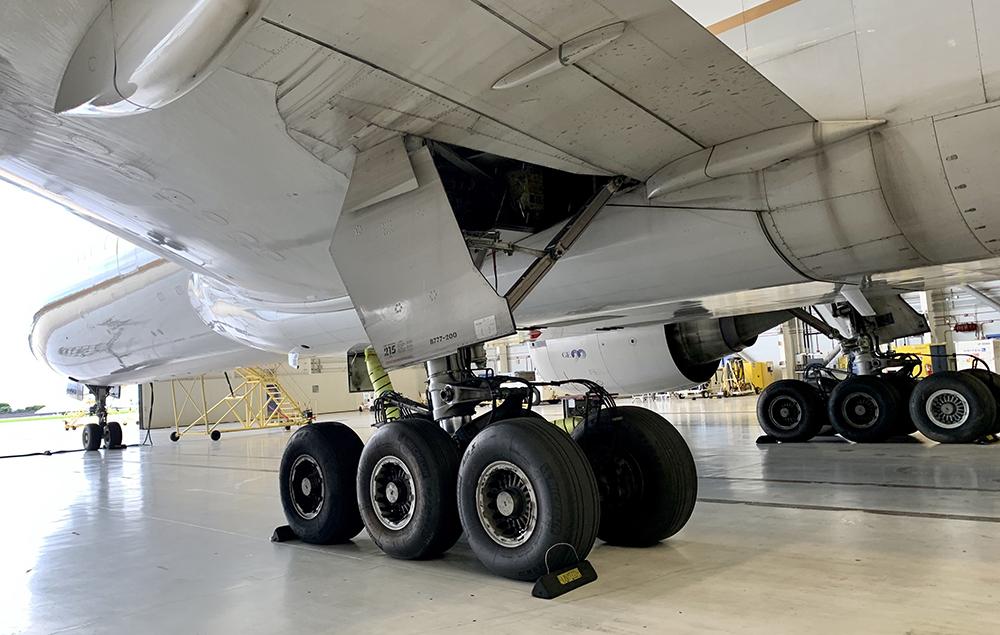
Credit: Sean Broderick/AWST
Some U.S.-based repair stations with European Union Aviation Safety Agency (EASA) approvals are getting pushback from that agency and the FAA on an approved method of showing a new part is traceable to the manufacturer, prompting the Aeronautical Repair Station Association (ARSA) to ask that FAA...
Subscription Required
This content requires a subscription to one of the Aviation Week Intelligence Network (AWIN) bundles.
Schedule a demo today to find out how you can access this content and similar content related to your area of the global aviation industry.
Already an AWIN subscriber? Login
Did you know? Aviation Week has won top honors multiple times in the Jesse H. Neal National Business Journalism Awards, the business-to-business media equivalent of the Pulitzer Prizes.