Workflow Management Software Going More Macro Management
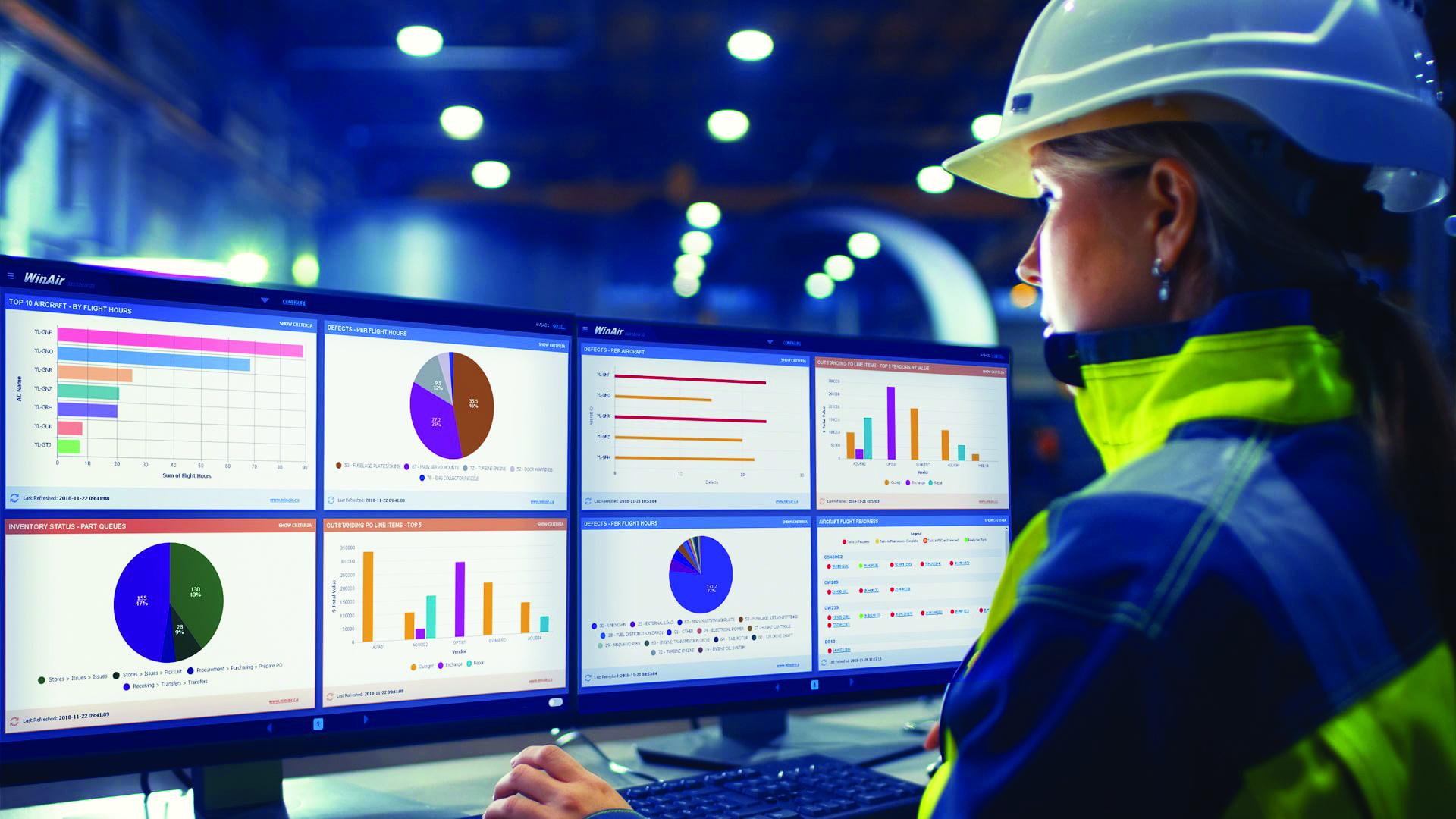
As MRO workloads increase, project scheduling, from induction to invoicing, becomes more complex. Software has automated workflow management by replacing magnet waterfall boards and Excel sheets, but today that is no longer enough. Instead, software designed to maximize workflow efficiencies must function as an integrated component of a total enterprise resource-planning (ERP) system, which is now likely to be cloud-hosted.
Because today’s MRO industry incorporates more predictive maintenance operations, “a more dynamic scheduling capability is therefore needed that optimizes across manpower, tools, facilities, capabilities, finance and materials—with a significant degree of granularity,” says Torsten Welte, SAP’s global vice president and head of the industrial business unit for aerospace and defense, travel and transportation. “MROs are looking for a real-time, integrated, holistic view of all resources, along with intelligent decision-support, tools that are easy to use, and the ability to eliminate duplicate tasks and manage a portfolio of projects,” he says.
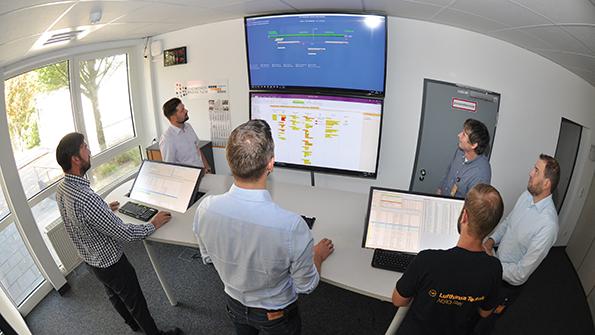
“Interactive, collaborative and integrated” resource planning is also critical for effective and efficient maintenance execution, adds Johann Schactner, SAP’s industry solution manager in the travel and transportation industry business unit.
