Simplifying Aircraft Waste And Water System Maintenance
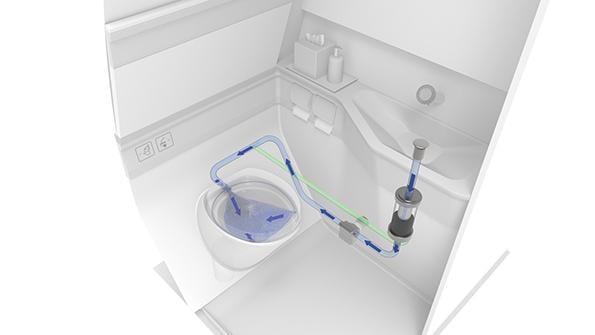
Diehl Aviation says onboard water reduction, such as gray water reuse, can save up to 210 kg on a Boeing 787 long-haul flight.
The complex piping and filtration systems that underpin airborne lavatories and galleys on commercial and business aircraft continue to evolve, as OEMs strive for lighter weight, enhanced reliability and, more recently, built-in health monitoring and diagnostics. Some understanding of onboard water and waste management issues, and their maintenance implications, helps clarify this trend.
“The maintenance intensity of the potable water supply is manageable, while that of wastewater-system-handling is more involved,” says Jan Boris Philipp, head of research systems for Diehl Aviation. “The main task for potable water maintenance is to regularly clean, decalcify and, in some cases, disinfect tanks, pipes and valves. The effort required for this purpose is reasonable and can usually be easily planned. For wastewater, the situation is different.”
Philipp points out that wastewater is classified as either “gray” water, which is generated by hand-washing in lavatory or galleys, or “black” water, which contains excrement from the toilet or food leftovers from the galleys.
“Systems that handle black water require more than average maintenance because they are dealing with aggressive mixtures that have to be collected in tanks, separated and disposed of on the ground,” Philipp says. “The aggressive environment which the components and sensor technology are exposed to can cause much more frequent impairments and must be checked much more often to determine if any parts have been negatively affected.”
Even so, airlines tend to see waste and water systems as among the least of their worries—until something goes really wrong, says Teddy Gil, chief administrative officer of Sheffield Aerospace, an aviation engineering consultancy in Texas.
“This is because, typically, these systems are not considered airworthiness-critical. That is far from correct,” Gil says. “Flight delays have been attributed to inoperative and/or clogged waste systems, because passengers inherently tend to use the toilet to dispose of wrong or oversized items, clogging the toilet and even the drain lines. In rare cases, the systems’ valves are negatively affected by these objects, requiring their removal for cleaning and repair.”
Clogs also can result from poor design, specifically in cases where the OEM-designed drain lines fail to meet minimal clog-resistance standards. One example Gil cites involved an Airbus A330 galley drain that had been designed with a 90-deg. tight elbow, which trapped debris.
“By slightly angling the tubing to the side, we were able to get enough clearance to install a larger sweep,” Gil says. “This design change did require a bit more material. However, at a minimal amount of additional cost, we were able to eliminate the problem altogether.”
Asked about improvements to potable water handling, Gil notes one pain point: coffee makers. “These have had their fair share of issues, ranging from overspills to poor water quality,” he says. “The new generation of coffee makers has been improved with the incorporation of better filtration, self-diagnosis and water cutoff to prevent overspills, along with reduced weight compared to legacy coffee makers.”
Chuck Zahnow, airframe technical representative for Citation and Hawker at Duncan Aviation’s Battle Creek, Michigan, location, agrees that waste management systems are more problematic in terms of maintenance and mitigation measures. “For potable water handling, it’s mostly a matter of filter changes and sterilization. On the waste side, the problem is corrosion and component failure,” he notes.
To illustrate, Zahnow says that on Citation jets, the waste tank is equipped with optical sensors that are prone to becoming coated with debris. Especially for externally serviced toilets, this can cause the sensors to incorrectly indicate the water level within the tank.
“The [tank] sensors are cleaned by a slinger, a device which sprays the tank with clean water,” he says. “Regular service is required to maintain a clean system to eliminate debris, which comes from a build-up of film from human waste as well as disposal of paper products other than toilet paper.”
Zahnow says corrosion is often the result of the chemical product added to wastewater for sanitation and odor control. “On the Citation line, we see this under the water tank, usually when the aircraft is in for a maintenance event that drives us to that spot,” he says.
The OEMs, Zahnow points out, have been addressing the corrosion problem under water tanks through the use of improved composite materials that provide greater durability. “With current designs, tanks are more robust, and it is rare to have to replace them,” he says. “At the same time, the trays under the tanks, which help to contain fluid leakage or small spills, [incorporate] more plastic. And we continue to see a lot fewer metal parts.”
Among the preventative maintenance trends Zahnow cites is the installation of optical sensors to aid in determining the toilet’s fluid level to avoid overfill. “Adding those sensors has achieved that goal, but it has led to some issues with the servicing process,” he says. “Most of the failures occur when the sensor is dirty and ‘thinks’ the tank is overly full, even if the tank is completely empty. In this instance, the fill valve will not open and allow for fluid to go into the tank.”
