Complexity And New Technology Drive Cabin Modification Innovation
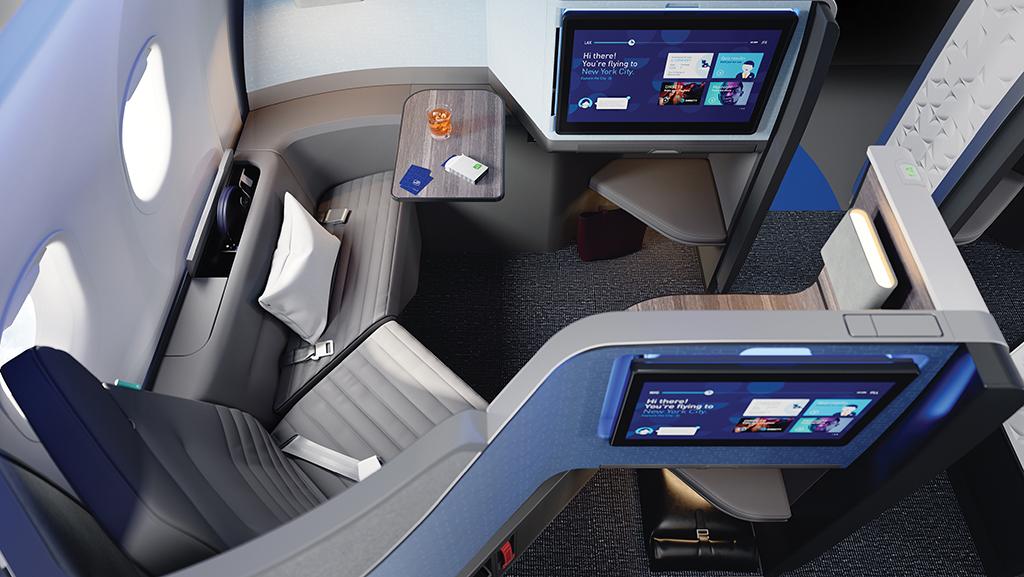
Business-first front-row seats are of increasing complexity in design, manufacture, maintenance and modification.
Cabin modification is a pressing issue for the commercial aviation industry as airlines seek to right-size their fleets after the sharp contraction caused by the COVID-19 pandemic.
Competing priorities, many of them interrelated, are further complicating an already intricate network of regulation, design, manufacture and installation. And the cabin interiors industry is responding.
“With respect to the differences between our recent cabin modifications and ones from even a few years ago, we do see a lot of relatively small changes that add up,” says Tim Lehnig, director of sales for interiors at Collins Aerospace. “What would have been considered an optimum cabin layout a few years ago would now be considered inefficient.”
Countervailing pressures include the drive for more space in premium cabins, plus more options behind the business-class divider, as well as the dichotomy between new narrowbody aircraft being designed both for ultra-dense, short-haul, maximum-passenger configurations and for more spacious long-haul configurations.
“[Layout of passenger accommodations (LOPA)] and interior products have gotten more complex, as airlines are all seeking to differentiate their cabins to achieve higher levels of passenger satisfaction while at the same time aiming to maximize the profitability of their LOPAs,” Lehnig says.
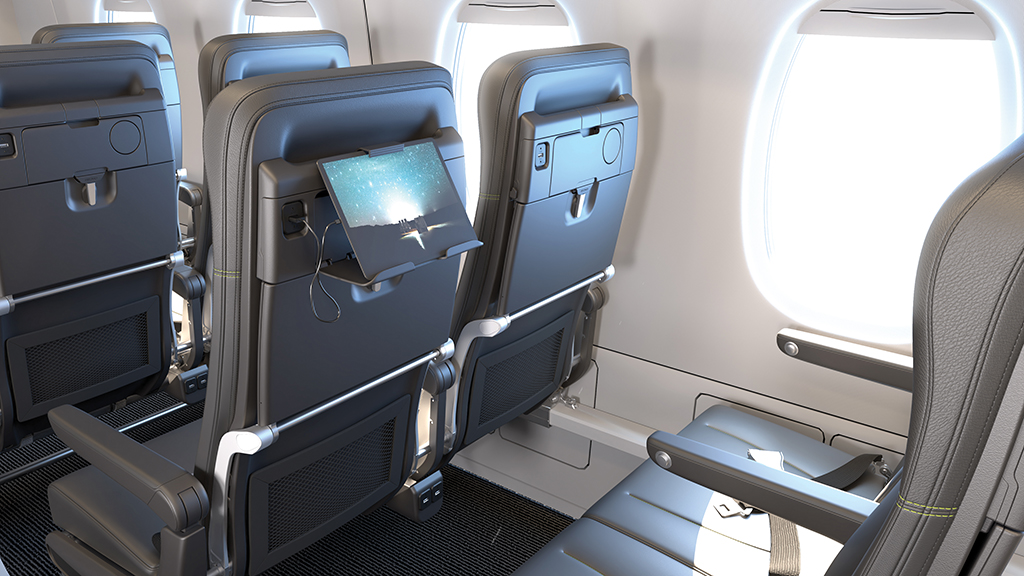
This complexity is a nose-to-tail issue for cabins. Up front, increasingly intricate business-class seats add density but also complexity, with stratifications appearing in seatmakers’ catalogs among airlines that are willing and able to design and operate bespoke seats, those that want substantial customization and those that are content with a more basic product. The trend of business-first front-row seats, such as JetBlue’s Mint Studio on its transatlantic Airbus A321LR or Virgin Atlantic’s Retreat Suite in Upper Class on its Airbus A330neo, adds a halo product but also complexity in design, manufacture, maintenance and modification.
