How Next-Gen Aircraft Windows Have Become Safer And Stronger
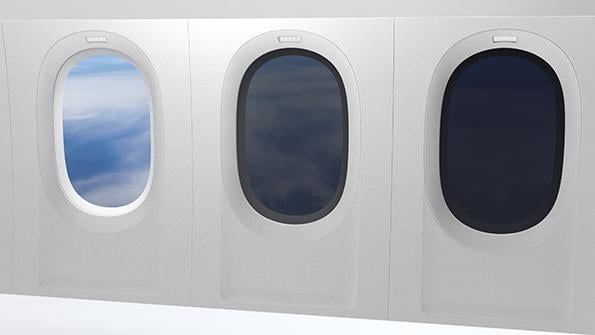
They are not the windows of a past generation of business and commercial jets: In the arcane world of aircraft windows, engineering trends are moving in new directions—such as shielding passengers and crews from harmful ultraviolet (UV) rays.
To that end, in June 2019 PPG announced its Solaron Blue Protection UV+ blocker technology, which “is the first technology to offer the broader protection in the harmful low end of the light spectrum,” says Brent Wright, PPG’s global business director for aerospace transparencies. “At the high end of the spectrum—say 800 nanometers—you have infrared light and thermal heat. At the other end—below 420 nanometers—you have UV and Hevblue [high-energy visible blue] light. These light rays appear to have links to skin cancer and macular degeneration.”
Solaron Blue Protection blocks 99% of the harmful ultraviolet A and B rays and more than 50% of Hevblue portions of the light spectrum, without degrading actual visibility for pilots, Wright says. “Existing aircraft transparencies [offer] a nominal amount of protection as a result of the chemistries that comprise their material construction,” he notes. “However, a typical glass cockpit window incorporating Solaron can exhibit an 83% improvement in Hevblue and a 27% improvement in UVA blockage.”
To accomplish this, PPG modified the chemistry of the materials used in the cross-section of its cockpit windows to incorporate Solaron—a PPG proprietary chemical compound—during the manufacturing process. “It is not a coating or similar component that is added later,” Wright points out.
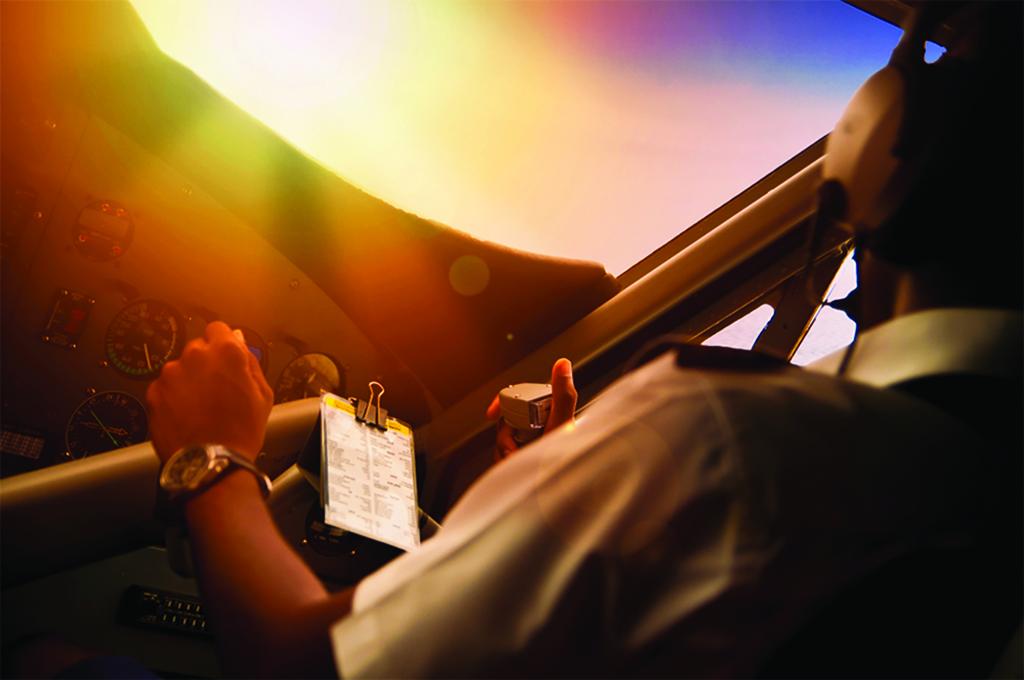
The Solaron transparencies, used for both cockpit and passenger cabin windows, are in the final stages of European Union Aviation Safety Agency certification, initially for a business jet application, and will be available as standard equipment for both line and retrofit. Wright could not name the specific business jet type or its manufacturer at this time.
Wright sees the business jet as a first step and is optimistic that Solaron will find its way onto commercial airline aircraft as well. “In fact, it was inquiries from commercial transport pilots that initially led PPG to pursue development of technology to mitigate potential UV/Hevblue issues,” he notes.