Water and waste management system OEMs are pushing weight-saving designs in such critical components as drain lines. “Lighter-weight metals and plastics are largely replacing heavier aluminum and stainless steel drain lines going from the galley,” says Jim Kimball, vice president of technical operations for FEAM Aero. “Also, with the vacuum toilet systems today, the waste lines have gotten narrower than they were with the old gravity-dump lavatories. Many are lined with Teflon to make them more resistant to the waste.”
From a maintenance perspective, Kimball says the waste lines are prone to developing scale deposits—especially in difficult-to-reach places. “Regular waste line maintenance, including frequent washings, is imperative,” he says. “If a waste line goes down, the airplane can be out of service for days while technicians tear the system apart to determine where the clog may be.”
Kimball says he is not aware of new technology that can pinpoint the location of an obstruction. “Finding it is still on the old-fashioned side,” he says. “However, there are companies developing cleaning products which can maintain the drain lines to like-new condition.”
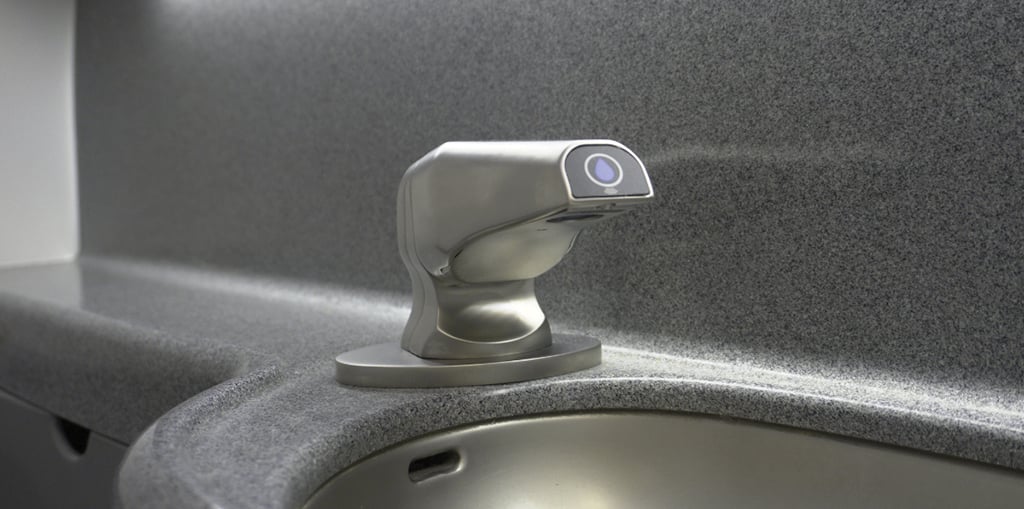
Still, new technology is making a difference. For airline passengers, using the lavatory is becoming a hands-free process. For example, Adams Rite Aerospace, a specialist in commercial aircraft cold-water systems, is fielding Touchfree, its latest suite of products that include sensor-controlled faucets, soap dispensers, flush switches, waste flaps and toilet seats.
“With Touchfree, we are combining infrared technology with the latest thermoplastic developments to make the aircraft lavatory more hygienic, but also more reliable and lighter,” says Ali Dadvar, vice president of sales and marketing at Adams Rite Aerospace.
The waste flap and flush switch are designed to be activated via an infrared optical sensor. “Our Touchfree products have the capability to have an additional printed circuit board for aircraft communication. However, the current version of the Touchfree products do not have this, based on airline feedback,” Dadvar says.
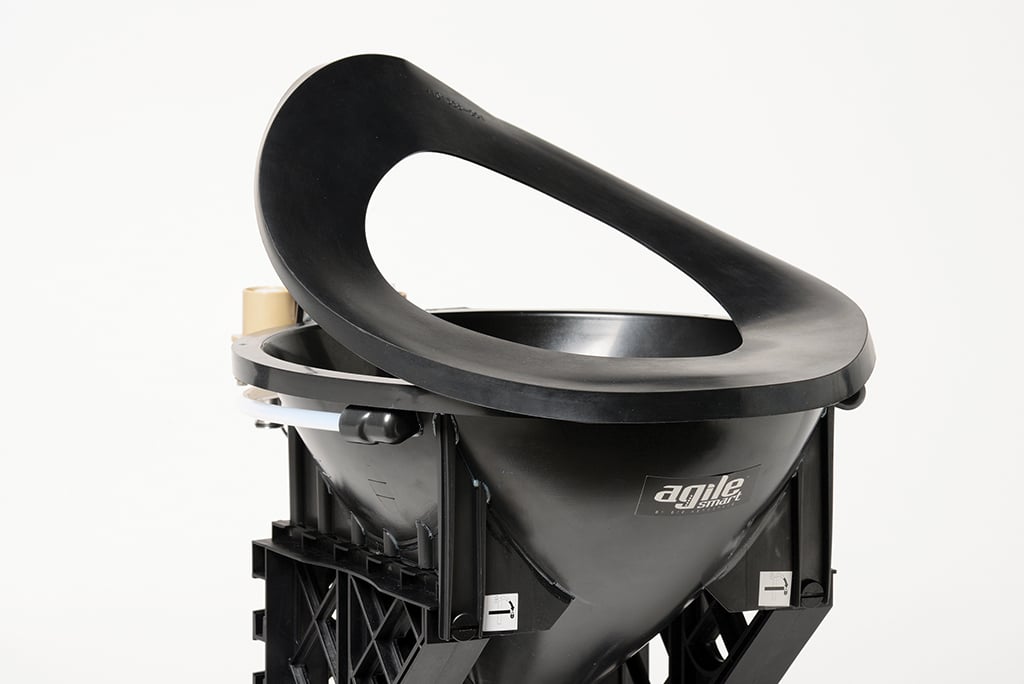
Collins Aerospace’s Agile Smart toilet offers built-in health monitoring, onboard memory for diagnostics and an RS232 interface for maintenance and fault communication, notes Don Roulett, the supplier’s business development manager. He says Collins Aerospace’s patented Splash Guard eliminates wastewater aerosolization into the lavatory and waste leakage around the bowl.
