How OEMs And MROs Are Ensuring Safe Water Onboard Aircraft
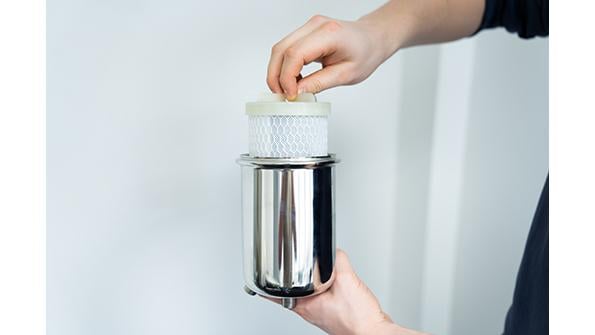
When boarding an aircraft, most airline passengers and crewmembers take for granted that there will be functioning toilets, wash basins, faucets and safe drinking water. To ensure this, operators focus a considerable degree of maintenance attention on the underlying infrastructure behind the onboard water and waste management systems. In recent years, at least some of the maintenance intensity has been mitigated through remedial measures on the part of system OEMs and MROs.
Ryan Havill, senior manager of business development for Collins Aerospace, cites a few examples of the issues facing maintenance crews. For instance, corrosion due to poor water quality can escalate the maintenance needed for lavatory water heaters, faucets and toilet rinse valves.
“Lavatory water heater maintenance can also increase if excessive water pressure oscillations have occurred,” Havill says. “Also, erosion due to extreme environmental conditions has caused maintenance issues with the gray-water drain masts, located on the external lower surfaces of the aircraft.” He also points out that toilet flush valve maintenance needs can increase if certain objects are thrown in the toilet and flushed.
At Collins Aerospace, Havill says engineers continue to use materials with enhanced corrosion-resistant properties and are taking steps to keep water away from the control parts of motor valves. “For example, greater structural strength has been designed into the latest lavatory water heater on the Boeing 777 to combat water pressure oscillations that occur,” he says.
Even legacy potable water systems generally use components that are very robust, according to Paul Koenig, aircraft systems engineer at Lufthansa Technik (LHT) in Frankfurt. He cautions, however, that there can be issues with components that are subjected to freezing temperatures, such as drain valves, as well as those components in contact with hot water, such as lavatory heaters, which are subject to calcification.
“Waste systems [also] bring their own set of maintenance challenges,” Koenig says. “Of note would be the waste tank inlet, the liquid-separator and the vacuum blower. These components are the ones farthest downstream in the waste management system.”
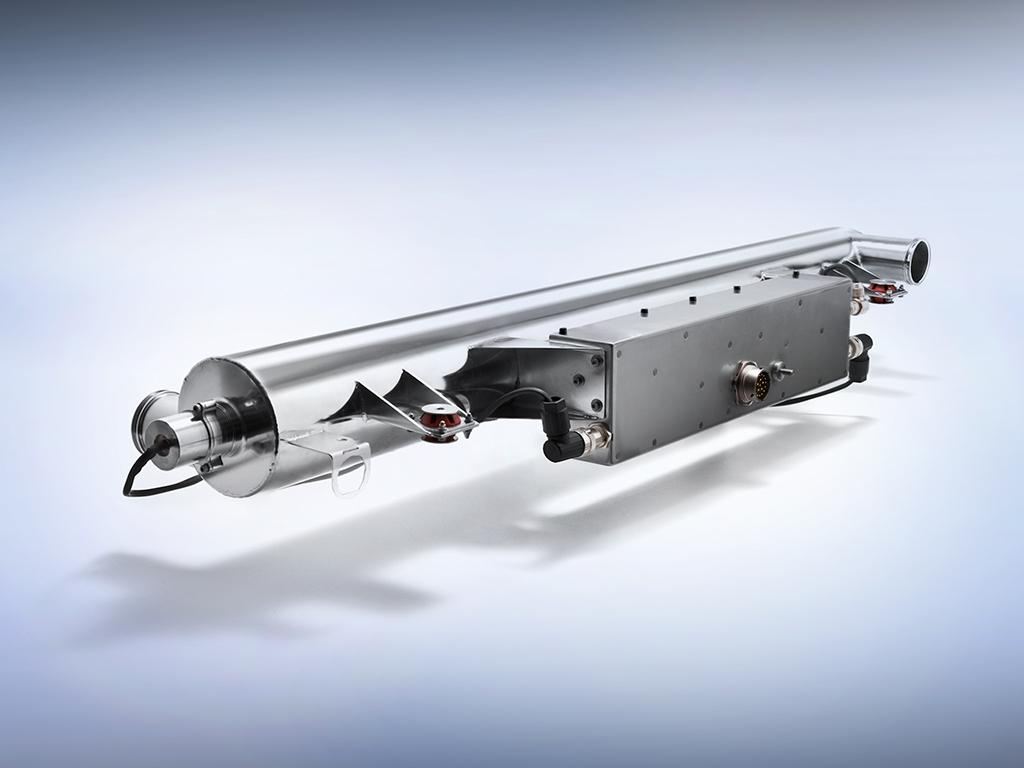
Koenig says corrosion is generally not a major issue with the waste system tubes since they are all made of corrosion-resistant materials, including polymers, stainless steel or titanium. “But there is corrosion in some components—as examples, the lavatory water heaters or vacuum blowers. However, they are usually not removed before functional failure occurs, due to other wear-and-tear issues occurring,” he says.
