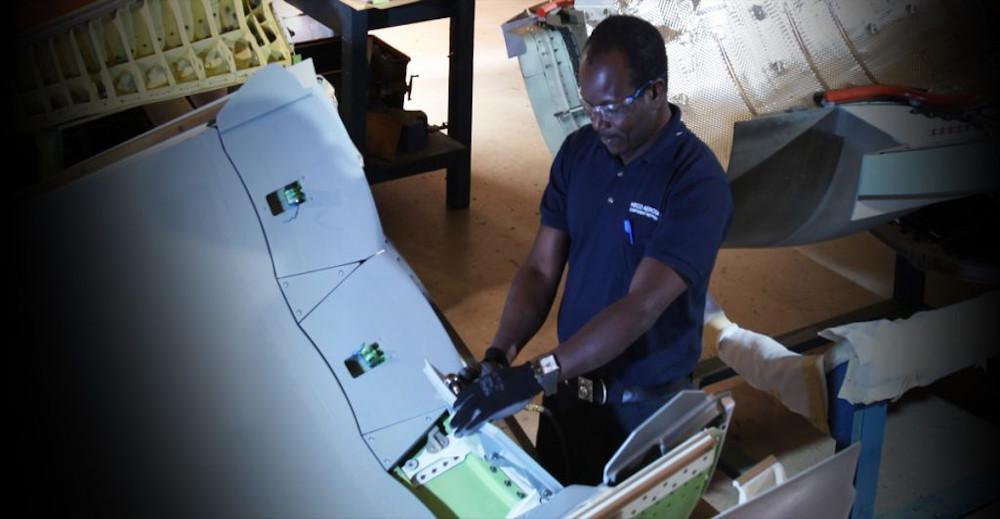
The engine overhaul bottlenecks that so frustrated airlines up to just a year ago now feature only in the fever dreams of MRO managers struggling to match shop capacity to drastically reduced demand.
Nonetheless, consultancy IBA has noted “surprisingly” that there are still some delays for engine repair slots.
“The overall trend is for very minimal lead time for all engine types, but there are some delays which are largely down to light scope hospital shop visits on engines, not the full workscope overhaul and LLP replacements,” said engine senior analyst David Archer.
He also noted that some capacity was being accounted for by an uptick in the return of leased engines and concomitant MRO work required.
Overall, IBA reported a 50-60% revenue drop for the engine MRO sector in the second quarter.
Interestingly, it also noted a low appetite for teardowns and used serviceable material (USM), which is usually an attractive avenue for airlines to keep repair costs down.
However, low utilization of aircraft and low utilization of material as airlines juggle equipment between grounded and active aircraft and engines, combined with their reluctance to pay for shop visits, has meant a fall in the demand for--and value of--components.
The fall may well accelerate as increasing numbers of aircraft hit the part-out market, but this could be good news for airlines with reasonably young CFM56 and V2500 engines, which are likely to return service and still await their first shop visits.
For when those visits occur, the airlines should benefit from some of the lowest material costs for many years.
It may well also have a knock-on effect on the price of new spare parts from the OEMs, meaning that the crisis may put a brake on the part price inflation that has so annoyed operators over the last decade.