Viewpoint: The MRO Technology Propelling Commercial Aviation Recovery
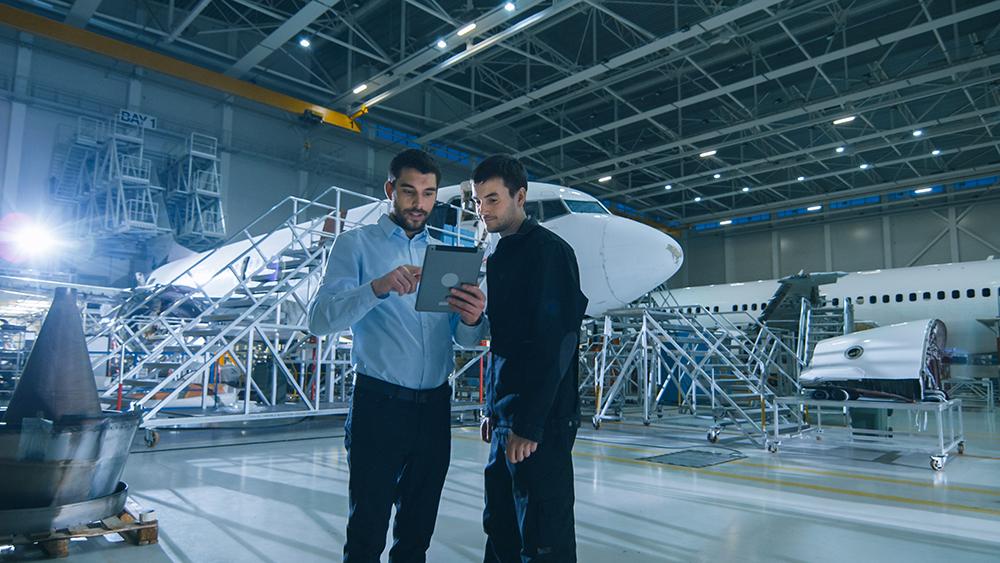
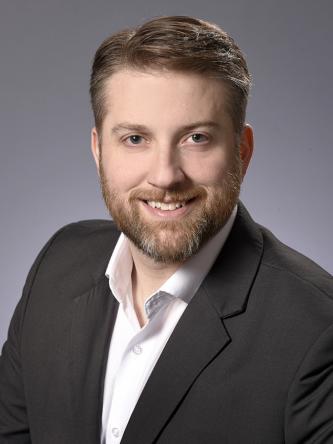
The aviation industry has faced massive economic challenges—from travel restrictions and quarantine rules to complete lockdowns, airlines and MROs are still playing catch-up from the near total shut-down of international travel in March 2020.
Airlines immediately sought to maximize their organizational efficiencies by doing more with less. This has ranged from keeping business operational with skeleton crews of staff to extending the life or increasing the availability of existing assets to the maximum possible extent.
Aircraft Stuck on the Ground
Work restrictions and social distancing requirements also forced businesses to work differently than they have in the past. Interestingly, in some cases these changes have demonstrated to previously change-averse organizations that rapid change is actually possible, and many leading organizations have seen the advantages that altering the way they work can bring.
Key examples of this include the FAA using remote collaboration on the evaluation of the 737 MAX or the arrival of ‘preighters’ as primarily passenger airlines convert their aircraft to carry additional freight, thereby unlocking new revenue streams.
Most airlines have had to make do with reduced workforces and significantly reduced fleets. According to Aviation Week Network Fleet and MRO Forecast data, more than 7,500 aircraft were in long term storage in May 2021 and more than 6,000 are still stored as of mid-September, with parked or parked/reserve status aircraft comprising 11% of the current in-service fleet. Managing so many parked and stored aircraft brings its own challenges, but the most strategic aviation organizations are actually seeing an opportunity.
Digital Projects Fill the Void
For many airlines that run to the tightest of margins, IT projects can be perceived as risks to continued operations. There’s no ability to free up the resources needed to execute projects and the potential disruptions to business have often meant much-needed IT investments are put off.
