Opinion: EASA’s Paperwork Obstinacy Amplifies Supply Chain Woes
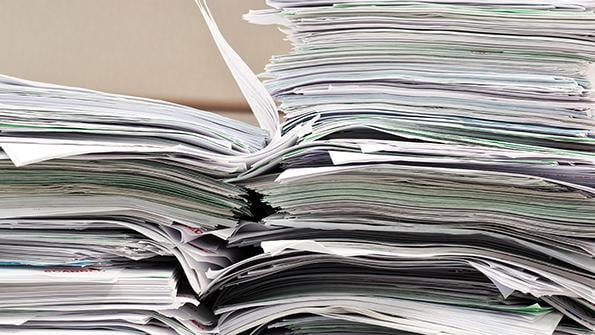
Current versions of forms required for new parts fitted during maintenance have undergone more than a dozen revisions since 2011.
In 2002, the European Parliament established the European Union Aviation Safety Agency to assume the responsibilities of the Joint Aviation Authorities system. The transition was completed by 2009, and the agency now establishes standards and oversees aviation safety for 31 member states. ARSA has invested considerable time supporting the agency’s blooming international leadership as the key bilateral partner of the U.S.
In 2015, Change 5 to the Maintenance Annex Guidance (MAG) between the FAA and European Union Aviation Safety Agency (EASA) first insisted new parts fitted during maintenance subject to the bilateral be accompanied by an FAA Form 8130-3 (or EASA Form 1) traceable to the production approval holder (PAH). Since then, EASA’s strong preference for paperwork has driven oversight of U.S. repair stations with European approval to the detriment of the mutual recognition embodied in the bilateral, American maintenance rules and the international supply chain for new parts.
Understanding the forces behind the problem requires a historical perspective. EASA benefitted from nearly a century of its American cousin’s hard-earned aviation safety oversight lessons. Chief among the benefits are the international mutual recognition and regulatory collaboration with the Joint Aviation Authorities (JAA) that occurred prior to EASA’s establishment.
Pre-EASA changes to FAA Form 8130-3 and its guidance for completion (Order 8130.21) provide insights into this collaborative history. The initial use of the form in the U.S. was for export only; it was issued by the FAA to establish compliance with an importing country’s requirements. Under harmonization efforts spearheaded by the FAA and JAA, the form underwent considerable revision in the 1990s to harmonize it “more closely with the form used for comparable purposes in other countries.” The new tag, updated in 1991, was primarily intended to facilitate acceptance of FAA-approved products and parts in other countries and to be used for conformity determinations, the FAA explained in its guidance.
The agency also noted the expansion of the form’s use to include approving work on articles for return to service: “Many countries have indicated to the FAA that an FAA Form 8130-3 form [sic] on a used product, filled out for return to service, will be acceptable documentation rather than requiring the tag to be filled out as an export airworthiness approval.”
EASA’s first bilateral agreement, with special conditions to address significant regulatory differences between the U.S. and EU, came into force in 2011. The supporting technical documents for airworthiness and maintenance were based upon similar long-standing U.S. agreements with Germany and France. The current versions have undergone a combined 14 revisions. Change 8 of the MAG, which entered into force in 2021, continues to require an FAA Form 8130-3 from a PAH with every new part installed during maintenance or alteration—despite no changes to the special conditions.
The agencies cannot ignore the fundamental purpose of a bilateral: mutual acceptance of each other’s aviation safety systems and regulations, except as set forth in the special conditions. Under that premise, it is clear the only FAA Form 8130-3 required from a U.S. repair station is after the maintenance has been performed under U.S. regulations.
That interpretation is consistent with previous bilateral maintenance agreements between the U.S. and its European allies with respect to parts documentation on maintained articles. No previous understanding among the aviation authorities required a form for new replacement parts installed during maintenance. The attempt to justify the obligation under the export requirements of the Technical Implementation Procedures (TIP) belies the reality that the TIP does not apply to maintained articles and is negotiated separately from maintenance agreements.
How are decades of effort developing international harmonization serving aviation safety and the aerospace community today? Supply chain issues are a chief concern, and there are no safety issues with the American system. Yet the two prime international regulators are at loggerheads over the installation of airworthy parts because documentation preferred by one is not required by the other. Thousands of parts sitting on shelves for want of paperwork serve neither safety nor the aviation industry—particularly when the form required by EASA states that it does not constitute eligibility for installation without further action by a maintenance provider.
The FAA was collaborating with international partners before EASA was a glint in the European Parliament’s eye. Yet as the European agency’s international prominence grows, its preferences are threatening the mutual acceptance of the American and JAA aviation safety systems out of which it was born.
Marshall Filler, Sarah MacLeod and Christian Klein are managing members of Obadal, Filler, MacLeod & Klein and senior leaders of the Aeronautical Repair Station Association. Brett Levanto is vice president of operations for both the firm and the association.