To address this, Koenig says LHT has developed repairs and upgrades for these components, incorporated in a shop overhaul, which often permits greatly extended times on-wing.
Koenig says the biggest challenge for potable water systems is to keep the water quality in line with regulatory requirements. To assure this, routine and nonroutine disinfections are usually done using hydrogen peroxide or chlorine. Although Koenig says these are potent methods, the results may be unsatisfactory.
“Since disinfection procedures can take quite long—up to 36 hr.—water-quality issues can be a real problem for airline operations,” he explains. “On top of that, the success of a disinfection procedure is not guaranteed and the airline might be required to repeat the procedure on short notice. In worst cases, this can result in multiple downtimes within just a few weeks.”
Koenig notes that removing contaminants, such as grease, from the potable water system is a difficult task, since most cleaning agents, such as soap, are prohibited. He says LHT has invested in developing alternative disinfection procedures using ozone or hot water.
“Although a hot water flush is very effective in removing contaminants like grease, it can damage the components installed, because potable water systems are limited to certain maximum water temperatures,” Koenig says. “To operate safely within those limits, we have invested in tooling that allows flushing the system quickly at precisely controlled and monitored temperatures.”
In the case of waste management, Koenig says the largest maintenance burden is due to blockages. To address that, LHT worked with Test-Fuchs, an Austrian test systems expert, to develop a proprietary product called WaLiClean.
“WaLiClean is used for preventive maintenance of the waste tubes and cleans them very effectively,” Koenig says. “Compared to traditional methods using specific cleaning chemicals, WaLiClean uses only citric acid, which is environmentally harmless and allows us to dispose of the removed waste and cleaning fluid into the public sewer system.”
But keeping the tubes clean does not prevent all clogs, especially those caused by foreign objects—usually trash—flushed down the toilets, resulting in substantial system performance degradation. The traditional method of clearing the blockages, Koenig says, is a manual one: determining the location of the clog inside the tube and disassembling that part of the system to clear it.
