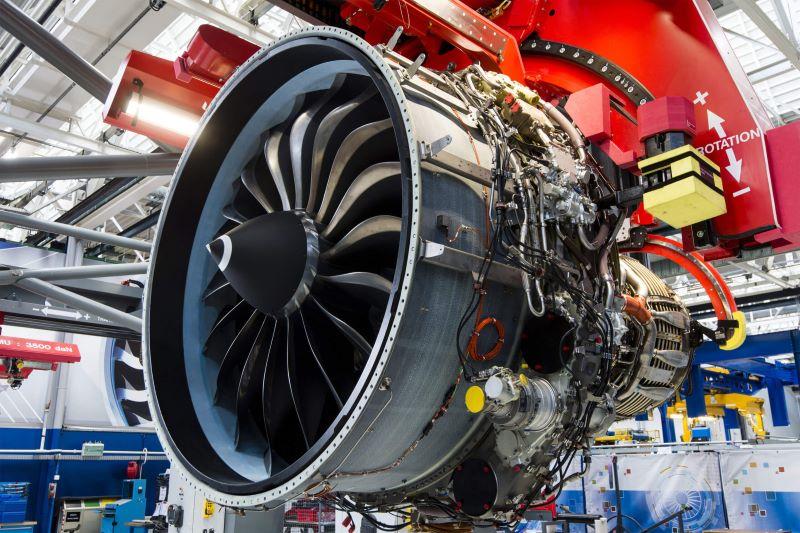
Credit: Philippe Stroppa Snecma / Safran
CHICAGO—CFM International has begun delivering Leap-1A new-production engines with its new reverse bleed system (RBS) designed to prevent a fuel nozzle problem linked to carbon deposits and expects to have retrofits available by mid-year. The problem, known as coking, occurs when core engine...
Subscription Required
CFM Delivering Leap-1As With Reverse Bleed System is published in Aviation Daily, an Aviation Week Intelligence Network (AWIN) Market Briefing and is included with your AWIN membership.
Already a member of AWIN or subscribe to Aviation Daily through your company? Login with your existing email and password
Not a member? Learn how to access the market intelligence and data you need to stay abreast of what's happening in the air transport community.