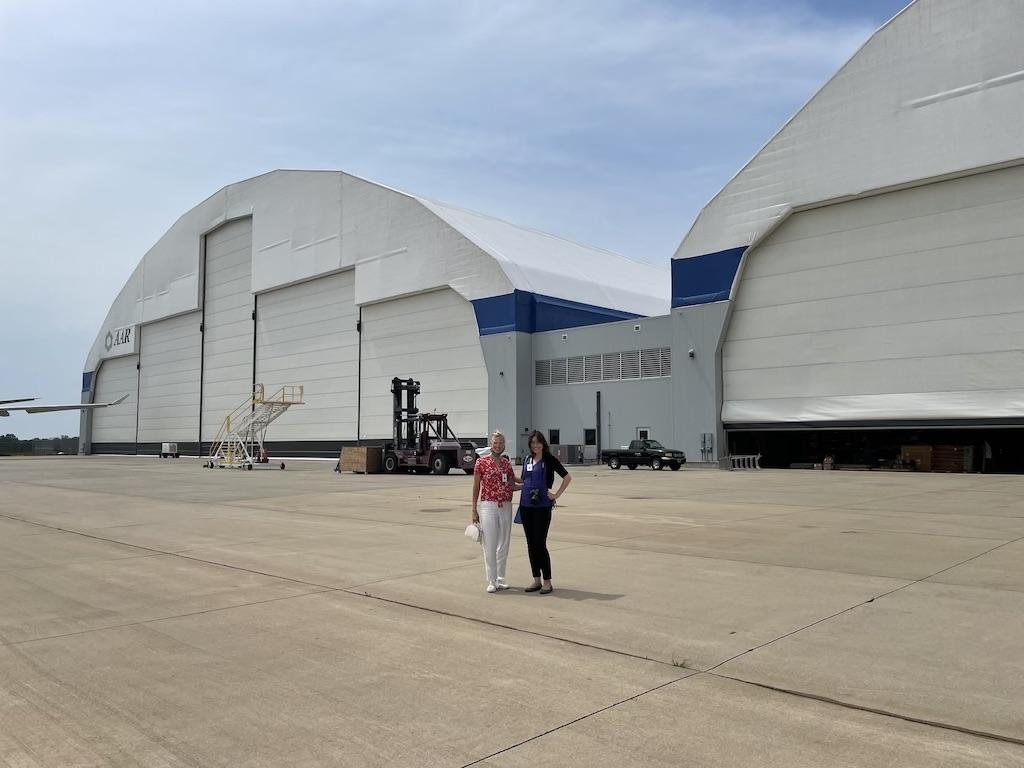
It’s August, time of the road trip here in the U.S., so my colleague Lindsay Bjerregaard and I drove west from Chicago to Rockford, Illinois, about a 2-hr. drive, to visit AAR’s facility there.
It’s always fun to visit someplace you haven’t been to, right, and neither of us had toured this AAR facility.
Yeti coffee mug beside me, off we went. We avoided traffic and were making good time until we hit the severe thunderstorm that our phones were alerting us about. Two hands clutching my steering wheel as tight as my fingers would allow to try to avoid the lane change the sudden high wind was trying to execute, onward we slowly drove through the downpour. Midwest storms of this magnitude never last long, so we got out of it before arriving at AAR’s facility (although we later learned the storm knocked out a lot of power lines and trees).
What we witnessed at AAR’s Rockford facility is a story that bucks the typical pandemic story.
The facility actually has been steadily expanding its work and workforce. It’s grown from 123 employees pre-pandemic to 237 now, according to Theresa Wiegert, an AAR human resources generalist. It landed a multi-year heavy maintenance agreement from United Airlines in April.
Walking through the two hangars, we saw a diverse workforce who looked engaged. We spoke with at least five women on the floor. We learned about the company’s mission to go paperless and we talked with mechanics and leads to see what impact that would have for them on a day-to-day basis.
The MRO facility was the one of the first, if not the first, to become an FAA-approved SMS facility (in Nov. 2020). Like any big program such as this, you don’t just say you’re going to do it and flip a switch—it’s a process. However, SMS seems ingrained at AAR’s Rockford site and now the majority of reports filed are proactive instead of reactive—i.e. employees identify and report things that might need to be fixed or changed to prevent a safety incident. In speaking with several employees, they say SMS has reinforced the correct processes and who to identify if they think something should change. They like it.
This facility didn’t quite take off as AAR had hoped it would when it opened in 2014, but from what we saw, there are a lot of positive things happening—and it really was a joy to speak with several of the people, in a variety of roles, who are making it happen.
Watch the MRO Digest next week for more from our trip.
And speaking of journeys, I’m working on Inside MRO’s editorial plan for next year. What content or data would you like to see? What would be helpful to you? Please contact me at [email protected] with your ideas. Thank you!