Further back, the adoption of premium-economy cabins by more airlines, together with the growth in the cabin’s footprint aboard aircraft, drives the installation of additional cabin walls and other monuments, yet these interrupt the efficient tessellation of the cabin LOPA.
In economy class, airlines are seeking to differentiate through both the growth of extra-legroom economy seats as an ancillary option and the expansion of basic economy products.
At the same time, Recaro Aircraft Seating CEO Mark Hiller explains that “newer aircraft are subject to stricter safety and environmental regulations by authorities or aircraft OEMs.” He cites the growth of requirements such as the head-injury criterion for dynamic testing during seat certification, tamper-proof requirements for life vest pouches and other factors.
“This must be considered for new seats as well as cabin modifications,” Hiller says. “Ultimately though, this does not make a modification easier or harder; it is only a technical requirement that needs to be considered. Modern aircraft cabins support layout changes on aircraft even after entering service.”
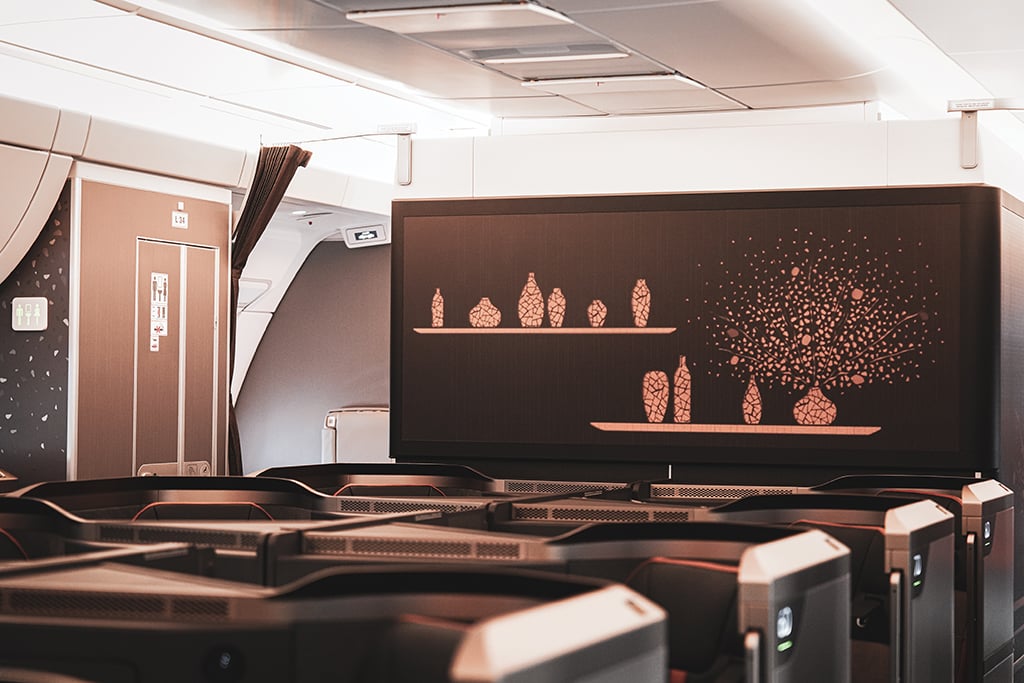
As the materials used to create modern aircraft change, so do the requirements for installing and maintaining them.
“The architecture of modern composite aircraft is significantly different and, in many aspects, more challenging than traditional aluminum aircraft,” says Collins’ Lehnig. “For us as an integrator, these changes translate into the use of different materials to control corrosion and strength. For example, on the [Boeing] 787, the seat tracks are different in both profile and material, so we are using titanium fittings for strength and corrosion control versus a more traditional aluminum profile.
“Another aspect that makes modern composite aircraft platforms more difficult to work on is the need for additional and more complex analyses and reports to support the certification of cabin modifications,” Lehnig continues. “This adds an additional layer of complexity that requires more engineering-intensive [integrated procedure trainings] and longer program lead times. An additional challenge is the availability of airframe data, which integrators are overcoming by forming new models of partnerships and collaborations within the industry.”