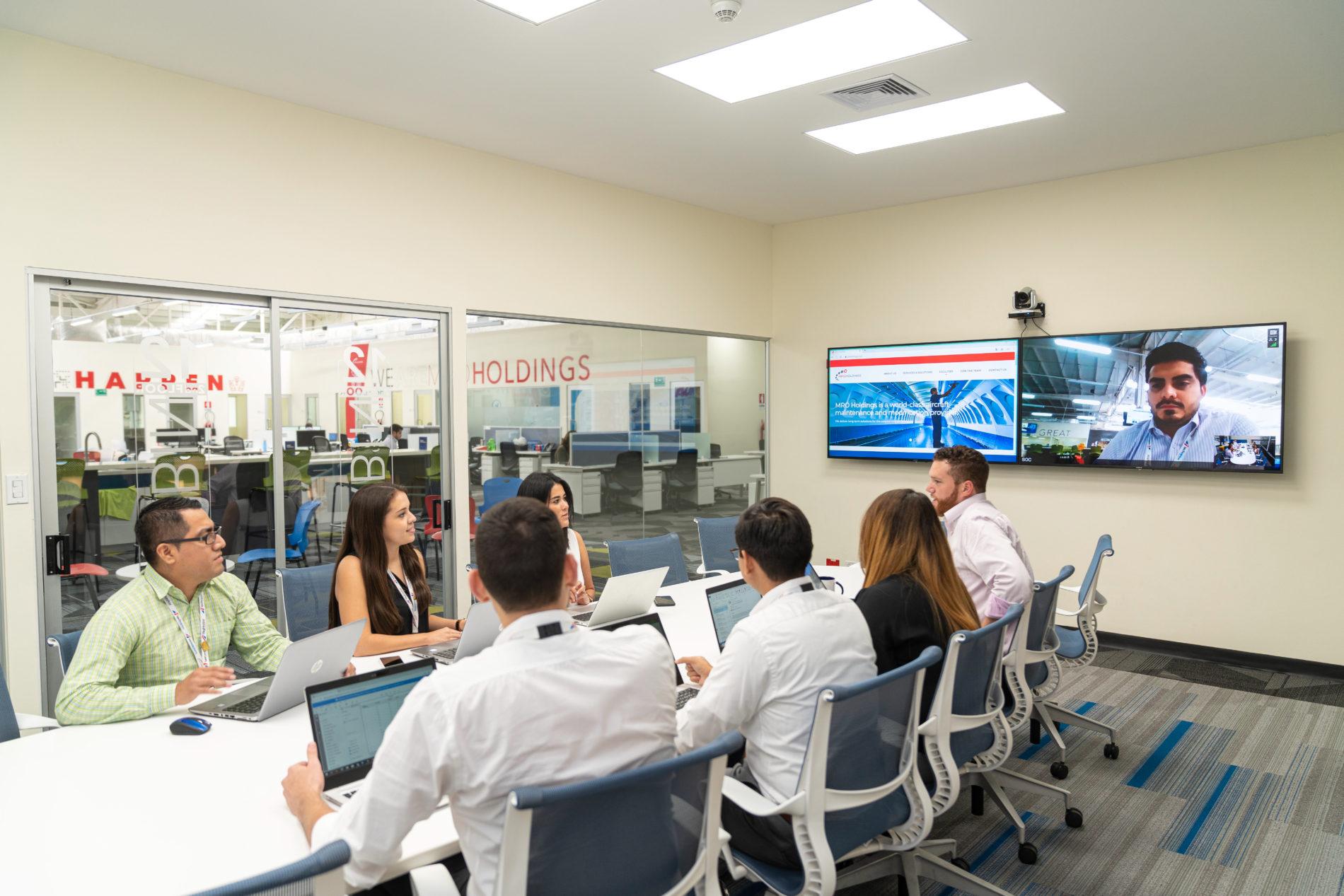
The use of remote collaboration tools within MRO has been receiving extra attention since the FAA released long-awaited guidance on March 31 broadening the use of remote video feeds for tasks such as inspections, training and tests in response to COVID-19 social distancing. However, these technologies were already gaining traction prior to the novel coronavirus crisis—and some MROs are using the opportunity to innovate their businesses.
