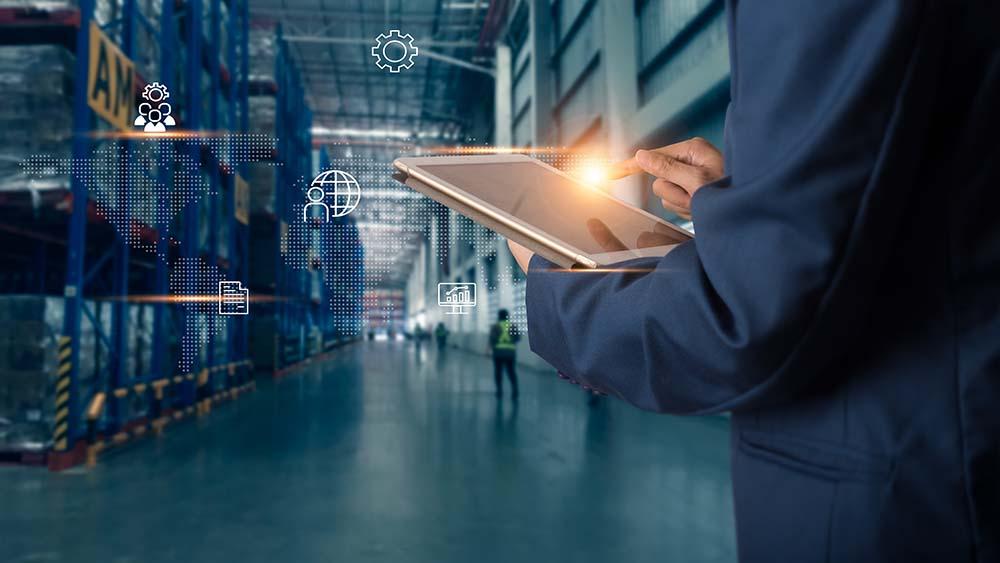
MIAMI—For years, when an airline or MRO was considering adopting a new MRO IT solution, it was customary for the considering managers to say, “no solution does it all.” That is likely still true, but software provider IFS is attempting to buck the trend by integrating its Maintenix product with the broad bundle of applications in its IFS Cloud platform.
Maintenix began more than two decades ago as an independent MRO application, and its development for defense aviation gave it very strong configuration capabilities that now aid airlines in regulatory compliance. The software advanced quickly, incorporating e-signatures in the early 2000s. Maintenix soon attracted many airline users, recently including Southwest Airlines, which executed what it says is the largest single conversion to a modern MRO IT system in commercial airline history. Acquired by IFS in 2016, Maintenix is now in discussions with another very large North American carrier.
All the while, IFS had been building a suite of applications for managing assets, people and customers for a wide variety of companies, including aerospace manufacturers such as BAE Systems and MROs such as Emirates Engineering and Revima. IFS says these tools can handle complex MRO, such as work on engines and landing gear. Human resources, procurement and other functions are also available.
A year-and-a-half ago, these capabilities were transferred to IFS Cloud, which it says is a highly flexible and economic way of offering a wide variety of tools—including predictive maintenance, artificial intelligence and machine learning—to companies inside and outside of aerospace.
IFS is now offering both airlines and aircraft MROs the opportunity to combine functions designed specifically for them with the much broader set of asset-, people- and customer-managing capabilities in IFS Cloud.
This is a multi-year ‘journey,’ as IT developers like to say. Some integration has already been accomplished, but much more is to come. The aim is a set of ‘composable’ solutions that can be selected to match the evolving needs of each airline, OEM or MRO, rather than applications that fit neatly within a limited product category.
IFS’s goals include seamless integration and a single platform. For example, a mechanic for cargo operator, lessor and IFS customer Air Transport Services Group would be able to use Lidar on his personal device to measure and take a photo of an aircraft dent, explains IFS Lab Leader Bas de Vos. The device would instantly reserve a replacement part electronically in the company’s storehouse, where the reservation would be digitally displayed on the part’s bin. Simultaneously, the device would electronically send the dent’s picture and measurement to a repair shop to fix it, all with a few clicks.
Some new Maintenix features may appear stylistic, but IFS says they are extremely useful. IFS Solution Architect Jeremy Green notes Maintenix screens will be easily configurable by users without requiring developers, so each user can configure their own login ‘lobby’ screen to provide exactly the information they need to begin daily tasks. Current Maintenix customers “want to get their hands on” this feature, notes Senior Vice President Dan Dutton.
Some new capabilities have already been added, such as support of remote assistance and streamlined illustrated part catalogues. Others will come as Maintenix moves toward IFS Cloud, Dutton predicts.
Users will have access to supply chain tools, a long-range fleet planner that models scenarios to help planners, continuing airworthiness management capabilities, customer relationship management tools to support outside MRO, an electronic technical log and much more.
Dutton stresses that Maintenix users will be able to choose the pace and method of the transition to IFS Cloud and the functions they need.