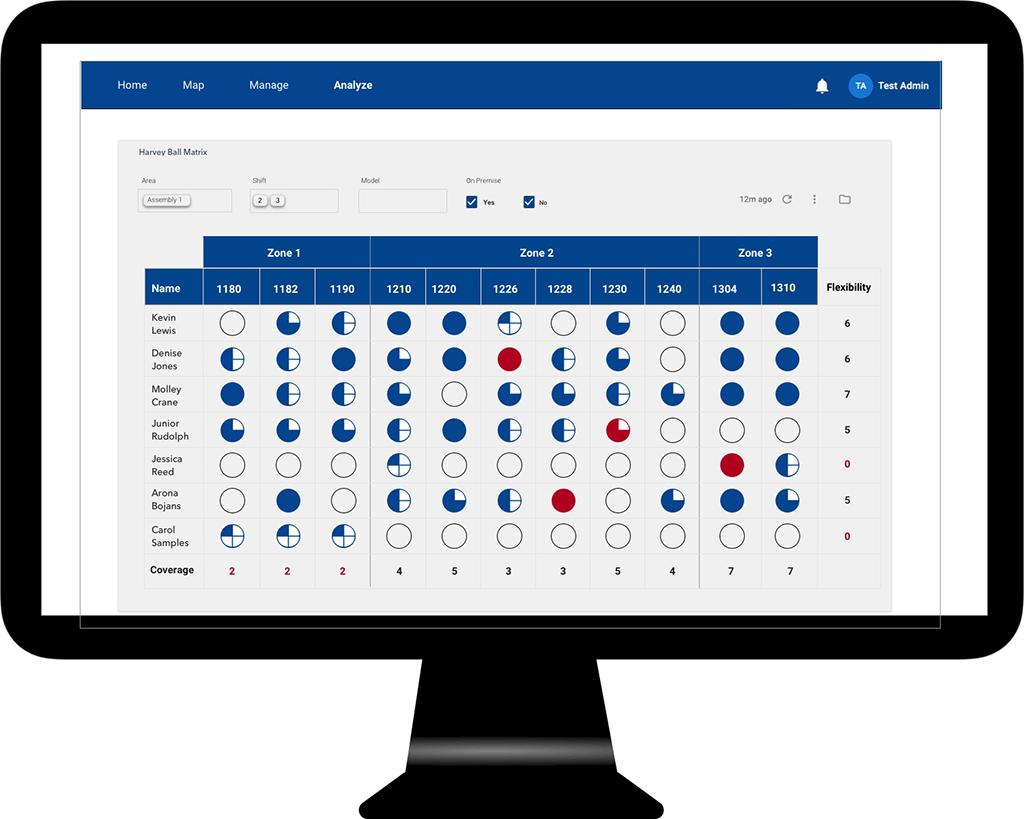
A Boston-based startup has launched a digital platform that is being used to help MROs and engine OEMs optimize technical training and labor scheduling. The platform aims to help aviation industry companies, which are feeling the labor crunch post-pandemic, do more with a smaller, more junior workforce.
According to Matt Delaney, head of enterprise solutions at Covalent, the platform was originally conceived as a research project at Harvard Business School to help industrial companies combat the skills gap.
“Even pre-COVID, the labor market was tight and the folks coming into these employers had a lower baseline competency than they have had in the past because people aren’t as mechanically inclined anymore—not to mention that the rate at which a lot of these companies were hiring has increased because of retiring Baby Boomers,” he says. “The takeaway was that at the shop level, either on the OEM side or the MRO side, these operations were taking on more responsibility for doing technical training in-house.”
During the platform’s development, Delaney says Covalent saw that many companies were using paper-based training and evaluation forms to track which employees knew how to perform various skills down to particular parts, processes and machines. “[The data] wasn’t real-time when supervisors rotated, moved or turned over so there was no continuity of data,” he explains, noting that even Fortune 1,000 manufacturers were “hitting that spreadsheet wall.”
Although many companies used corporate learning management systems such as Workday, SAP or Cornerstone to help digitally manage training processes, Delaney says these systems were designed for the indirect workforce (e.g. support and supervisory labor, such as administrative and management staff), so “there was a big gap as far as what was actually happening out on the floor and in the field for the direct workforce.”
This is further complicated at companies such as major engine OEMs, which have multiple divisions within different businesses, multiple job sites, and different workers at each site with various occupations and job pathways. “Each one of those occupations might need to know how to do 50 different things in order to buy off on a work order,” says Delaney. However, the ways in which these workers obtain and maintain each of those different skills can vary, such as requirements for completing various hours of work, written or practical examinations, supervisory sign-offs, certifications and renewals.
Delaney says Covalent helps companies map out the process through which workers obtain and maintain these skills. “We facilitate those little interactions between the trainees, the trainers, the evaluators, the auditors and the supervisors,” he says. “If you do that well, you’re capturing data along the way of how people are progressing against their learning pathway.” The data can also be linked to a company’s existing learning management system.
“Let’s say I’m a new technician and I need to know how to do 20 things,” explains Delaney. Covalent’s software could track skills completed in a corporate learning management system, proof of industry certifications, and in-house confirmations that an employee has learned how to use particular tools or run certain repair station procedures.
For new hires, Covalent can track larger learning pathways, such as how certain individuals are progressing against established productivity standards and areas where new hires are facing roadblocks. The data can also be used for optimized workforce planning, such as ensuring whether a company will have enough technicians to fulfill a new contract or determining which employees can backfill work when certain staff are out.
Delaney says the software has proven to increase companies’ “bench strength” by four times, helping them do more work with the same team or the same amount of work with a smaller team. He notes that Covalent’s software has reduced companies’ training time by 65% by automating up to 40% of the process.