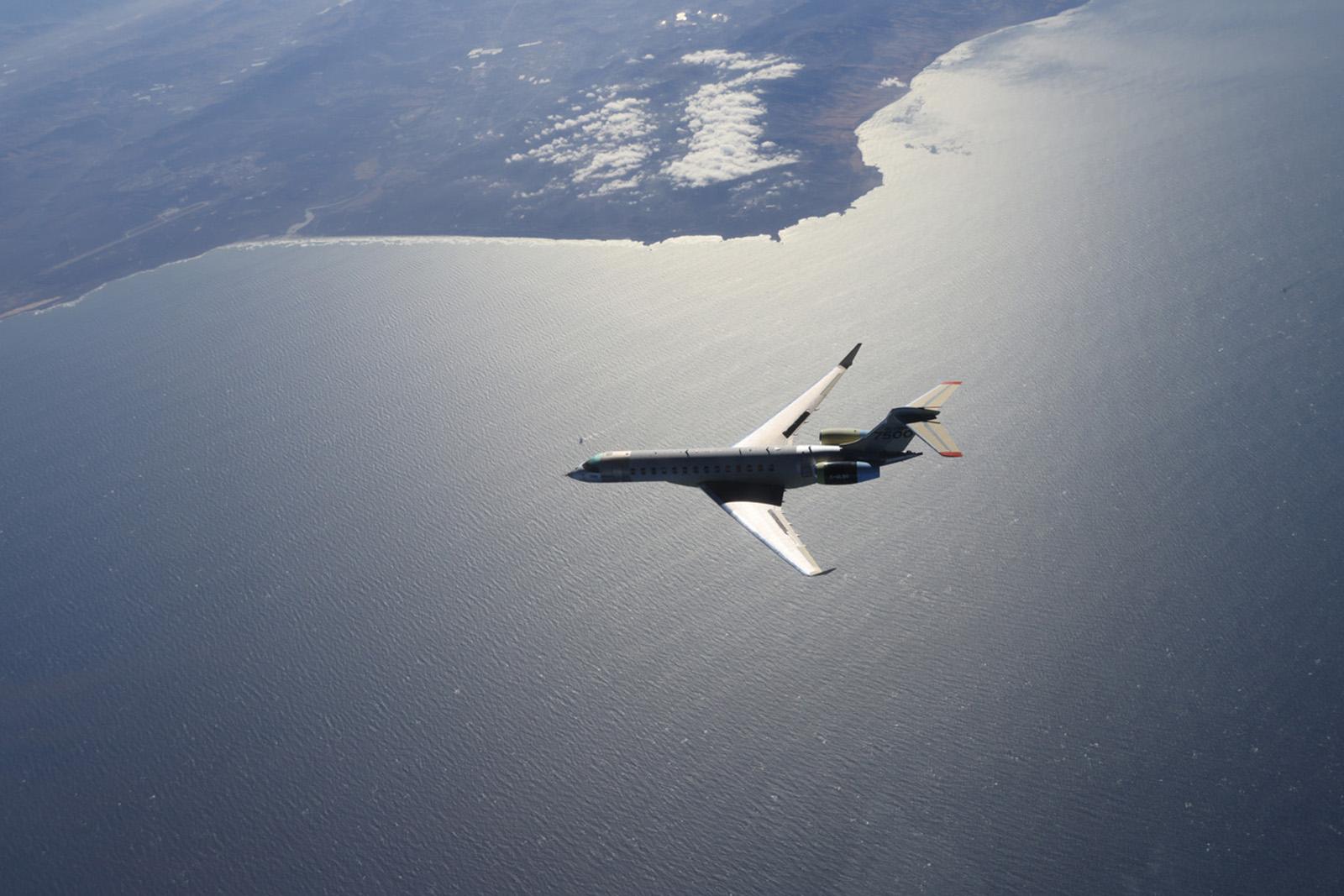
COLORADO SPRINGS—As Bombardier continues certification tests of the extended-range Global 8000, company test pilots have provided new details of the unusual supersonic flight-test campaign conducted last year off the California coast.
Flight testing for the fastest and longest-range purpose-built business jet is being conducted using FTV-5, a development Global 7500 aircraft on which the new variant is based. Tests at supersonic speeds were required as part of plans to certificate the Global 8000 with a maximum Mach operating speed (MMO) of Mach 0.94, versus the Global 7500’s top speed of Mach 0.925.
Bombardier’s high-speed test campaign culminated in May 2021 when FTV-5 repeatedly achieved supersonic speed in shallow dives, reaching Mach 1.015 off California’s Pacific coast. The tests marked the fastest flight of a civil aircraft since the retirement of the Anglo-French Concorde and the first transport category aircraft to fly supersonically with sustainable aviation fuel.
Describing details of the test and lessons learned, Ed Grabman, senior technical authority for the Bombardier Flight Test Center and an engineering test pilot, said envelope expansion was undertaken because certification requirements require a minimum margin between the maximum cruise speed and the maximum dive speed. “So, while the speed increase was not particularly large the regulations would require us to demonstrate that the aircraft is safe at supersonic speeds. And keep in mind [that] while this is a transonic jet, initially there's never been any plan to test it above Mach 1.”