According to an audience poll during Aviation Week Network’s MRO Compliance During COVID-19 webinar, 67% of participants were already investigating remote collaboration technology before the COVID-19 crisis, 19% have started pursuing it since the pandemic broke out and 9% now intend to look into the technology.
“In terms of remote connectivity, using tools to engage over distances is not a new emergence—it’s not something that the switches were flipped on just because suddenly inspectors, customers or other parts of the supply chain had to stay home,” explains Brett Levanto, VP operations at the Aeronautical Repair Station Association (ARSA), which has been working to broaden understanding of remote technology usage within MRO for several years.
Levanto points to ARSA’s foundational concept “that what’s not prohibited is allowed,” so, “actually, there are few regulatory limitations on your ability to use remote connectivity tools. In fact, most of those limitations come when there is just a requirement that the agency approve your process. It’s not even specifically related to the tools you happen to be using,” he explains.
According to Levanto, what it boils down to is working with regulatory agencies to ensure that visual inspections using remote tools provide “the same level of visual acuity and ability to inspect the element as if you were in-person, on-premises” to confirm the work was performed properly. “If you can do that using your tools, then you’ve just crossed a big hurdle,” he says.
Levanto notes that ARSA has found most remaining reluctance about remote collaboration technology is not coming from regulators, but rather from customers or other suppliers missing “a certain level of physical touch.” However, one MRO is banking on the use of virtual relationships to increase customer trust.
MRO Holdings launched a new business unit called MRO Solutions in summer 2019, which centralizes planning, production control, engineering and supply chain functions into a single off-site system operations center. “The vision at the time was to develop a virtual relationship using audio/visual technology that allowed some of our off-site experts to continue experiencing that same planeside feel, but also to do it with a smaller, highly experienced and knowledgeable workforce than if we had tried to provide this on-site at each MRO,” explains Gregg Brown, VP of compliance and technical solutions at MRO Holdings.
This virtual relationship approach has already provided great results for the company, according to Brown. “In one unique certification event in this past month, we were able to facilitate a remote inspection for the regulator for approval of a facility expansion at one of our repair stations,” he says. MRO Holdings used a video conferencing system on a mobile device to function as the “eyes and ears for the inspector,” which enabled the inspector to remotely see the entire facility, receive electronic documents, and take digital photos and videos through the system.
Brown says the inspection itself took approximately three hours and allowed the inspector “to see every single thing that they would have seen if they would have been on-site” while providing even more digital evidence than the inspector normally would have obtained. “It allowed for a timely approval for the facility to be in use immediately afterwards. From a timing perspective it had the potential, for a CapEx-intensive project, to sit idle for months—if not longer,” says Brown. “But instead it’s now already being used as it was intended, so it was a great outcome.”
While MRO Holdings is all-in on video inspection technology, Brown is still skeptical about the practical applications of remote technologies such as drone video inspections. “We still find it difficult to figure out how to cash the check on that. I think the opportunities are going to be more immediate and there are some very interesting investments to consider in the near-term, especially using the automated devices for inspection of aircraft—even remotely,” he says. “If we are able to assure ourselves that automation is able to perform at the same level as the human, generate the same findings and not miss defects at the same human level, there’s a real business case to be made that can allow us to leverage that human expertise in more critical areas and save considerably in the amount of ground support equipment and other things that we purchase and maintain today.”
Despite current limitations, Brown believes COVID-19 may provide opportunities for innovation within MRO. “I think we’re in a rapidly evolving landscape for the foreseeable future,” he says. “I think that this crisis is going to spur some really innovative thinking, and I’m really excited as a technology geek to watch this happen."