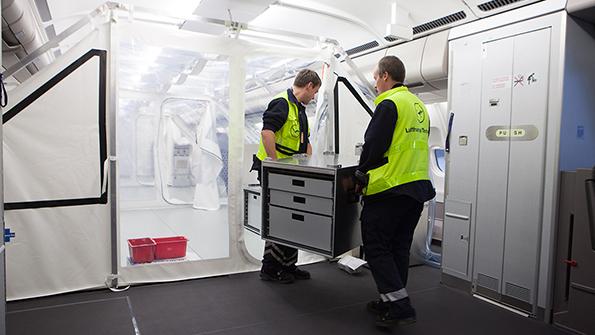
The novel coronavirus pandemic has seen passenger air traffic fall dramatically, but many operators and MROs are adapting to new demand during the unprecedented situation by pursuing temporary modifications for cargo conversions and medical transport.
For Lufthansa Technik (LHT), which employs approximately 1,000 people in its VIP and special mission aircraft department, COVID-19 is not the first pandemic to create demand for special aircraft used to transport and treat highly contagious patients. The MRO was commissioned by Germany’s Federal Foreign Office to convert an Airbus A340 into a special evacuation aircraft during the Ebola epidemic in 2014.
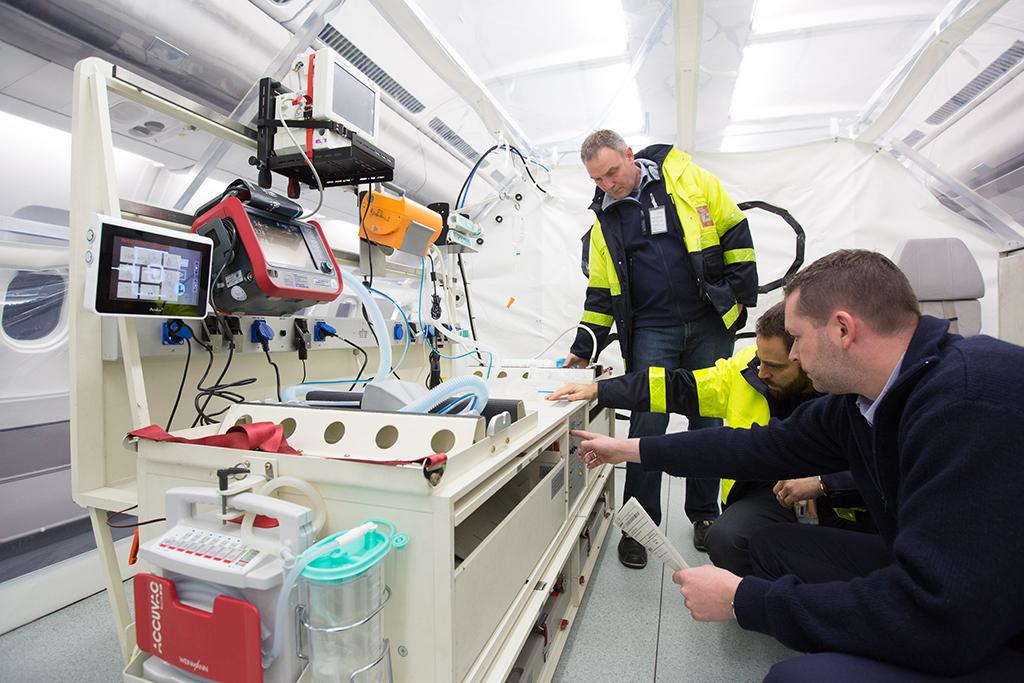
In addition to providing space for a patient transport isolation unit, the A340 required special adaptations to isolate crew, prevent contamination and supply power to systems for intensive care, ventilation and disinfection. LHT removed passenger seats, galleys and luggage bins to provide room for a patient transport isolation unit, which was surrounded by an airtight tent with negative pressure as well as two exterior tents to serve as buffers for entering and exiting the isolation tent. To prevent contamination in the event of a sudden pressure loss, LHT integrated flaps into the isolation tent structure that could open and safely collect the air. It also installed electrical connections and a special communication system for aircraft crew and medical staff.
An integral part of the design was LHT’s patient transport unit (PTU), which provides the necessary underlying infrastructure and medical equipment needed to transport intensive care patients on a large aircraft. LHT says it can be installed within minutes using seat-track adapters in any aircraft, and it is small and light enough to be easily handled by two people. The MRO is now in the concept phase to adapt the PTU with EpiShuttle, a single-patient isolation and transport system for providing intensive care monitoring and treatment. The company also says it has been in close contact with several air forces in Europe that are looking for medevac mission solutions for crisis situations such as COVID-19.
