
Taiwan Semiconductor Manufacturing Co. makes more than 60% of the world’s semiconductors and over 90% of the most advanced chips.
The aerospace and defense industry has become highly dependent on semiconductors, the computing brains of modern electronics, which are integral to powering aircraft navigation, communication and control systems. But because the aerospace and defense market accounts for just a fraction of global semiconductor demand, those companies in need of specialized microchips find themselves at the tail end of a lengthy, fragile supply chain. If that supply ever were disrupted severely, the industry would face an unprecedented crisis.
“Defense systems use huge quantities of semiconductors, and though most of these chips can be built in the U.S., today some of the most advanced processors cannot,” Chris Miller, an economic historian at Tufts University and author of Chip War, a history of the semiconductor sector, tells Aviation Week.
- Chipmaking is highly concentrated in a few countries
- Aerospace’s small share of semiconductor demand limits its bargaining power and influence
While the semiconductor supply chain is global, both its crown jewels and niche capabilities are concentrated in just a handful of countries. Taiwan Semiconductor Manufacturing Co. (TSMC) makes more than 60% of the world’s semiconductors and over 90% of the most advanced chips. The Netherlands’ ASML is the sole manufacturer of the $200 million extreme ultraviolet lithography machines used to produce those cutting-edge chips. Japan has a near-monopoly on the specialty chemical photoresist used in photolithography and photoengraving of microchips. And the U.S. dominates semiconductor design with companies like Nvidia, Intel and Qualcomm.
Before Russia invaded Ukraine in February 2022, Ukraine provided 90% of semiconductor-grade purified neon gas used by chipmakers. Semiconductor producers did, however, start diversifying suppliers and building up stockpiles after Russia annexed Crimea in 2014. As a result, the semiconductor industry has not faced serious shortages of neon gas during the conflict.
But the industry continues to grapple with supply chain bottlenecks that began during the pandemic and have been exacerbated by the war. In March, the advanced semiconductors on which defense contractor Mercury Systems relies for platforms such as Lockheed Martin’s F-35 and Aegis and Raytheon’s Patriot and Lower-Tier Air and Missile Defense Sensor radar system still had wait times of 36-99 weeks—“a length of time that just isn’t acceptable,” President and CEO Mark Aslett wrote in a blog post on the company’s website.
- Download Aviation Week’s new app at AviationWeek.com/App for our team’s up-to-the-minute coverage from the Paris Air Show
In an April earnings call, Aslett said lead times for semiconductor processors had improved modestly, with a range of 13-78 weeks. However, because constraints in some areas continue to affect new product development and program execution, he added: “We don’t expect a significant improvement in lead times until the second half of fiscal 2024.”
The U.S. government has revived industrial policy initiatives in a bid to mitigate risks to the semiconductor supply chain. Crucially, it has persuaded TSMC to make advanced chips in the U.S. The Taiwanese chipmaker has committed to building two semiconductor fabrication facilities (“fabs”) in Arizona at a cost of $40 billion. Meanwhile, the $280 billion CHIPS and Science Act allocates $52.7 billion for domestic semiconductor manufacturing. CHIPS stands for “creating helpful incentives to produce semiconductors.”
Miller notes that certain types of advanced chips called field programmable gate arrays—logic chips best known for their programmability and widely used in defense systems—are made exclusively in Taiwan by TSMC. “One of the aims of the CHIPS Act is to bolster production of advanced processors to ensure that military requirements can be met with domestic production,” he says.
TSMC makes semiconductors used in F-35 fighter jets and a wide range of other “military-grade” equipment by the Defense Department. However, the full range of chips the company makes for the U.S. military, and the Pentagon’s overall dependency on Taiwan for these semiconductors, are not widely known.
A combination of factors drove TSMC’s decision to build a fab in Arizona. These include proximity to key American integrated circuit design houses that account for 60% of its revenue, supply chain diversification, national security considerations and favorable government support, Kai-An Cheng, an industry analyst at the semigovernmental Market Intelligence & Consulting Institute in Taipei, tells Aviation Week. “By expanding its manufacturing footprint in the United States, TSMC aims to contribute to the resilience and competitiveness of the U.S. semiconductor industry,” he says.
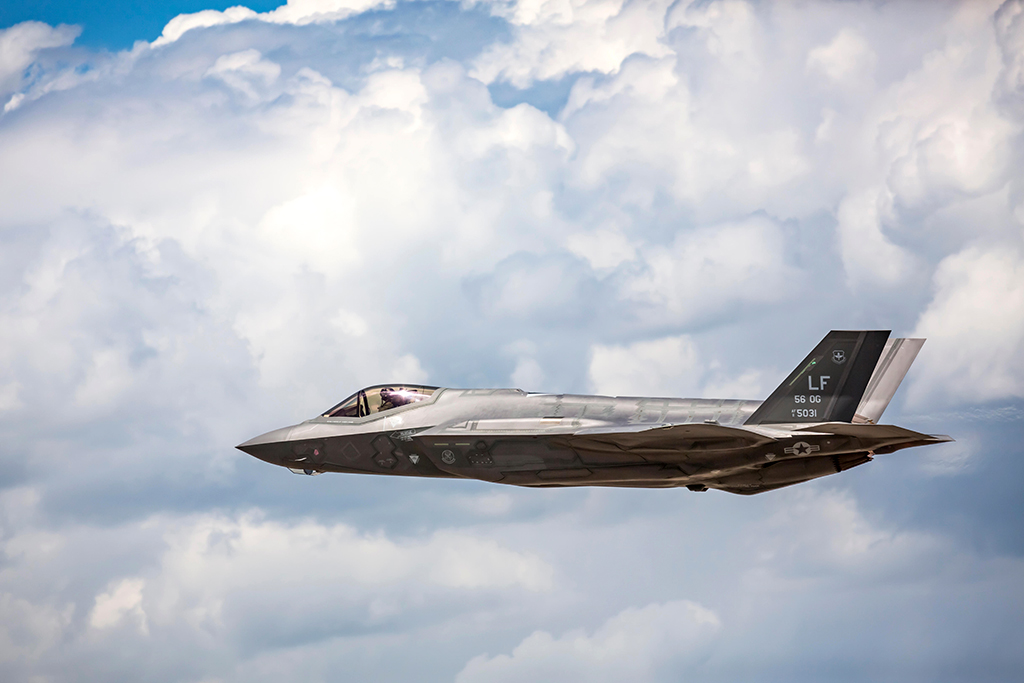
Ensuring a domestic chipmaking supply for the U.S. military is not a novel idea. The Pentagon launched the Trusted Foundry Program two decades ago for that purpose. According to the Center for Strategic and International Studies (CSIS), the program has grown to include 75 device-makers as well as companies focusing on packaging and testing. But as of 2021, these “trusted foundries” were making just 2% of the chips for military systems, among them semiconductors that need to be hardened to withstand radiation in space or a nuclear conflict.
