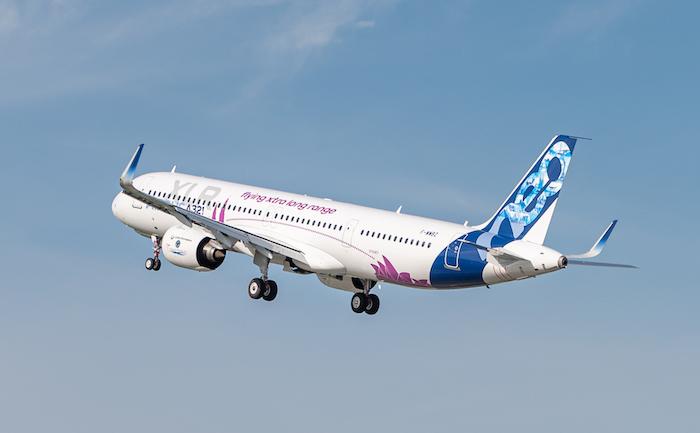
Credit: Airbus/Stefan Kruijer
PARIS—CFM International has unveiled details of an upgrade to the Leap 1 which has been developed to fix the long-running coking issue around the fuel nozzle that has affected the engine on the Airbus A320neo and Boeing 737 MAX fleets. The coking problem was traced to temperature-induced evaporation...
Subscription Required
This content requires a subscription to one of the Aviation Week Intelligence Network (AWIN) bundles.
Schedule a demo today to find out how you can access this content and similar content related to your area of the global aviation industry.
Already an AWIN subscriber? Login
Did you know? Aviation Week has won top honors multiple times in the Jesse H. Neal National Business Journalism Awards, the business-to-business media equivalent of the Pulitzer Prizes.