MROs Still Focused On Workforce, Supply Chain Issues
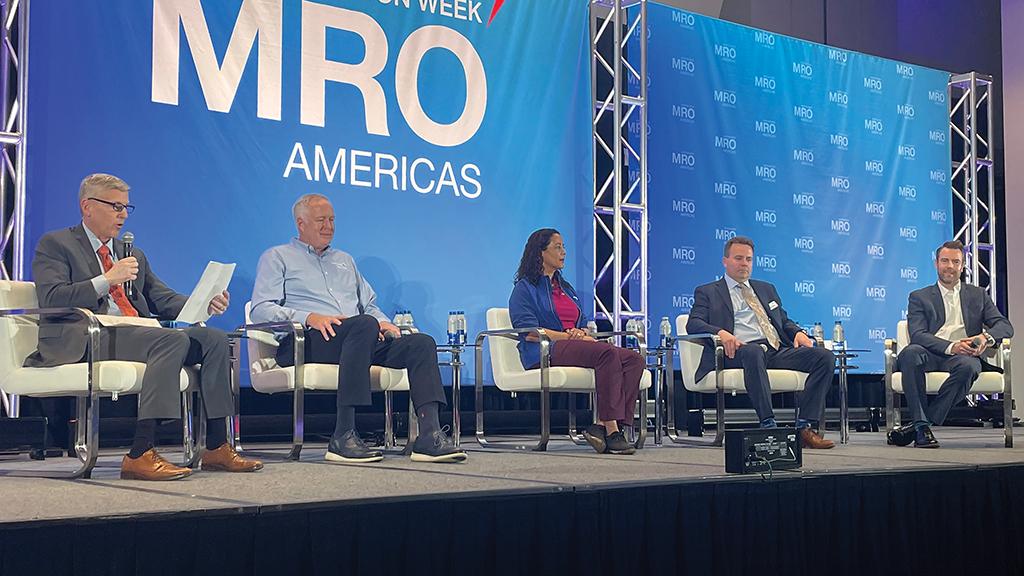
Pictured from left: Dennis Santare, partner at Oliver Wyman; Rick Brown, director of technical operations training at United Airlines; Simone Drakes, managing director of United’s Calibrate program; Ryan Goertzen, vice president for workforce development at AAR; Phil Shorten, head of human resources for U.S. Commercial at Airbus Americas.
Credit: Lindsay Bjerregaard/Aviation Week Network
Industry’s largest event dedicated to MRO was an appropriate setting for updates on the biggest challenges facing aftermarket stakeholders. Panelists at Aviation Week’s MRO Americas, which drew more than 17,000 attendees to Chicago April 9-11, spent much of the event discussing the major pain points...
MROs Still Focused On Workforce, Supply Chain Issues is part of our Aviation Week & Space Technology - Inside MRO and AWIN subscriptions.
Subscribe now to read this content, plus receive full coverage of what's next in technology from the experts trusted by the commercial aircraft MRO community.
Already a subscriber to AWST or an AWIN customer? Log in with your existing email and password.