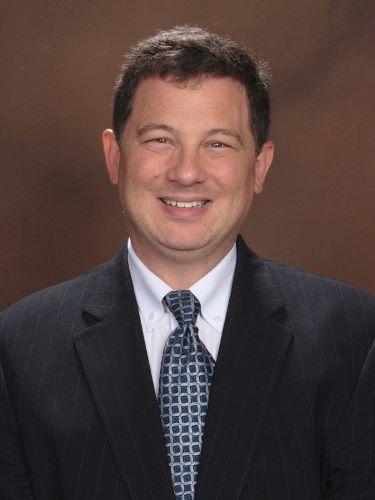
Jason Dickstein, president of Washington Aviation Group
The Aircraft Fleet Recycling Association (AFRA) is developing a major program with the Civil Aviation Administration of China (CAAC) that will look to develop opportunities for AFRA's best management practice (BMP) accredited part-out companies. Jason Dickstein, president of Washington Aviation Group [which represents AFRA], gives Aviation Week more insights into the collaboration project.
Could you provide an overview of the AFRA and CAAC collaboration program?
The Chinese industry was hit by counterfeit and bad part issues around 10-15 years ago. In response, the CAAC has begun investigating how to buy safe used serviceable material (USM) again without exposing the industry to counterfeits. Their intention was to purchase USM from entities with China Civil Aviation Regulations [CCAR] Part 145 repair station certificates with the special disassembly ratings. They have been observing AFRA for a long time and have seen its efforts over the years. AFRA has an accreditation program which focuses on environment, safety and airworthiness—which are the priorities for the CAAC. Because of this, they were interested in AFRA and put trust in us.
We are building a special limited program with CAAC around their advisory circular on disassembly. This program will help AFRA BMP accredited companies obtain CCAR Part 145 certification from CAAC to sell their disassembled parts into the Chinese market. Once the companies receive a CCAR Part 145 certificate, they can tag their disassembled parts under the Chinese database system and make them available for the CCAR certified repair stations. Currently, we have a Chinese version of the database, but as part of this program, we will develop an English version. In short, as a part of the collaboration, AFRA will provide CAAC with the companies that are acceptable for the investigation, inspection and further certification.
What are the primary goals of the program?
The primary goal of this program is a combination of safety and commerce. AFRA already has an accreditation program that helps to encourage aviation safety. One of our goals is to continue to have a safety program that ensures the disassembled parts are treated in a way that preserves their airworthiness. On the commercial side, we want to ensure that people from all around the world can work together towards safety and can purchase and sell good parts in order to make sure their aircraft stay airworthy. Apart from that, CAAC has its own goal to prevent any counterfeits from their system.
How will the program help AFRA BMP accredited part-out companies?
We expect that the program will open up a new market opportunity for the companies that have made an investment and are getting AFRA BMP accreditation. For instance, the UK-based part-out company who owns the disassembled parts can’t sell those parts in China because it is illegal and doesn’t meet CAAC requirements.
So, this program will give those companies a way to have processes in place that the CAAC accepts and CCAR Part 145 certification, which will allow them to sell their parts into the Chinese market. Along with that, it will also help the Chinese carriers and the Chinese operators to be able to source USM parts that are known to be good in the global marketplace.
What oversights and regulatory requirements will be associated with the program?
Both AFRA and CAAC have their own laws, regulations and accreditation programs. Through this program we are trying to take the pieces that already exist and put them together so that CAAC can accept USM from foreign companies. AFRA has voluntary standards which focus on two different areas: airworthiness and environmentalism. On the airworthiness side, part-out companies need to have provisions related to training of personnel to ensure that they know how to disassemble an aircraft properly. There will be documentation, tooling and tagging requirements for the disassembled parts to ensure their identity. Additionally, there are requirements related to handling of the parts to prevent any hazards or risks to the parts.
On the environmental side, there are provisions concerning the identification of local laws and its compliance. CAAC has its own set of regulations under CCAR Part 145, including certification and CCAR Part 145 manual requirements for the repair stations to ensure the basic processes are appropriate and in compliance with the regulations.
What trends are you observing in the aircraft recycling industry?
It is hard to say, as the trends are not linear because of COVID-19 and its aftermath. Before COVID, we predicted that there would be a huge wave in aircraft disassembly because of the expected volume of aircraft retirements. However, it didn’t happen. Due to COVID, many aircraft were parked, which led to less of the need for the parts. Currently, we are seeing a substantial amount of aircraft disassembly, but not the huge explosion that people feared.