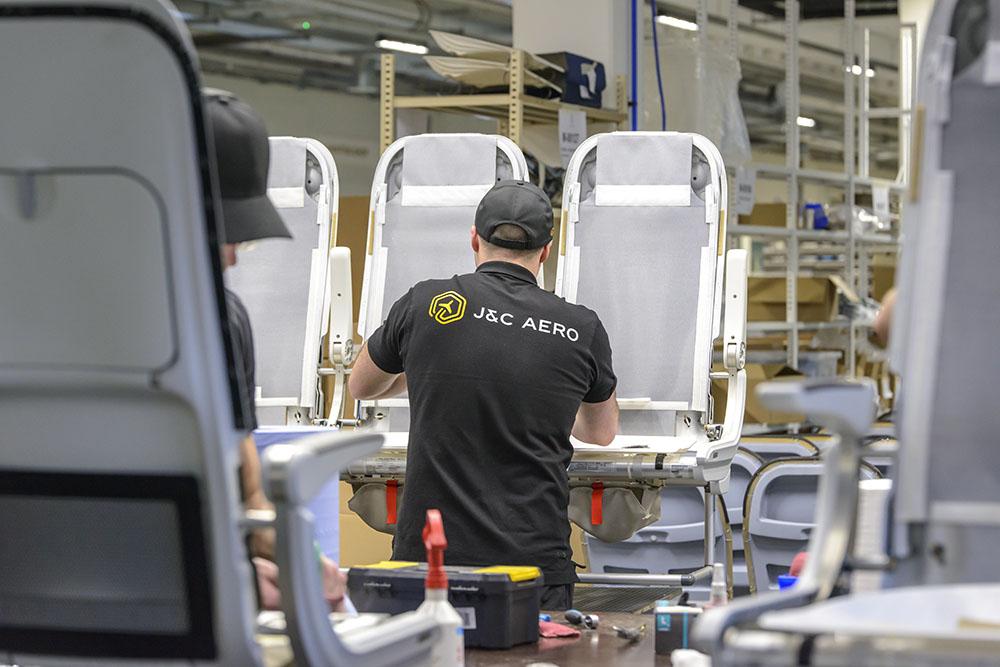
J&C Aero plans to deliver full-cycle cabin retrofit programs from its newly inaugurated cabin interiors facility in Vilnius, Lithuania. The facility will introduce turnkey aircraft retrofits, including new interior developments, certification, production and installation.
Maksim Jurkov, head of design at J&C Aero, tells Aviation Week there have recently been a few notable trends within cabin retrofits. For instance, he says there has been more focus on cabin interior quality and fleet standardization this year to provide easier, more effective maintenance that involves fewer resources from the airline.
“We have also seen airlines shifting toward long-term planning, versus the shorter-term planning we saw during the pandemic,” says Jurkov. He notes that planning is key and over 60% of J&C’s current projects were already planned for last year. “We have seen that Asian-Pacific customers tend to invest in premium economy and business class cabins, while many European customers prioritize seat pitch reduction to accommodate a maximum number of passengers,” he says.
The cabin interiors sector is also facing many of the supply chain issues that are affecting other aviation aftermarkets. “The interior segment is partially affected … and we have previously identified potential supply chain and sub-contracting issues, so we have been investing in internal capacities ever since,” says Jurkov.
J&C Aero is banking on the new 3,600 m2 (39,000 ft.2) production facility to reduce its dependency on sub-contractors and enable it to start manufacturing most required parts in-house.
The new facility is equipped with a full range of cabin interior capabilities, including machining, composites, painting and flatbed cutting shops, as well as cleaning, sanding, vacuum, foam and general workshop areas. J&C Aero’s in-house Design Organization Approval, Production Organizations Approval, Continuing Airworthiness Management Organization and Part 145 teams, together with electrical, livery, 3D printing and sewing units, have moved to the new cabin interior hub.
The company’s R&D department has also moved into the new facility and produces cabin components such as custom-shaped lightweight windscreens, moveable class dividers and integrated passenger information signs.
Jurkov says that in most cases, custom interior parts come with plug and play solutions that have forms and functions similar to the original parts. “This approach allows us to use existing attachment points while offering a modern design or upgraded functionality and ensuring there’s no weight increase,” he says.
J&C Aero expects to see significant benefits by moving operations and new capabilities under one roof, with Jurkov noting that improvements are expected in terms of technology integration, delivery of turnkey programs and business flexibility. He adds that new technologies and continuous training will be pivotal in this development.
“For the last several years, we have been heavily investing in process robotization and automation that allowed us not only to increase production rate, but also substantially cut our environmental footprint,” says Jurkov. “In some of our shops, we were able to reduce waste materials by almost 50%.”