Solaron is available for any multi-ply PPG cockpit window, passenger window or fighter jet canopy. “PPG has performed extensive testing to assure the technology does not change the structural, performance or durability characteristics of the equipped windows,” he says. “Thus, certification for OEMs is a matter of a drawing change backed by a comparative material properties report supplied by PPG.” He stresses that because Solaron does not affect the structural or reliability characteristics of transparencies, PPG anticipates a straightforward certification.
Asked if the addition of Solaron could extend the service life for cockpit windows, Wright says it will have no effect on the failure mode or the design engineering considerations. More typically, an electrically heated windshield will fly for 5-10 years and ultimately fail due to a heater anomaly, often preceded by moisture ingress over time, in which water molecules migrate into the window cross-section and adversely affect the metal heater components.
“In theory, perhaps the protective properties of Solaron might enhance the life of a cockpit window, but we can’t claim that now,” Wright cautions. “Combined with PPG’s Opticor—an advanced transparency material—there may be an opportunity to enhance the service life of cabin windows versus conventional stretched acrylic,” he suggests.
Opticor is flying in some cabin window applications today. “Performance to date is promising, but the jury is still out on whether longevity can exceed the 10 years currently seen with some stretched acrylic windows,” Wright explains.
In another development at PPG, the OEM is pursuing a “smart” window system dubbed WinLogic. This technology incorporates a component that identifies and mitigates electrical anomalies in a windshield’s heating system to predict a possible failure. In tandem with that is a data-collection capability that can be linked to some big data analysis. That would help to determine future product improvements as well as enable greater reliability and logistical support for operators. “COVID-19 has slowed our ability to get that technology fielded, but we are close,” Wright adds.
Dimly Lit
With the introduction of the Boeing 787 in 2011, electronically dimmable windows (EDW) were born. When in their “closed” mode, all but a minuscule amount of outside light is blocked, and when “opened,” the windows offer a soft and gradual transition to ambient light.
The 787’s EDW cabin windows are the result of a partnership between PPG, which supplies its Alteos dimmable window assemblies, and Gentex, which provides the electrochromic technology. PPG is also the system integrator and supplies the assemblies to Boeing as well as post-sale customer support.
Gentex’s EDWs are “the first and still the only kind” flying on commercial airliners today, says Mike Behm, the company’s director of business development.
“Our latest technology, with near black-out darkness levels and fast switching speeds, is now offered on the Boeing 777X,” says Behm. “Speed improvements are one of the primary areas of focus and development for our products. People inherently expect instant on/off with things like dimming windows, so we’re constantly working to improve speeds.”
Behm says the 777X EDW will block more than 99.999% of visible light, while those on the 787 block 99.99%. “Although that may seem trivial, the difference becomes very apparent at altitude with full solar loading,” he remarks. “Also, the new EDWs can transition between full dark and full clear—or vice-versa—in approximately half the time as those on the 787s. We refer to the 777X system as ‘Gen3’ and the current one as ‘Gen2.’”
Behm reports that Gentex has also improved the switch design and function for the 777X EDWs, by moving from an elastomeric push-button to a glass-faced capacitive touch design. This offers a more intuitive function, along with significant improvements to durability, he says.
Behm adds that Gentex will be offering a similar dimmable windows package to Airbus in 2021 for application to an as-yet-unannounced aircraft. “The demand for ‘smart’ surfaces, including dimmable surfaces for privacy or shading, is constantly increasing,” he says. “We expect to see continued improvements to reliability and system design flexibility as material sciences continue to offer innovative new raw materials and substrates for constructing switchable and ‘smart’ surfaces.”
Bigger Is Better
Some of the main trends driving aircraft window design and engineering are intended to give pilots unobstructed views by enlarging the size of the cockpit windows and reducing the number and size of structural pillars. New materials are also playing a role, particularly with the use of high-mechanical-strength glasses and organic materials to reduce weight and thickness.
“With increasingly larger windshields, optimizing the mass, geometry and the electrical heating power is becoming a critical factor,” says Scott Huth, Saint-Gobain Mobility’s general manager for aerospace. “Along with that, the Saint-Gobain research and development team is focusing on optimizing the coupling between the airframe and the transparencies to reach a higher level of impact resistance to bird strikes and foreign objects. There is also an increased utilization of laminate designs that balance the structural requirements, visibility, exterior impact resistance and aircraft weight.”
Citing one example, Huth points to Saint-Gobain’s patented, multiflow product line technology coupled with ultra-thin coating. “Saint-Gobain is a world leader in vacuum-deposited thin layers such as metal, oxide and transparent conductive coating,” Huth says. “The combination of these layers with laser treatments and scribing allows us to finely adjust the heating power to needs of anti-icing over the whole surface of the windshield, keeping the energy consumption lower.”
The OEM is also using high-mechanical-strength glass products and organic materials to reduce weight and thickness. High-mechanical-strength glass has historically been thermally tempered glass. Today, Saint-Gobain provides more generally chemically tempered glass, specifically designed for aerospace applications, allowing higher mechanical resistance and optimized weight, says Huth. To do that, it utilizes polymethyl methacrylate, a stretched organic material. Examples include Saint-Gobain’s Solidion and Ionalex mineral glasses, produced in-house.