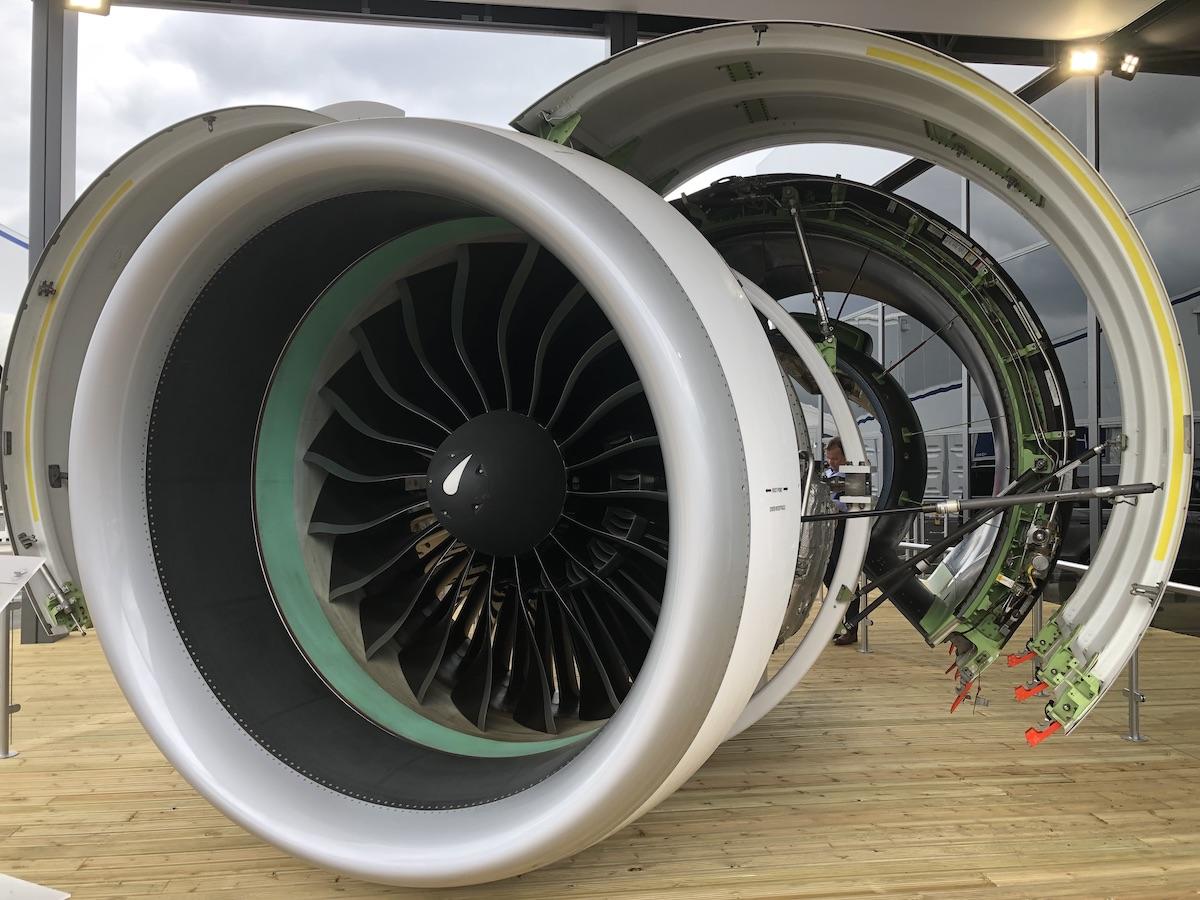
FARNBOROUGH—Pratt & Whitney has revealed key elements of a broad-based next-generation geared turbofan (GTF) technology plan to develop an engine with at least 10% better fuel efficiency over current engines by the end of the decade.
Outlining the plan for the first time since arch-rival CFM International launched the Revolutionary Innovation for Sustainable Engine (RISE) program for future powerplants in mid-2021, Pratt & Whitney Chief Sustainability Officer Graham Webb says the proposed development path builds on a wide range of propulsive and thermodynamic efficiency improvements—many of which are already underway.
Key features include plans to increase “the bypass ratio of the GTF engine beyond where we are today,” says Webb. Fan diameter will be increased beyond the existing 81 in. to push the bypass ratio from the 12.5:1 of today’s GTF towards the 15:1 range. “So we are working lightweight structures technologies. The composite fan blade is a key element of it as well as the composite fan case. We will also have to increase the fan drive system gear ratio,” he adds.
The GTF family is currently configured with an aluminum and titanium fan, but the next-generation design will be based on a three-dimensional woven composite material. “That will enable us to hit those higher bypass ratios,” says Webb.
Although the focus is on bypass ratio, Webb says “the actual physical parameter of interest for us thermodynamically is fan pressure ratio, so we're going to lower fan pressure ratios. We've actually demonstrated those in a recent program that was funded by the FAA CLEEN program and so that enabled us to demonstrate successfully the ability to go to the lower fan pressure ratios that we would require for the next generation of GTF engines.”

“We've been also working with funding from NASA on a variety of small core technologies focusing on improving the compressor - the aerodynamic efficiency and the sealing of the compressor,” says Webb. “Also we're working on the turbine in a similar fashion. We're advancing our cooling capabilities in the turbine using some advanced core technologies that we're going to first deploy with its first step in the Advantage engine. Then we have to have to work the combustor, and all of that is also associated with the powertrain development we have to work with.”
Key portions of the advanced core improvement work centers on the use of high-temperature ceramic matrix composites, the focus for which is taking place at a recently established research and development center in Carlsbad, California. “That's enabling us to actually produce airfoil components, which we're now doing. We have some proprietary technology in terms of the coatings that are required for that, that we're also embodying and we want to start doing the engine testing of that in 2025, generally speaking,” he adds.
Longer term, the roadmap also includes potentially adopting more-electric and hybrid power developments under study both internally and with GTF partner MTU in Germany. These include the Hydrogen Steam Injected Intercooled Turbine Engine (HySIITE) concept being evaluated by Pratt & Whitney that is designed to exploit the full potential of hydrogen by going beyond use as a fuel to also maximize its cryogenic properties to lower emissions and improve thermodynamic performance. MTU is studying the Water Enhanced Turbofan (WET) to build on an improved version of the engine by 2035. The WET engine adds a condenser to collect water from the GTF’s exhaust gas and a heat exchanger to vaporize the water into steam, which is injected into the combustor.