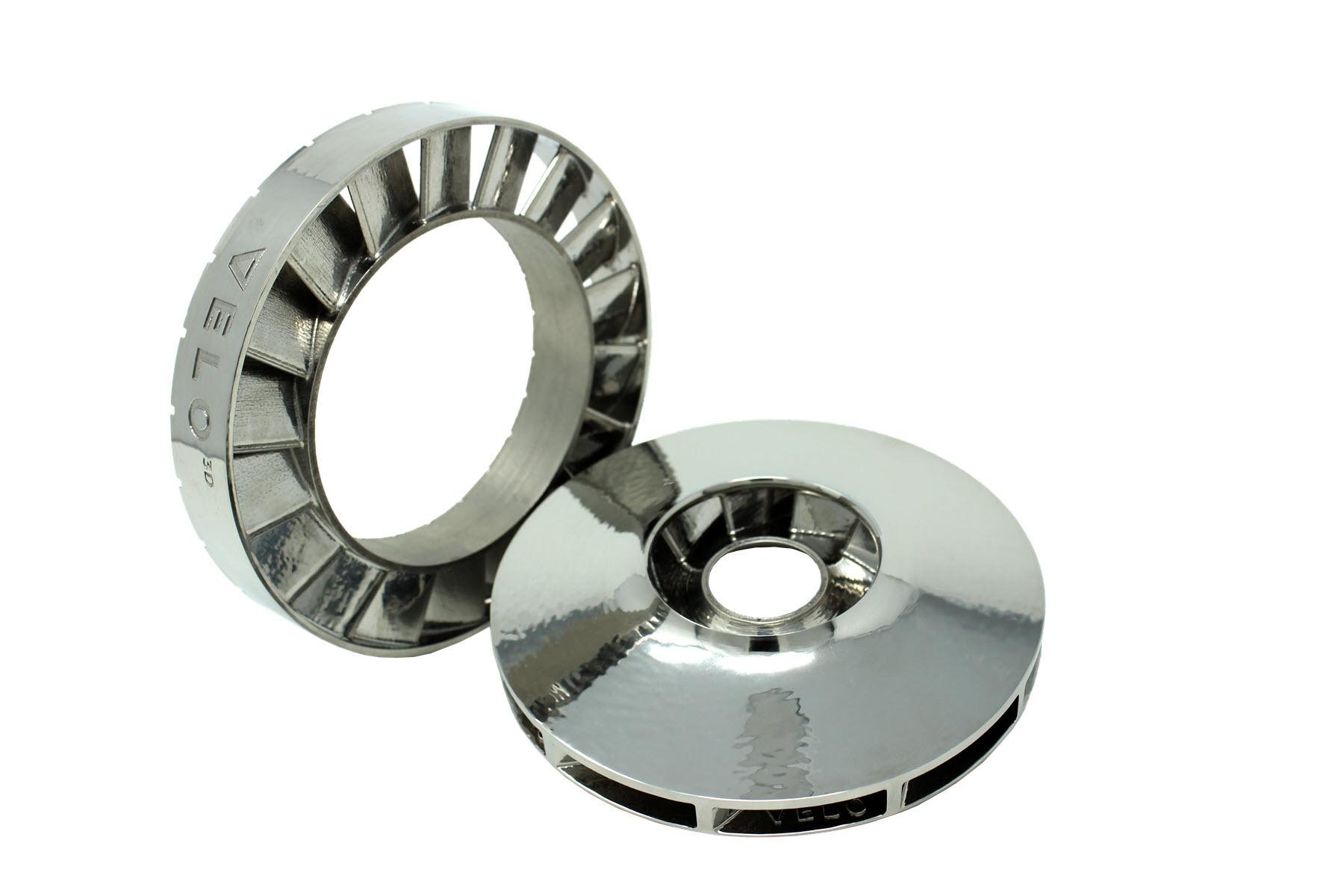
Chromalloy is installing a new additive manufacturing machine, its first in “the metal world,” to reduce MRO costs for and extend the life of the aviation and energy engines it supports.
The Velo3D Sapphire machine can print nickel-based superalloys, including Hastelloy X that is known for its strength in high-temperature environments.
Jim Whitton, Chromalloy’s director of innovation strategy, says the Velo3D machine can print parts up to one cubic foot and provides two primary benefits.
The first is that “The very low angle build capacity negates a lot of support material requirements" and the “downstream processing to remove things that were added in the build unnecessarily which don’t contribute to the net form of the part. This is just wasted energy,” says Whitton. Post production also adds cost and time, which can be eliminated by printing parts with complex geometries.
Secondly, he says Velo3D’s mindset focuses on data and processes, which is evident in its machines. “At the end of the day, in our business, technical data rules,” Whitton says. Chromalloy is a very process-driven company and “we need that technical data to back up the processes and the quality controls,” he says.
While the company won’t disclose which parts it will print with this new capability, Whitton say it will be good for hard to find and costly parts needed in low volumes.
“We’ve been developing a few components and have realized the results that we intended,” says Whitton, who manages the company’s technology road map.