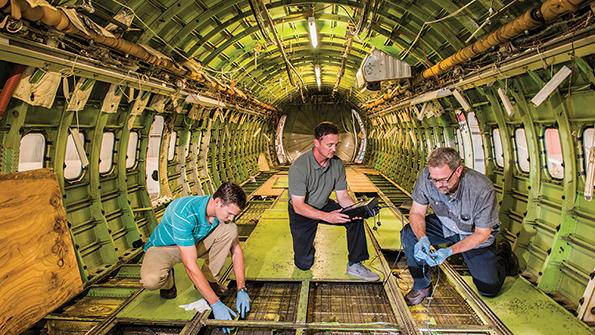
If an airframe structural inspection reveals a crack, the aircraft, by regulation, is grounded until repairs are made. By contrast, an engine turbine blade with a known hairline crack could remain on wing, as increased inspections determine when the blade must be replaced. To level the playing field, regulatory approval of structural health monitoring (SHM), employing high-tech sensors, is being sought.
Sandia National Laboratories in Albuquerque, New Mexico, a leading SHM research and development center, has primarily worked with five different sensor technologies—comparative vacuum monitoring (CVM), piezoelectric (PZT), fiber optics, carbon nanotubes and acousto-ultrasonics (AU). “Each has its own way of interrogating a structure to obtain signatures associated with specific types of damage,” says Dennis Roach, a senior technical fellow there.
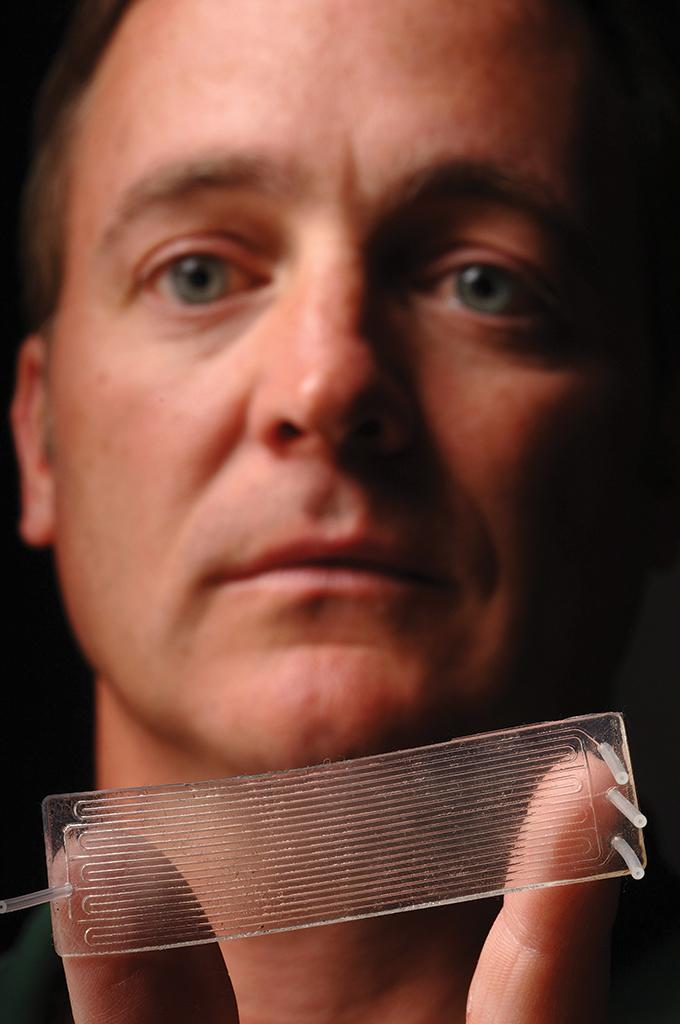
CVM and PZT are considered the maturing technologies. With CVM, a sensor in the form of a self-adhesive elastomeric patch—about the size of a credit card—is used. By applying vacuum pressure to the sensor’s built-in rows of interconnected channels, any measurable change in the vacuum level will reveal a crack.