“A special focus was applied during the design of the Agile toilet, and it resulted in four times greater reliability than the previous-generation toilets,” he says. “It is currently installed on the Boeing 737, 747, 757, 767 and 777, as well as the Airbus A320.”
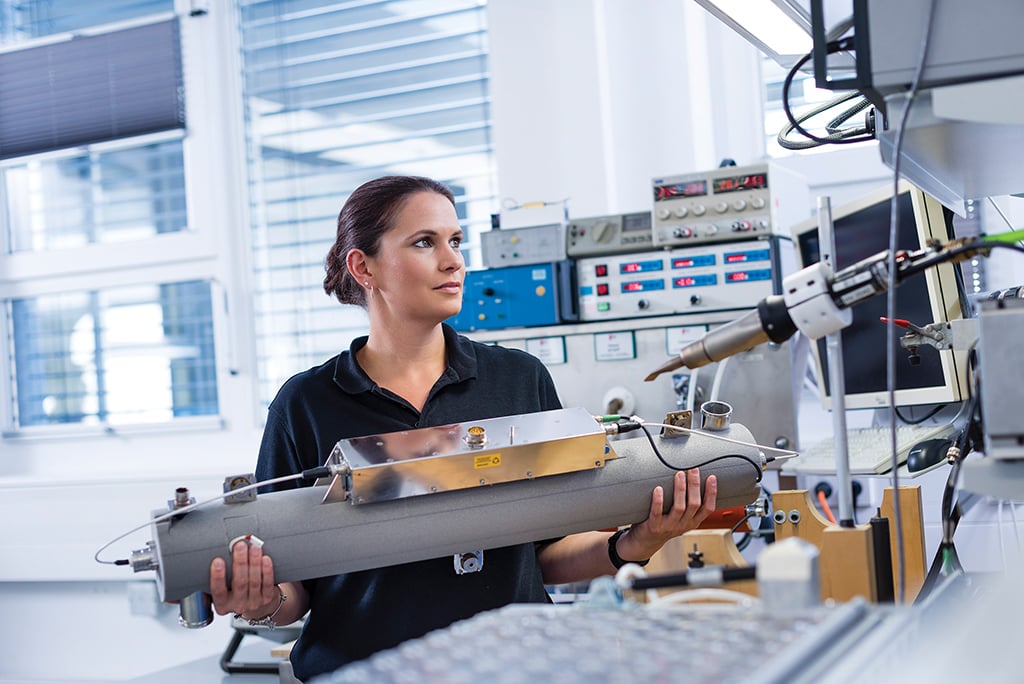
Diehl Aviation is working on predictive-maintenance research projects, such as a patented system to predict pipe blockages. The OEM also is participating in the i+sCabin2.0 research project that includes Safran and Thales as well as institutions such as the Hamburg University of Technology in Germany. “The project aims to collect data from the entire cabin—galleys, overhead bins, seats and from toilet assemblies,” Philipp says. “The goal is a smart cabin that anticipates and reports the need for maintenance and repair work on individual components.”
He also says that research continues into lighter-weight components, using a multifaceted approach. Diehl’s weight-savings research is based on three pillars. The first is focused on new materials such as carbon-fiber-reinforced plastic (CFRP) or titanium. Examples include titanium tanks developed by Diehl and its ultralight InnoLite toilet, launched in 2020. Made with CFRP, it is 20% lighter than previous models.
The second pillar is looking at water reduction. “Our Gray Water Reuse Unit collects gray water from the sink, treats it and uses it to flush the toilet assembly,” Philipp notes. “In a Boeing 787, for example, this can save up to 210 kg [463 lb.] in weight.”
System simplicity is the target of the third pillar. “The most recent example is our single tank for long-range aircraft,” Phillip says. “Until now, long-range aircraft have been equipped with two or three tanks for potable water or wastewater. Diehl now offers a single-tank solution in a long-range aircraft, which has a weight savings of 50 kg.”
Philipp says Diehl also has developed treatment systems applying UV technology to disinfect water during refilling. One is applied to the circulation system. “In the pipes, UV light continuously disinfects the water so that germs do not form or spread during the flight,” he says.