MRO Technician Shortage Drives New Training and Recruiting Strategies
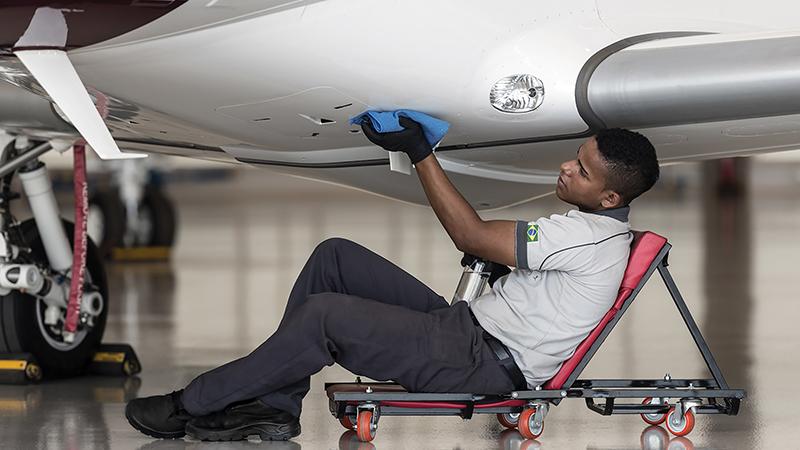
Growing customer demand for new maintenance lines led Embraer to launch a new training program this year in Brazil.
Credit: Embraer
A booming market is forecast to boost maintenance, repair and overhaul business over the next two decades, but the industry might struggle to meet demand if the pipeline of new maintenance technicians cannot keep pace. In response, stakeholders across the aftermarket are ramping up efforts to...
MRO Technician Shortage Drives New Training and Recruiting Strategies is part of our Aviation Week & Space Technology - Inside MRO and AWIN subscriptions.
Subscribe now to read this content, plus receive full coverage of what's next in technology from the experts trusted by the commercial aircraft MRO community.
Already a subscriber to AWST or an AWIN customer? Log in with your existing email and password.