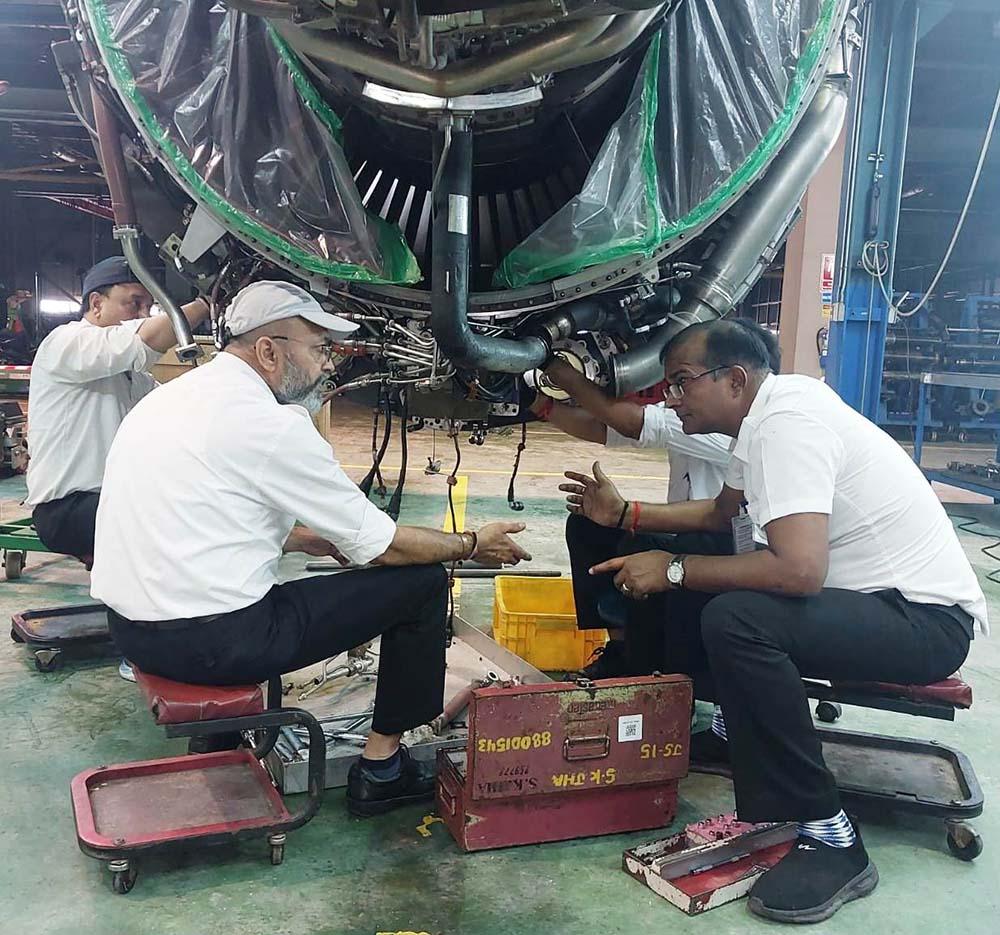
A broad overview of India’s MRO capabilities reveals sharp contrast in capability development. On one hand, India’s airframe maintenance capabilities have grown by leaps and bounds. Now, almost 90% of domestic airlines carry out airframe maintenance in-house. On the other hand, there is a huge gap in the engine and component overhaul segment.
India currently has about 700 commercial aircraft and, when considering recent orders from Air India, Akasa Air and IndiGo, this number will shoot up to more than 2,000 over the next five years. Typically, a jet engine requires a shop visit after 10,000 flight hours or 6,000 flight cycles, and it takes around 60-90 days for a complete jet engine restoration.
It does not require an expert to predict that India’s engine MRO facilities are far from developed enough to meet the engine overhaul demands over the next few years, with Indian MROs losing a huge chunk of business to foreign counterparts.
AI Engineering Services (AIESL) is currently the only MRO in India providing engine MRO services. It is the only engine repair station in India certified by the FAA, European Union Aviation Safety Agency and India’s Directorate General of Civil Aviation (DGCA) that has full capability for CFM International CFM56-5B/-7B, GE CF6-80C2, IAE V2500-A1 and Pratt & Whitney PW4000 engines. It also has partial capability for GE90 and GEnx engines and a variety of APU types from Honeywell Aerospace and Pratt & Whitney.
AIESL’s repair shop is fully equipped with machining capabilities and a computerized test cell with 100,000-lb. capacity. “We are capable of overhauling 100 engines per annum currently, with single shift working. We can easily double our capacity in two years,” says CEO Shri Sharad Agarwal. But is this enough?
With Safran’s upcoming engine MRO facility in Hyderabad, things are looking brighter. AIESL is already working with Safran to expand its capability to include Leap 1A and 1B engines, which power Airbus A320neo and Boeing 737 MAX aircraft. When asked about a possible joint venture with Safran, Agarwal said: “It is definitely a possibility. [The] Indian MRO space is less of [a] competition and more [about] complementing each other.”
In terms of how Indian MROs are expected to cater to the engine overhaul demand created by the huge influx of aircraft, Agarwal does not expect AIESL to stand alone. “With more than 1000 Leap engine-powered aircraft on order, no single shop can cater to all the demand,” he says.
Aside from looking at external OEMs as potential partners, AIESL is also constantly ramping up its capabilities and services with small wins. The company recently received Civil Aviation Authority approval from Cayman Islands and it obtained DGCA approval to perform borescope inspections on Leap 1Bs. AIESL’s Nagpur facility performed its first C check for an international customer in late 2023 in just 15 days. The facility also expected to have completed maintenance for 200 aircraft by the end of May.
The tides of change are slowly tilting in favor of India’s MRO industry, and the country’s MROs are gearing up to grab a larger chunk of the pie from the huge business that is about to arrive.
When considering India’s broader MRO environment, inside sources claim that almost 90% of the airframe maintenance work is done in-house. “Hardly any domestic players send their aircraft outside India for airframe maintenance,” says one source.