Supervisors and planners often allocate resources using virtual tools. “This capability is provided by a multi-resource scheduling tool to aid users when making scheduling decisions, visualize the planning situation, visualize the usage of resources, and perform manual, automated and optimized work assignments,” Schactner explains.
SAP’s MRO tools offer core planning and scheduling capabilities as part of a total enterprise management package, such as the vendor’s Enterprise Portfolio and Project Management, Multi-Resource Scheduling and Integrated Business Planning. In that way, additional capabilities can be deployed and seamlessly integrated to enhance planning and scheduling, says Schactner. “We provide dedicated capabilities to schedule critical resources—which could be human resources, machines, tools and events. Due to the integrated nature, constraints such as skills of human labor and machine availability can be easily considered,” he says.
In general, the MRO industry is looking for more automation in the scheduling and assignment of resources for proposed or planned maintenance events. “At the earliest stages of planning a maintenance input, the provider wants to see proposed hangar slots and manpower availability against the workload,” says Chris Clements, sales representative for Swiss Aviation Software (Swiss-AS). “This may not be just hangar-based maintenance, but it also needs to include the workshops in case there are any components that require [outsourced] processing.”
Clements says another emerging trend for scheduling software is to incorporate the ability to determine what portions of the manufacturing or repair process should be sequenced or prioritized, along with planning for the infrastructure or supplies needed.
While there are still more requirements being identified, “once the initial requirements for the workscope have been defined, the next steps should be proposed and scheduled, and all associated resources and parts should then be identified and planned as part of that process,” Clements says. He adds that this particular scenario is being addressed by Swiss-AS by upgrading its AMOS Component Maintenance modules. AMOS is the vendor’s widely used maintenance management system.
Chris Lawn, marketing specialist for global aviation management software producer WinAir, reports that WinAir Version 7, the company’s aviation maintenance scheduling and inventory control software product, is designed to integrate with other systems, such as accounting and flight operations.
“While many maintenance software systems claim to do everything for everyone, rarely does this turn out to be the case,” Lawn says. “On the other hand, software that integrates with a customer’s existing systems not only provides the ability to continue using those systems, but enables the customer to leverage the data within them.” These integrations save MRO operations significant time because they automate procedures, eliminate duplicate data entry and boost overall business efficiencies.
Michael Perrotta, a WinAir product support specialist, says MRO scheduling software should provide the capability to schedule as well as forecast, taking into account scheduled and unscheduled work, the parts that will be required and current inventory levels.
Among WinAir Version 7’s latest enhancements is “Work Packages,” designed to address scheduling and workflow management across multiple MRO locations. “With a Work Package, all parts of the project can be bundled together, focused on where the work will be done and when scheduled,” he explains. “The package also allows tracking as production moves among different MRO facilities, including labor allocation and parts stock flows.”
Work Packages, along with Access Groups, says Perrotta, are applicable to a multilocation MRO, as well as to one that outsources some of its work. “If some of the work has to be outsourced, that facility can be given access to whatever data they need to accomplish the work. This is a feature more customers are asking for, especially when there are expertise or lower labor costs at locations out-of-house.” Work Packages is now in its first phase of development; the next two phases will be released during the second quarter of this year, he says.
WinAir is a cloud-based product, largely as a result of preference by the MRO industry for software as a service (SaaS). Doing that, Perrotta says, saves the MRO the expense of setting up an in-house hosting infrastructure and makes it easier to manage data in real time. “If you cannot keep up with data management in real time, forecasting goes out the window,” he stresses.
One example of an MRO using work scheduling automation is Lufthansa Technik AERO Alzey (LTAA). Technical Director Thomas Hoffmann says that in 2010, LTAA scrapped Excel sheets and moving magnets on waterfall boards in favor of a digital data-driven system. “This system offers scheduling of single work steps and much greater visibility of the overall production status,” he says.
For scheduling, LTAA uses a standard production software product called FAST/Pro from GTT, which is connected in real time to LTAA’s SAP-ERP system, and an add-on, SAP iMRO.
“Adjusted to MRO needs, FAST/Pro is continuously improved by local programming staff to meet our evolving needs,” he notes. “It also interfaces with our customer information system, LUCIS. Having FAST/Pro as a separated platform from our standardized SAP iMRO ERP system allows us to quickly adjust it to our production needs.”
As Hoffmann explains, every engine is inducted into the shop using a “net plan” that reflects the customer’s approved workscope. With this net plan, manpower resources—needed today and projected—as well as material availability, reflecting actual delivery dates from suppliers, are factored in. “The software tells the mechanic what to do next in order to have an optimum production flow,” and customers can view projected delivery dates, he says. “We need to reflect the whole value chain, from receiving a customer order to writing the invoice. All processes that are needed in between are integrated in the workflow.”
To manage the complexity, each person working on engines has his or her own visualization and workflow screen, based on role and responsibility.
LTAA considers FAST/Pro’s ability to prioritize material needs as critical. “Having the material needed to build an engine is a daily challenge, with a few missing items sometimes delaying assembly on or near the scheduled due date,” says Hoffmann. “A clear visibility of potential late deliveries, optional material usage or internal repair issues is key. For example, we may need to know when a part is required for a special assembly task, and the system tells us if the delivery date fits, or if we need to look for alternatives.”
Hoffmann admits that without an automated scheduling system, handling more than 100 engines—with hundreds of thousands of parts, simultaneously—would be impossible. “With Excel sheets and magnet waterfall boards, we had daily status meetings requiring a lot of preparation time, with more than 25 foremen and engineers lasting close to 2 hr. in peak times,” he notes. Now, production status is available in real time. “The mechanic just clicks ‘started’ and ‘finished’ for an assigned work step. No one has to walk around collecting the information and writing it in Excel sheets,” he says.