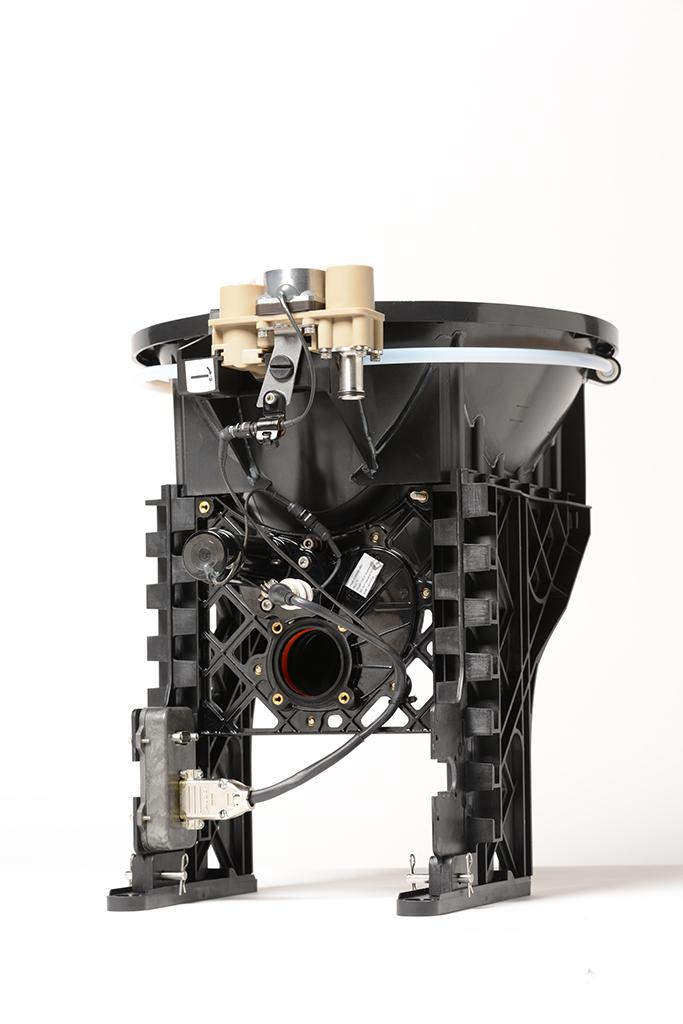
“This can be a labor-intensive process, since the tubes are not always easy to access, with some located in the wingbox area requiring passenger-seat removal and cabin floor opening,” Koenig points out. “To avoid this time-consuming and dirty task, we developed a tool that applies negative pressure in a reversed-flow direction. We can therefore suck the clog out of the line and dispatch the aircraft quickly.”
At Diehl Aviation, a Germany-based supplier of onboard water and waste management equipment, a two-stage ultraviolet (UV) water treatment system is being offered, which Rolf Kessler, the company’s chief expert of engineering systems, describes. “First, the water, which is constantly circulating, is disinfected with UV light directly when the water tanks are filled and then permanently by a UV lamp within the circulation system,” he says. “Thanks to the permanent onboard disinfection, we were able to extend the system maintenance intervals from three to six months. Moreover, we guarantee the high quality of drinking water at all times.”
Kessler further notes that in the case of wastewater systems, there has been a change of concept—from “absorbing” to “separating” filter technology. “Basically, separating filter technologies have longer service lives and do not clog as quickly as absorbing filters,” he says.
In another development, Diehl Aviation has managed to significantly reduce the number of parts in its onboard water systems. One way of doing this has been by moving from two tanks to a single unit on some long-haul aircraft, cutting weight and fuel costs. Further weight reduction has also been achieved through the use of new composite manufacturing technologies, such as automated (advanced) fiber placement.
“This means that fewer metal components and more components made of CFRP [carbon-fiber-reinforced polymers] or GFRP [glass-fiber-reinforced polymers] are used,” Kessler says. “We have also developed a sustainable water filter technology with our Greywater Reuse Unit, which reduces CO2 emissions and thus the ecological footprint. It saves not only water but, thanks to its low weight, also fuel—along with low maintenance and no constraints for the passengers.”
Diehl Aviation also provides the capability to optimize the maintenance of drinking water and wastewater systems, with the application of special sensors and software solutions that enable the early detection of contamination, according to Torsten Bottger, vice president of engineering. “Many customers are currently still satisfied with the usual methods and measures for predictive maintenance, which is why these solutions are not yet actively used,” Bottger says. “However, we are sure that this will change soon.”