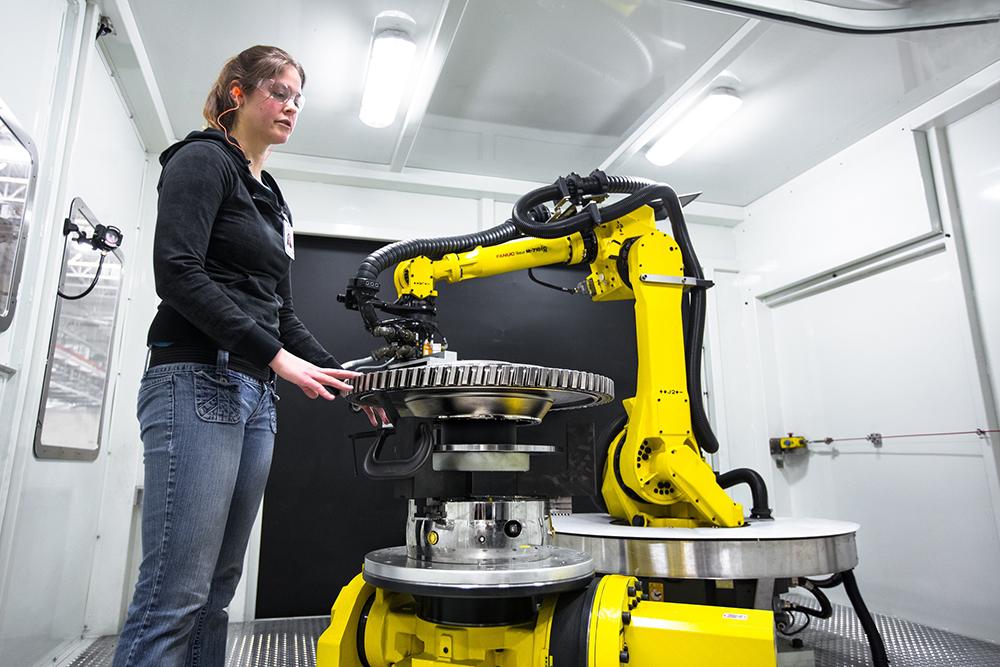
Engine OEMs have been developing robotics use cases in MRO for some time now to make maintenance processes more efficient, but new innovations could now provide benefits that go even further. According to GE Aviation, the use of robotics and automation could help the MRO industry tackle sustainability and labor shortage challenges.
The engine OEM acquired UK-based OC Robotics in 2017, and since then it has been working to develop and adapt its snake-arm robotic technologies for use cases in engine MRO. The robots provide better access to difficult-to-reach areas of the engine, and GE is leveraging this to focus on three key areas: cleaning, inspection and repair.
While manually operated inspection technologies such as borescopes can be used to look inside these tight spaces, they have their limitations. According to Adam Mallion, commercial and operations leader at OC Robotics, “what they lack is the ability to steer and navigate inside some of these spaces.” He adds that robots also provide the ability to “get back into the same place again and be able to see the same areas time and again from the same angles and the same viewpoints.”

Inspection is only one piece of the puzzle. These tight areas also need to be reached for cleaning and maintenance, which can often require taking engines off wing. GE and OC Robotics are developing technologies to carry out some of these tasks on wing, such as reapplying thermal barrier coatings.
According to Mallion, wear and tear on these coatings can be particularly challenging for operators that fly engines in regions with hot, harsh weather. “On the GEnx fleet we have deflectors in the combustor that get affected by dust buildup and ingress when working in these [regions],” he says. “Over time, that buildup means those parts need to potentially come off wing earlier.”
Mallion says GE’s teams have designed small robotic arms that can enter the igniter ports on the combustor to reapply these coatings in the field using “a clever robotic system that can mount to the outside of the engine.” The technology can be used on wing or in an MRO shop, which GE says can increase engine durability and reduce maintenance burden.

GE is also using automated technology to simplify engine cleaning through its 360 Foam Wash system, which it launched last year in partnership with Etihad Airways. It has been capturing data from the wash system and from its engines, which it says shows that 360 Foam Wash is providing significant improvements in exhaust gas temperature performance. GE says this results in both reduced maintenance burden for the customer as well as more sustainable engine performance. It also reduces sustainability impacts in the supply chain, since engines need to be transported to repair facilities less frequently.
To further sustainability efforts, GE has also begun efforts to localize repair technologies through new automated, robotic approaches. According to Nicole Tibbetts, chief manufacturing engineer for repair, GE Aviation has invested in automated welding technology that it is starting to roll out across its repair network.
“One of the big investments we’ve made as an MRO network over the last year is we’ve procured six new cold metal transfer machines,” says Tibbetts. “Cold metal transfer is really the next generation of welding technology, where it allows us to have a laser vision system and a modified MIG [metal inert gas] welding application that puts less heat into the part. It’s four times faster than manual welding and it has some additional capability for repair yield.”
Tibbetts notes that the automated capability provides significant sustainability benefits. “Because it is a much more efficient welding process, we’re able to transition many of our conventional weld repairs out of centralized centers of excellence and the repair network, and into the overhaul network—which means the repair work is being done where the engine is being overhaled,” she says. “You reduce all that waste in terms of transportation of the part going 3,000 or 5,000 miles in each direction to be repaired and returned to the engine.”
GE has already installed its first of these system in Cardiff, Wales and plans to subsequently add more at its facilities in Brazil, Caledonia, Scotland, Hungary and Singapore.
Tibbetts says GE is also investing in other automation and robotics technologies that have helped it transition repair work to where engines are being serviced. One such investment is an automated and artificial intelligence (AI) enabled fluorescent penetrant inspection (FPI) system in Singapore. According to Tibbetts, 90% of its CFM56 airfoil inspections at the site are now being done by an AI-powered robotic system, which is “a unique opportunity to take the subjectivity out of the inspection.”
Another area in which Tibbetts believes automation can help is by reducing the workforce and training burden. “The post-COVID workforce has fundamentally changed how the aviation industry needs to operate,” she says.
For instance, certified inspection techniques such as FPI can require hundreds of hours of on-the-job training. “When you can impart something like AI that has all the intrinsic machine learning and has seen hundreds of thousands, if not millions, of blades before, you have a technical standard that you can achieve in real time without having to undertake 400 hr. of training humans,” says Tibbetts. “It really is affording us the ability to work in new ways, especially around automated and AI enabled inspections.”