But now, those previously tight systems contain some unexpected slack. With lower load factors, fewer aircraft in service and, depending on levels of government support, staff potentially under less-than-typical pressure, there has been a somewhat surprising trend toward investment in digital transformation initiatives—even from the usually ultra-lean independent MRO sector. In fact, recent statistics from SITA show 31% of organizations expect an increase in IT spend in 2021, despite pandemic disruption.
But this increased spending doesn’t necessarily require large scale digital overhauls. IFS has found some airline and MRO organizations are looking for technology tools which tackle key recovery plans, such as unlocking predictive maintenance efficiencies, allowing remote collaboration and addressing safety issues.
Getting Ahead of the Recovery Curve
As vaccination rates increase globally and infection rates in many countries are declining, we are looking at a gradual re-emergence of commercial air travel. Many predictions have shown narrowbody fleets returning to 2019 levels in 2023, with widebodies following in 2024. However, faster than projected vaccine rollout in some regions and rebounds to domestic air travel happening more quickly in markets such as the U.S. means that there is a clear possibility of significantly beating those predictions. For the most forward-thinking airlines, it’s now a race to see who is going to emerge on top and, as such, many airlines are seeking new competitive advantages to leverage as they look to be first out of the gate.
At IFS we see airlines and MROs investing in certain operational focus areas to gain competitive advantage against an industry backdrop of recovery and economic pressures.
AI and IoT Accelerate Predictive Maintenance
One of the maturing industry technology applications is the use of Internet of Things (IoT) and Machine Learning (ML) for predictive maintenance. Maintenance software applications now allow for the aggregation of real-time sensor data, business and operations data, logs and more into a data lake infrastructure—with the ability to transform all this information into proactive maintenance tasks.
These data insights, along with ML models, can then be used to produce advanced statistics and KPIs to provide a holistic view of the asset or component in question, combining historical and forecasted values. Thanks to these digital developments, the often risk-averse aviation industry can pivot to using predictive maintenance models not only to increase performance and reduce costs, but also to better manage risk and enhance safety.
For example, as of 2020, Rolls-Royce is using AI forecasting supported by IFS to help airline customers automatically update predicted maintenance deadlines for every life-limited component inside their engines. This is a key part of the Rolls-Royce Blue Data Thread strategy, a digital information thread connecting every Rolls-Royce powered aircraft, every airline operation, every maintenance shop and every factory.
Remote Assistance Provides Guidance
The proliferation of smart devices and maintenance software applications now available on mobile have fast forwarded merged reality—where the real and virtual world are mixed and objects from both can interact. With remote working and social distancing becoming commonplace, remote assistance technology has been taken up by more airlines and MROs that see the benefits and adopt the solution.
Remote assistance lets team members work together over long distances, sharing information in a common view to diagnose and fix issues together. Remote assistance tools are also able to create an auditable archive of recordings that can later be searched through and reviewed, which is a valuable point for inspection, quality assurance, training and compliance activities.
Data-Driven Defect Management
Defect management is another key area ripe for innovation. Master Minimum Equipment Lists are often housed in paper or individual PDF documents and must be looked up manually. Information must be combed through to check if every individual fault can be deferred. Collaborative defect management offers fast, effective and supported decision making for technicians, which leads to improved efficiency and visibility, as well as real-time deferral compliance management.
It is up to the M&E systems to enable intelligent decision support for defect management by providing a single accessible framework for technicians to take faults raised and utilize a flexible, collaborative workflow to evaluate if the fault may be deferred. But the deferral doesn’t end when it is approved. To ensure compliance going forward, intelligent tools should also automatically generate and schedule follow-on tasks and recurring inspections until the defect is ultimately fixed.
The result of proactive and improved defect management is fewer grounded aircraft and reduced flight delays—and fewer delays means more profits for airlines.
The flightpath to a safe and efficient aviation industry recovery will require agility, flexibility and visibility for airlines and their MRO partners. Now is the time for organizations to prioritize their IT investment to unlock competitive advantages while ensuring they can maximize aircraft uptime and continue supporting a safe a return to passenger travel over the coming months. IT systems will play a key role in taking the industry from parked to soaring.
As Vice President, Aerospace and Defense Industries, Rob Mather is responsible for leading the charge on IFS’ global A&D industry marketing strategy, while also supporting product development, sales and partner ecosystem growth.