Speaking at the Society of Experimental Test Pilots symposium in Anaheim, California, in September, Grabman said the overall project was divided into three phases. The initial stage focused on verifying that stability and control requirements could be met in the new speed regime, while the second phase covered envelope expansion to supersonic speeds. A third phase, yet to come, will involve certification tests of the aircraft with any necessary flight control and systems modifications.
As part of preparations for the flights a complete systems analysis was conducted to understand the effects as the aircraft went supersonic. As a result, the standard air data system was augmented with an experimental air data system, which consisted of a nose-mounted miniboom and a trailing cone on the empennage—the latter for measuring accurate free-stream static pressure.
Flying outside the envelope protection of its fly-by-wire (FBW) flight control system, the crew resorted to operating the aircraft in direct mode instead of the standard normal mode. For testing aeroelastic excitation the high rates of descent and short time on condition meant that the usual external aerodynamic vane system could not be used for testing frequency sweeps and dwells. “So we went ‘old school’ and used stick wraps and control pulses for the excitation, but instead of the pilot making the inputs they were actuated by the flight test injection system [(FTI)],” said Grabman, who added that this capability was embedded within the FBW system.

To assist with the high-speed evaluation, the aircraft’s 18,920-lb.-thrust-rated General Electric Passport engines were also marginally uprated through a temporary software change. Although the engines provided “plenty of thrust for level flight at 0.94 Mach,it really didn't do much to reduce the dive angles needed for the Mach expansion test,” says Grabman.
Testing was conducted in restricted air space off the coast from Vandenberg Space Force Base. “There were some test area constraints,” says Jeff Karnes, principal engineering test pilot at Bombardier. “We had to stay greater than 12 mi. offshore, and we couldn't be pointed at land when we did the supersonic dives because of the shockwave. We also had to stay within 90 nm of our telemetry trailer, which was located at Santa Maria Airport,” he says. For safety, the aircraft was fitted with a high-speed recovery chute on a tail-mounted mortar and was provisioned with two inflight emergency egress doors, one at the bottom of the aircraft around midfuselage and the other located in the cargo bay, which was modified with a hydraulic ram door opening device. The crew also wore life vests and parachutes. A NASA-operated Boeing F/A-18 was used as the chase aircraft.
Pitch angles that gave the right Mach speed and longest time on condition were defined prior to flight tests in an engineering simulator. “We had to maximize time on condition, so we chose a steeper initial acceleration angle to get to about 0.15 Mach below the target Mach,” said Karnes. Dive angle could be altered based on atmospheric conditions, temperatures and winds. “On the dive the pilots just modulated within plus or minus 1 deg. of that target pitch angle so that we could make sure we got to the Mach desired,” he added.
Envelope expansion was conducted from Mach 0.985-1.015 in 0.01 Mach increments. Each test point included flutter excitation in all axis via the FTI. “We also did pitch, roll and yaw control checks as we went down and then we extended spoilers to do a 1.5-2g recovery,” Karnes said. “There was limited time on condition, so we had to repeat the dive at each test condition to get all the data we needed to. On-condition time lasted between 15 and 22 sec. depending on the Mach number that we were trying to achieve.
Dives were conducted from around 49,000 ft. at Mach 0.88 “or as high and fast as we could get based on the fuel weight that we had,” Karnes said. “We had to recover by 37,000 ft. because of dynamic loads that we had to limit, or the position of the tropopause.” Pilots had to be careful of avoiding a Mach overspeed as they dove through rapidly changing temperatures or wind gradients. An instantaneous 5-deg. temperature inversion “costs about a Mach 0.01 exceedance, while an instantaneous 6 kt. wind increase on the nose is a Mach 0.01 increase,” he added.
The pilots worked with the ground-test team’s engineers and National Oceanic and Atmospheric Administration daily atmospheric sounding data to predict where gradients would be. “This doesn't mean that's what you're going to see when you get in the airplane, Karnes said. “So, during the climb to altitude, we had engineers on the ground in trailers that were looking at the temperature and wind profiles as we climbed up through it.” Using real-time data the ground team would calculate an updated acceleration dive pitch angle and Mach target offsets, as well as the final pitch angle, to achieve and maintain the Mach.
“Overall, testing went very well,” Karnes said. “There was very little airframe buffet, though it increased a little bit when we put G on. There was excellent control effectiveness in all three axis, though during the accelerations there were some minor nonlinear pitch and roll moments. But we expected that,” he added, saying these were likely caused by the shockwave moving across the control surfaces as the G7500 accelerated. “There was no Mach tuck or aileron control reversal, so we were pretty happy with that,” he said.
Not everything went to plan, however. On one high-speed dive the crew aborted the test after hearing a loud bang. No sign of damage was detected after returning to Santa Maria ,and the incident remained a mystery until a flight-test engineer noticed from camera footage that dynamic pressure had caused a composite wing-to-body fairing to temporarily deform. “When we slowed down they popped back to normal configuration. We did further inspections on the area and there was no damage, so we continued testing and we had this characteristic on most of the recoveries from then on,” Karnes said.
Another test was called off when the sensors indicated an overspeed of Mach 1.05. Analysis later showed the chase aircraft had flown closer longitudinally, causing its shockwave to impinge on the static cones of the trailing cone—resulting in a false reading.