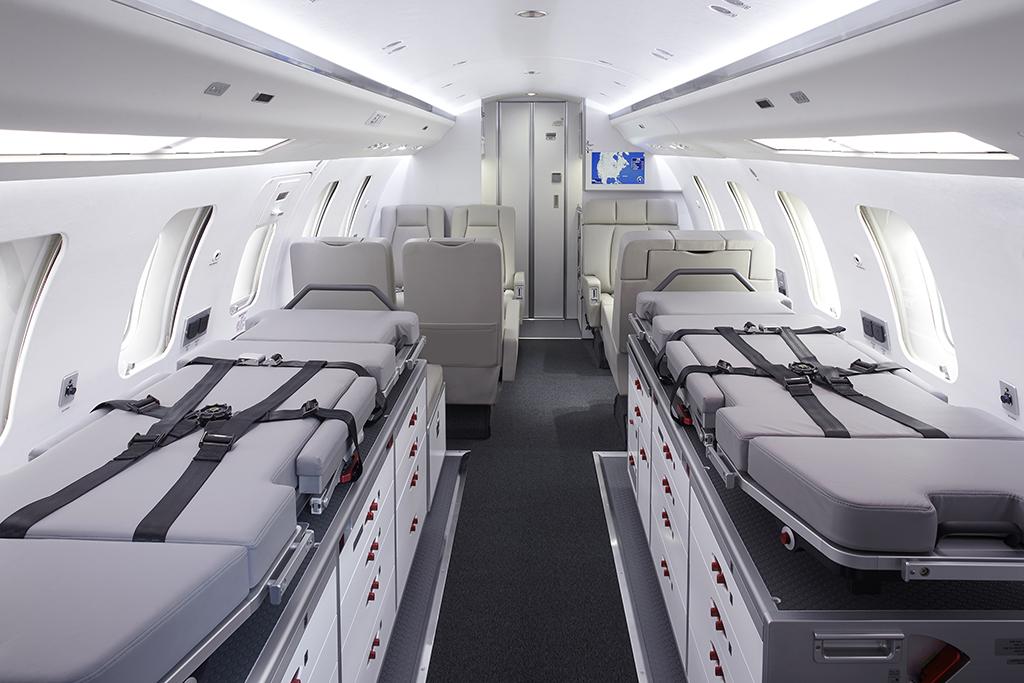
Canadian MRO Flying Colours Corp., which has experience converting aircraft ranging in size from the Beechcraft King Air to the Bombardier Q400 into medevac formats, points out that these try to replicate on-the-ground environments as closely as possible in the air.
“Creating the medical space requires an intelligent approach, some ingenuity and, on occasion, a bit of imagination,” says Sean Gillespie, executive vice president for operations at Flying Colours. He notes that in addition to forming close relationships with medical equipment suppliers, the MRO tries to maximize the use of space and to ensure that the equipment can be safely and securely installed. “Space and weight have to be taken into consideration, as well as the needs of attending clinicians so they have the best possible environment to deliver the best possible care. We need to consider patient access and egress—you don’t want to be lifting a critically ill patient over a set of obstacles,” he explains.
At the basic level, Gillespie says medevac installations incorporate stretcher beds, medical oxygen supply and seating for passengers and medical staff. More advanced, dedicated air ambulances are outfitted with full emergency equipment offering life- support systems for critical medical emergencies as well as soundproofing to reduce noise levels in the cabin. To incorporate specialized components such as these, Flying Colours also needs to obtain the appropriate supplemental type certificates (STC).
“This takes experience and can be extremely complicated, as the equipment will often incorporate complex electrical components, unusual materials that are not generally found in the aviation environment or specific items not normally used on aircraft, which means we have to do a lot of testing to make sure the materials can be validated for aviation use,” Gillespie says.
Flying Colours anticipates that it will receive more medevac-related requests after COVID-19—particularly for multipurpose interiors that can be easily swapped out as needed. One such example is a project the MRO began for aerial firefighting provider Conair Group in 2018, for which it is modifying six Q400MR aircraft with interchangeable interiors for passenger, cargo, combi-transport and medevac modes. The aircraft remain in cargo mode while firefighting operations take place, but the side wall fittings and alignment are designed so the custom interiors can be quickly changed as needed.
“The design of the interior change-out is influenced by the need to be able to make the swap-out of the components within a short period of time,” explains Gillespie, noting that Flying Colours aimed for a design that could be changed out in 6 hr. or less by a team of 6-8 people. “This was the initial request, and we even timed it with stopwatches to ensure we met the needs as requested.”
