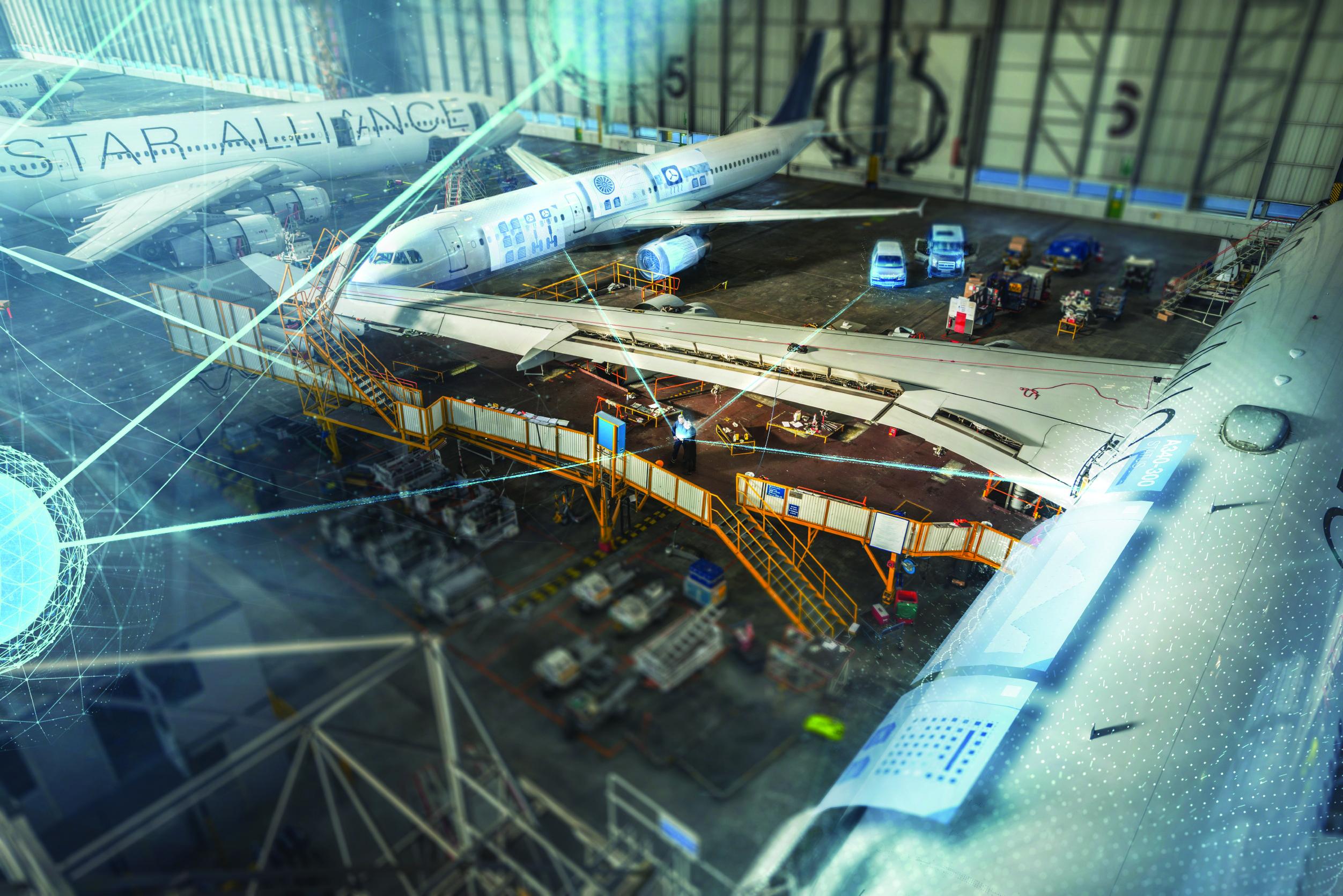
Technology
Maintenance exists to support equipment, so changes in airframe, avionics and engine technologies will always require adaptation from MRO providers. Often this means new tooling and training, but sometimes technological change is so profound that it leads to new business models as well.
Although the basic form of passenger aircraft has not changed much in the past 50 years, the use of carbon fiber has increased over the last 25 years as manufacturers sought weight savings across more parts of the airframe. In turn, MRO providers had to expand their expertise from metal repairs to support of composite materials, adding a host of new inspection, testing and repair processes.
“If you want to get into deep repairs, you need an autoclave of a certain size,” notes Gaag. “This is a very expensive investment that requires high utilization once you have it.”
At the same time, the spread of composites across aircraft has meant certain inspection tasks are no longer necessary, notably fatigue- and corrosion-monitoring on parts previously made from aluminum. Another technology change that has lightened maintenance workload is the shift to fly-by-wire controls and flight control computers.
“If you have a mechanical flight control system, then you have to adjust cables and check for wear and tear, but all that is gone if you use just electrical signals,” notes Stegerer.
Airlines also have benefited from better engine sensor data and vastly improved means to analyze it through machine learning and artificial intelligence, both of which have underpinned the rapidly growing field of predictive maintenance in the past 10 years. For airlines, this has meant fewer unscheduled maintenance events and less downtime, while MRO providers have been able to add new digital services to their product offerings.
“Analytics can be used to define the optimum inspection interval based on the duty cycle for each specific engine, with the goal of minimizing line maintenance and unnecessary inspections,” notes CFM’s Barton.
Predictive maintenance is part of a broader digitization trend that also encompasses a shift away from paper-based records; advances in 3D printing; automation of certain testing, inspections and repair procedures; and the first steps toward better parts and life-cycle tracking via experiments with distributed ledger technology. With the probable exception of predictive maintenance, few of these developments are mature enough to have significantly influenced MRO until now, but many are likely to do so in the coming decade, in some cases simply because the aircraft aftermarket lags so far behind other sectors.
“Why can an airline manager track the $10 book he ordered yesterday at any point in time, but not his $100,000 aircraft part to and from an MRO? We need to be better than that,” states Gaag.
Recruitment
While MRO providers look forward to efficiencies provided by new technology over the next decade, they also fear the growing shortage of technical staff. And since the maintenance business is likely to remain dependent on touch labor for the foreseeable future, the implications of this shortage are potentially far more significant than any gains realized from new technology.
“Recruitment really became an issue around 2015. Prior to that, it wasn’t a major concern,” says Loomer. “As the baby boomers started to retire and airlines at the same time started to hire more technical staff, it has had a major effect on the MROs. The industry has a major challenge looking forward, as we see a technician workforce shortage.”
Gaag speculates that aircraft MRO providers’ difficulties in attracting and retaining staff might have to do with a deromanticizing of the sector. “I have the feeling the profession of an aircraft mechanic does not have the same appreciation it had in Western societies 25 years ago. We are missing the aviation enthusiasts that we used to have,” he says.
Here again the influence of LCCs is detectable, for they transformed air travel from a small luxury into a mundane part of modern lifestyles, at least in the West. OEMs and MRO providers have tried to rekindle interest with outreach programs, educational partnerships and even their own dedicated training colleges, but more may be required.
“We have to become better at selecting sites not necessarily at the lowest-cost location but close to young people who are interested in aviation,” says Gaag. “And we have to do better to keep them.”
Another—unwelcome—solution to the manpower shortage is possible. Maintenance demand could collapse following the COVID-19 crisis if it causes many airlines to fail and the survivors to reduce their fleets. For that reason, MRO managers must hope that recruitment remains a concern in a year’s time.