But PZT sensors have an advantage over CVM, says Amrita Kumar, executive vice president of Acellent Technologies in Sunnyvale, California. “CVM sensors are ‘point sensors,’ which means they need to be placed exactly at the location where damage such as cracks are anticipated,” she says. “PZT sensors, such as Acellent’s Smart Layer sensors, can be used in a network design to monitor an entire area for damage.”
Kumar adds that another advantage of a PZT Smart Layer sensor network, compared to CVM, is that it can be used in both an ultrasonic and acoustic mode for crack detection. In an ultrasonic mode, the sensors can be used periodically to provide information on damage location and size. In an acoustic mode, the sensor network “listens” for external impacts and provides the location and magnitude of damage to the structure.
The Smart Layer sensors, says Kumar, have successfully undergone MIL-STD 810G and lightning-strike testing for use on any metal or composite structure. Also, the sensors have been proven for use in damage detection through extensive testing and validation at the coupon, component and flight-test levels.
“Boeing and Korea Aerospace Industries (KAI) have both adopted the technology and declared it ‘tech-ready,’ and Airbus has flight-tested it on the A350,” she says.
Airline Benefits
“For airlines, SHM could be an airframe maintenance game changer, moving unscheduled actions to scheduled maintenance,” says David Piotrowski, senior principal engineer for Delta Air Lines. “SHM will give us the data to safely manage our fleets more efficiently and in a more cost-effective manner. Rather than taking the aircraft out of service immediately for repair, the area could be monitored.” This can help determine if a crack needs to be repaired right away, or if it can wait until the next scheduled maintenance event or another convenient opportunity.
Using SHM in this manner could enhance safety, as it allows for continuous, real-time monitoring versus today’s periodic examinations, says Piotrowski. “While the technology is ready, there is more work to be done to persuade regulators of a data-driven, tail-specific maintenance program. Therefore, near-term applications of SHM will be limited to substituting for conventional inspections, which still provide substantial benefits to operators.”
In fact, Piotrowski points out, Delta is currently performing a 1,200-cycle repetitive inspection of the rear pressure bulkhead fasteners on its Boeing 737NG fleet as mandated by an airworthiness directive (AD). The airline has requested an alternative method of compliance (AMOC) using SHM technology rather than eddy-current inspections, as required by the AD. Other applications on Boeing and Airbus fleets also are being prepared for AMOC requests.
“On the 737NG family, the eddy-current inspection requires removal of a galley. If sensors were located in that area, the technician would only need to remove the galley if a problem is detected,” Piotrowski says. “Not having to remove the galley frequently would provide significant savings for the airline and allow the aircraft to be available for more revenue opportunities.”
Delta Air Lines has been leading industry efforts with SHM since 2005, including work done by Northwest Airlines, which installed CVM sensors on two DC-9s in 2004-07. Delta, which merged with Northwest in 2009, flew sensors on Boeing 757s and 767s in 2005-12.
Most of the initial work, explains Piotrowski, focused on data collection and addressing the question of how well the sensors would work under real-world conditions. The next question, he says, was answered in 2014, when an FAA-funded program was established to determine what, if any, certification guidance would be needed to support SHM applications. Under the program, Delta—in partnership with Boeing, Sandia National Laboratories and Anodyne Electronics Manufacturing—installed 10 CVM sensors in the center wingbox of seven of its 737-700s. The center wingbox was selected because it is a high-stress area. The installations were approved by a service bulletin revision drafted by Boeing. Those seven aircraft are still flying with the sensors installed and to date have logged 110,000 flight hours and 56,000 cycles, says Piotrowski.
Other programs included sensor installations by Azul, in conjunction with Embraer, on the Brazilian airline’s E190 jets, and an Air Canada Jazz CRJ that flew with sensors in 2009-10, he says. “Combining those with testing by Northwest and Delta, CVM sensors have flown some 1.5 million hr. to date,” he points out. “We have proven that the sensors work under all operating conditions—flight cycles, pressurization, vibration, contaminants—anything that could impact them in flight,” he adds.