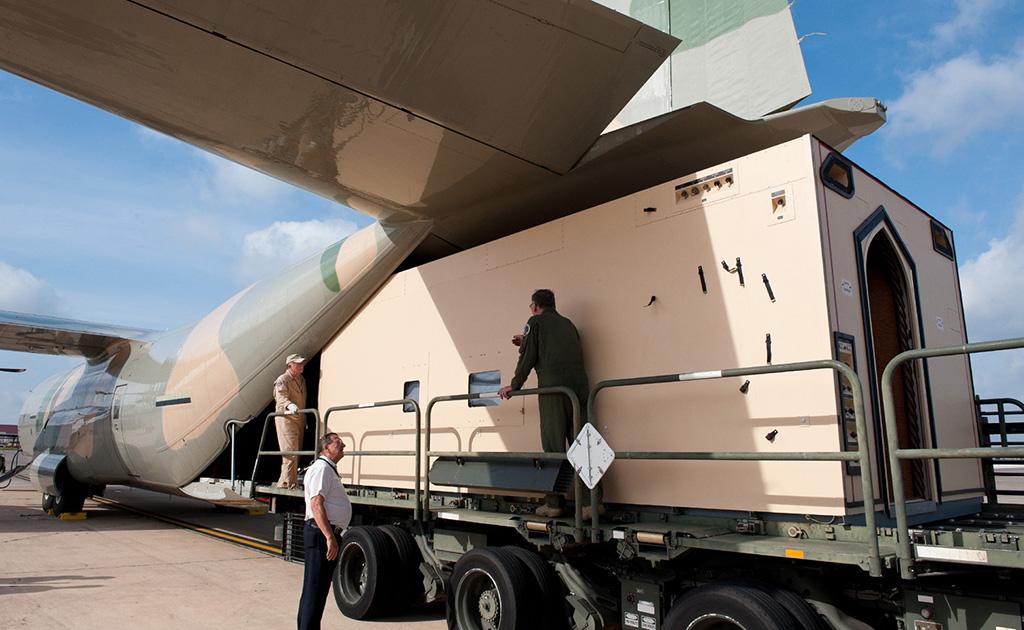
One company offering a unique take on transforming cargo aircraft interiors is Knight Aerospace, which designs, manufactures and installs custom modules that can roll on and off and then be locked into an aircraft’s cargo handling system. The San Antonio-based company describes the modules as being similar to “building an aircraft inside of an aircraft.”
“We’re giving our customers the ability to transform their cargo aircraft into multi-use aircraft. Having an aircraft on the ground is expensive, so we’re giving them the ability to transport high-level individuals, carry out medical missions and do various operations so they don’t have an aircraft on the ground,” says Michael Knight, vice president for sales and marketing.
The company recently began production of its universal patient module and aero-medical bio-containment module (ABCM), which builds on the VIP modules it has already been producing for government customers worldwide. Typically designed for cargo aircraft such as the Lockheed C-130 or Airbus A400M, Knight Aerospace’s modules have been produced with a heavy focus on elements such as acoustic and vibrational treatment, air quality and lighting to make traveling inside feel more like a commercial aircraft—and as close to a hospital setting as possible.
“One of the things that we bring to the table that’s very unique is pressurization. We can either pressurize our modules for negative pressure or positive pressure, depending on the kinds of patients that we’re trying to transport, so this starts helping you in things like contagion,” says Bianca Rhodes, president and CEO of Knight Aerospace. “For instance, if you’re transporting a burn patient, you want as few contaminants in the atmosphere as possible because infection is probably the biggest issue for a burn patient.”
Conversely, when it comes to contagious diseases such as COVID-19, the concern becomes more about preventing contamination from reaching crew. For example, Rhodes notes that during the Ebola outbreak, aircraft used to transport patients needed to be grounded afterward for decontamination.
“Separating the air crew from the patient and the medical crew is huge. You can take this structure, roll it in, lock it into the aircraft in an hour, fly your mission, come back, roll it off and you’ve not exposed the aircraft or the air crew to any of that,” says Rhodes, noting that the interior can be further enhanced to separate medical crew from patients.
To help design the medical modules, Knight Aerospace’s engineers studied operating rooms, ambulances and air medical helicopters to understand the nuances of transporting patients. The modules feature 30 air changes an hour, electrical components in the ceiling so wires do not become obstacles, and a sink component with hot water, refrigeration and a safe for controlled medications. Rhodes says other unique elements include horizontal and vertical railings for equipment storage and intensive care unit (ICU) beds that come out of the wall to allow full access to the patient.
The medical modules can also be taken off a cargo aircraft and operated on the ground once hooked up to a power source, so they could potentially serve as remote clinics or ICUs in areas with less developed medical facilities. Knight Aerospace expects the solution to have appeal for both military and international nongovernment organizations.
Since the COVID-19 outbreak, Rhodes says Knight Aerospace has worked with its initial customer for the universal patient module to expedite production and has since received several other requests, primarily from the air forces of various countries. It has also sold its first ABCM, which it expects to complete soon.