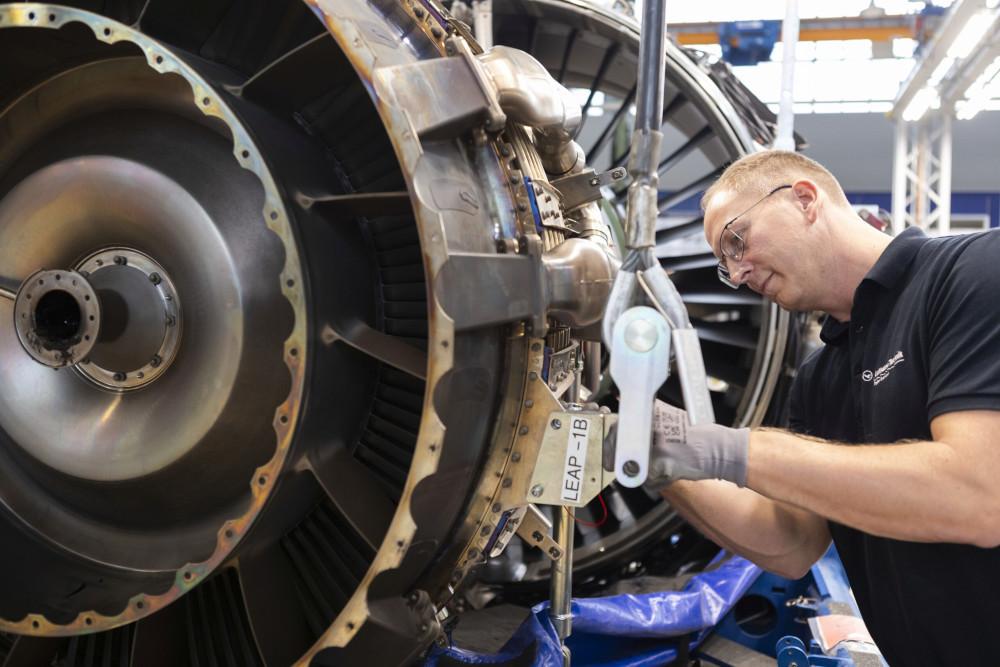
Pandemic-induced labor shortages have been partially overcome by big MRO providers, thanks to investment in training facilities, recruitment drives and links to higher education.
U.S.-based StandardAero, for example, continues to invest in its recruitment and training functions, such as its new San Antonio-based training academy, and in close relationships with local technical colleges. As a result, its employee count is 1,500 higher than in 2019, at around 7,500 people.
Unfortunately, smaller organizations have found it more difficult to re-staff, especially specialized repair shops, which had led to third-party repairs becoming a choke-point in the engine aftermarket.
“The problem is in the parts that go outside for repair and the backlog that still exists in the subcontracted repairs,” said Ana Bidarra, engine shop planning and control manager for TAP Portugal, at Aviation Week Network's Engine Leasing Trading & Finance Europe conference in London earlier this year.
However, MRO providers are more optimistic now.
In an interview with Inside MRO Lufthansa Technik’s Martin Mueller observes that “with global capacities coming back online, the overall situation and turnaround time of subcontracted repairs are improving.”
Filip Stanisic of Magnetic MRO in Estonia agrees, saying: “Third-party repairs are still lasting longer than pre-COVID, but turnaround times (TAT) for material repair have dropped significantly compared to post-COVID days when they delayed engine repair TAT drastically.”
He adds: “Most of the repair vendors are doing their best to cope with the demand and return repair TAT to what we had before COVID. On some materials, we are already at the level of 30-40 days, and it’s a huge improvement from the 120-180 days we saw a couple of years ago.”
For a closer look at the engine maintenance market, see the next issue of Inside MRO.