NDT Substitute
Sandia National Laboratories’ Roach reports that the current focus of study is the use of SHM as a substitute for nondestructive testing (NDT) tasks that often involve the application of human-deployed inspection methods to identify damage. These are labor-intensive processes that require inspectors to physically access the “structure of interest” to conduct manual inspections. The idea behind SHM, Roach says, is to place an array of embedded sensors throughout the aircraft to quickly alert the operator that some type of damage is taking place on a certain structure. To achieve this, the sensors are tailored not only to the parts of the aircraft being targeted but to the type of damage to be detected. As SHM evolves, the interrogation will move past “hot-spot” monitoring to include applications across a broad spectrum of aircraft components.
“Basically, each SHM application is reviewed for desired flaw detection such as cracks, corrosion or disbonds; location such as the surface or subsurface; sensitivity required; as well as structural material, and geometry,” Roach explains. “Thn the sensor network approach is designed based on this information.”
In some cases, there may be several types of damage to be detected in one area. “In the future, the desire is to move toward condition based maintenance (CBM), allowing airlines to automatically acquire information from the sensors and use that to make maintenance decisions,” he says.
Roach adds that while there may be no need for more performance data in general, there will always be a need for testing the specific SHM application. In that respect, he says, additional flight history and successful operation from a series of applications will help move SHM into new areas faster. “We are acquiring that data now, but the newness of SHM technology—or any new aircraft technology—requires that the performance data be very comprehensive for each new application,” he says. “Once we get downstream, we will be much smarter on the performance of SHM for each variance in application. This will streamline the process from initial identification of an SHM application to final installation and routine use of SHM solutions on commercial aircraft.”
Rich Poutier, executive vice president, business development for Perth, Australia-based Structural Monitoring Systems (SMS)—the supplier of CVM sensors being used by Delta Air Lines for the 737 wingbox service bulletin inspections—reports that the next step for SMS is to obtain regulatory approval for application of the sensors to mandatory inspections. The FAA received an approval request from SMS in January 2019, he says.
Because the FAA considers the application of sensors to SHM a “new and novel technology,” the agency is finalizing what is referred to as a policy issue paper, says Poutier. That paper will provide the regulatory inspectors with guidance material to use as reference for approving future applications of the technology—which will initially take place on a targeted case-by-case basis.
“Once a sensor application is identified, we then design a sensor configuration [to] target that area to monitor for a surface crack,” he says. “The sensor can detect a crack as small as 0.1 in. [depending on the materials being monitored] and it can monitor crack growth until it reaches a size where the OEM would require a repair, based on the OEM’s damage tolerance model.”
According to Poutier, SMS is the only company certified by an OEM—Boeing—offering CVM technology for aircraft SHM through its patented and trademarked CVM product. SHM holds more than 30 patents globally for CVM technology, with 14 more pending. Those patents include surface crack detection along with detection of internal delamination within composites and composite bonds.
SMS selects targeted applications for its sensors, based on labor hours and aircraft downtime required for current inspection processes. Right now, the two with the highest priority are the 737NG aft pressure bulkhead, and the Wi-Fi antenna mount structure for all narrowbody aircraft.
“The aft pressure bulkhead AD calls for inspection of stringers 5-7L on the left side and 5-9R on the right side of the bulkhead,” Poutier notes. “It was selected because there can be a high amount of false positive readings when using conventional low-frequency eddy-current probe inspections, which sensors could reduce.” The false positive rate for many low-frequency eddy-current inspections averages 3-5%, he says. The result is unnecessary grounding of aircraft and galley removals to confirm if a crack exists on the forward side of the bulkhead.
For the Wi-Fi antennas, Delta Engineering (no affiliation with Delta Air Lines) holds the supplemental type certificate—licensed to Gogo—and has applied to the FAA for a revision to the instructions for continued airworthiness to include the use of CVM sensors as an option to visual and eddy-current inspections of the structure, Poutier adds.
While the FAA ignored a request for comment, the Euro-pean Union Aviation Safety Agency (EASA) gave a cautionary response. “EASA does not believe that SHM will change existing strategies regarding damage tolerance philosophies,” says Janet Northcote, its head of communications. “A conservative ‘step-by-step’ approach will be taken when considering potential adoption of SHM, as has been openly discussed in public forums with OEMs. It cannot be predetermined that use of SHM will allow flight with
known cracks.”