A long-running challenge for the Pentagon is that it only accounts for about 1% of global semiconductor demand, giving it limited influence over the development of crucial technologies. The entire aerospace and defense semiconductor industry is valued at about $6.3 billion, according to Oregon-based Allied Market Research. In contrast, the automotive semiconductor market is valued at close to $60 billion, while the market for smartphone chips is worth $144 billion.
“One of the primary challenges for the defense industry is the design of a chip,” Peter Hanbury, a partner at Bain & Co. and an expert in semiconductor manufacturing, tells Aviation Week. “It’s a capability issue and a cost issue.”
For example, while a cutting-edge 5-nanometer chip may cost $500 million to design, it makes financial sense for Apple to do so because it can amortize the costs over the many smartphones it sells. Apple shipped 225 million smartphone units in 2022, generating $197.2 billion in revenue.
For an F-35 fighter jet, on the other hand, the economies of scale just are not there. “There haven’t been even 1,000 F-35s produced to date, so the numbers are just dramatically different, even if per platform the chip intensity is higher on an F-35 than on an average commercial capital good like an automobile,” says Michael Sion, a partner at Bain and expert in aerospace and defense.
It is also a challenge for the Defense Department to persuade companies to keep producing old technology to support legacy chips. While consumer electronics and data centers generally require advanced semiconductors, defense systems designed decades ago need older chips when they are repaired. “Chipmakers often don’t find it profitable to produce such old chips, so the Defense Department has struggled to keep low-end, old chipmaking capabilities online,” Miller says.
No quick fix for the problem exists.
“Maybe there is a world where you can convince those [trusted] U.S. foundries to repurpose their output toward aerospace and defense in a national security situation, but today they don’t,” says Jim Harris, a partner at Bain and co-leader of its global aerospace, defense and government services practice.
While the U.S. has been focused on boosting domestic semiconductor fabrication, it has paid less attention to outsourced assembly, testing and packaging (OSAT) of semiconductor devices. Semiconductor packaging involves enclosing integrated circuits in a form factor that can fit into a specific device. Samsung’s Newsroom explains that “if a semiconductor were a human brain, its packaging would be the nervous system and skeletal structure.” The last stage of semiconductor fabrication is the package test, during which the packaged chip undergoes final quality assurance procedures.
The U.S. has just a 5% share of the OSAT market, according to the CSIS. Most OSAT operations are based in Taiwan, China and Singapore.
The lack of onshore OSAT capacity could pose security risks. “We tend to get excited and animated about aspects of chip production like design and manufacturing, but the packaging is where, from a security perspective, the vulnerabilities actually become quite concerning,” Christian Rodriguez, an expert associate partner at McKinsey & Co.’s Aerospace and Defense practice in Washington, tells Aviation Week. “Packaging represents a handover in the ownership and control of the device from the manufacturer to the packager. It becomes a natural entry point for something to happen. If we can’t package chips, we have to send them somewhere else, potentially disrupting the supply chain and security.”
For that reason, boosting OSAT capabilities in the U.S. could strengthen overall resilience of the semiconductor supply chain. “We want to build more capacity onshore so that [at] least for mission-critical, safety-critical, high-consequence-of-failure systems, more of that final packaging is being put in place somewhere with a high degree of assurance and trust,” Rodriguez says.
Given that geopolitical tensions remain high and may well increase in the coming years, it is no surprise that the aerospace and defense semiconductor market is set to more than double in size by 2031. Allied Market Research forecasts that the market will reach $12.9 billion by that year, up from $6.3 billion in 2021. Driving market growth will be burgeoning military expenditures, increased aircraft modernization and the use of radiation-tolerant semiconductor components.
Efforts to boost supply chain resilience will continue. Yet there will be a limit to how much of the semiconductor supply chain the U.S. can build onshore. Steep costs are a key factor, as are availability of labor and the high degree of specialization necessary in parts of the industry ecosystem. For these reasons, the aerospace and defense industry will remain dependent on a wide variety of suppliers in other countries—mostly in East Asia.
Taiwan’s dominance in chipmaking means that the impact of a conflict with China on the semiconductor supply chain and the broader economy would be exponentially greater than Russia’s invasion of Ukraine. The research firm Rhodium Group estimates that a Chinese blockade of Taiwan, even without the use of force, would imperil $2 trillion in economic activity.
With that in mind, resiliency for the semiconductor supply chain can only be ensured if the Taiwan Strait remains peaceful.