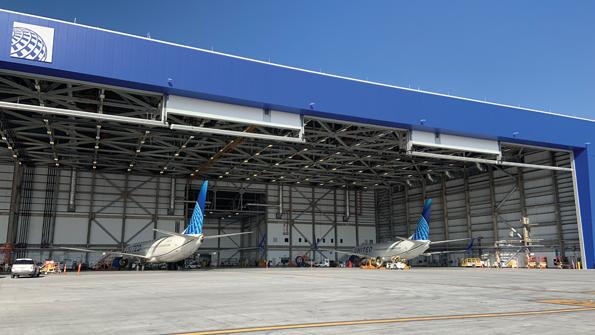
United Airlines recently opened a new $352 million technical operations center at Los Angeles International Airport (LAX) that is bringing significant efficiencies to its operation. On top of that, it should receive the U.S. Green Building Council’s Leadership in Energy and Environmental Design Silver certification in the next few months.
Although United and Continental Airlines completed their merger in 2010, the tech ops vestiges of the two at LAX really did not merge until this new facility opened on Nov. 11, 2021.
The former East and West facilities were more than 1 mi. apart, so after the merger, moving parts and people between them was very inefficient.
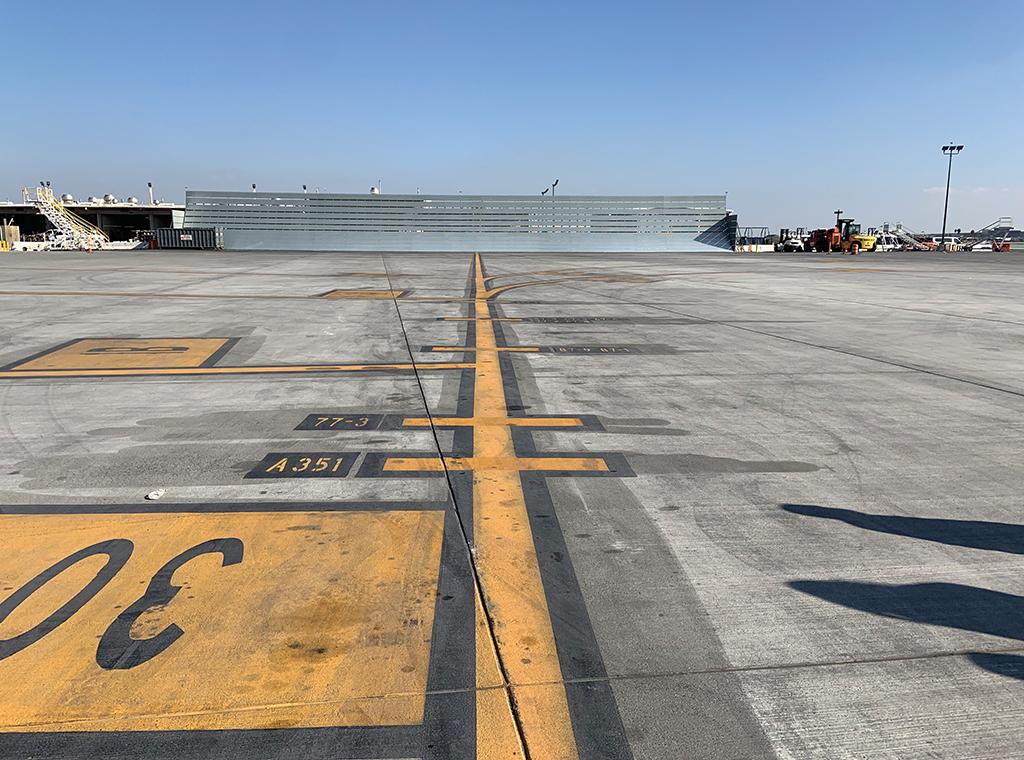
Most of the parts were stored in the West facility, so “if an aircraft parked here at the East needed a part, and you got into a high bank departure time for the international flights going out on the red-eye flights, [driving there] was like getting on the freeway,” says Fabio Maietta, United’s managing director of LAX technical operations. “I mean, you would go a little bit and stop, and go a little bit and stop, and go a little bit and stop” because aircraft movements always had the right of way.
The West facility, formerly Continental’s, included an L-shaped hangar that could house two widebodies and four narrowbodies. It was built in the 1960s, when the airline was flying DC-6s—so in actuality, the hangar could only fit one of today’s widebodies, such as a Boeing 787 or 777, that have much larger wingspans. It also was just getting old—an alarm system would go off almost weekly or the hangar door or overhead crane would malfunction. The East facility, formerly occupied by United, was small and used to be part of an old airport terminal. All aircraft maintenance was performed outside.
Time For an upgrade
The LAX airport authority started updating its master plan in 2015-16, partly to move airline operations closer to the terminals from which they operate. For United, its East area was closer to its operations at Terminals 7 and 8.
But the East facility would not accommodate a combined operation. United needed a new tech ops space. It also needed a good remain-overnight (RON) line facility that could handle its daily operations and make sure the aircraft were prepared for the next day, says Maietta.
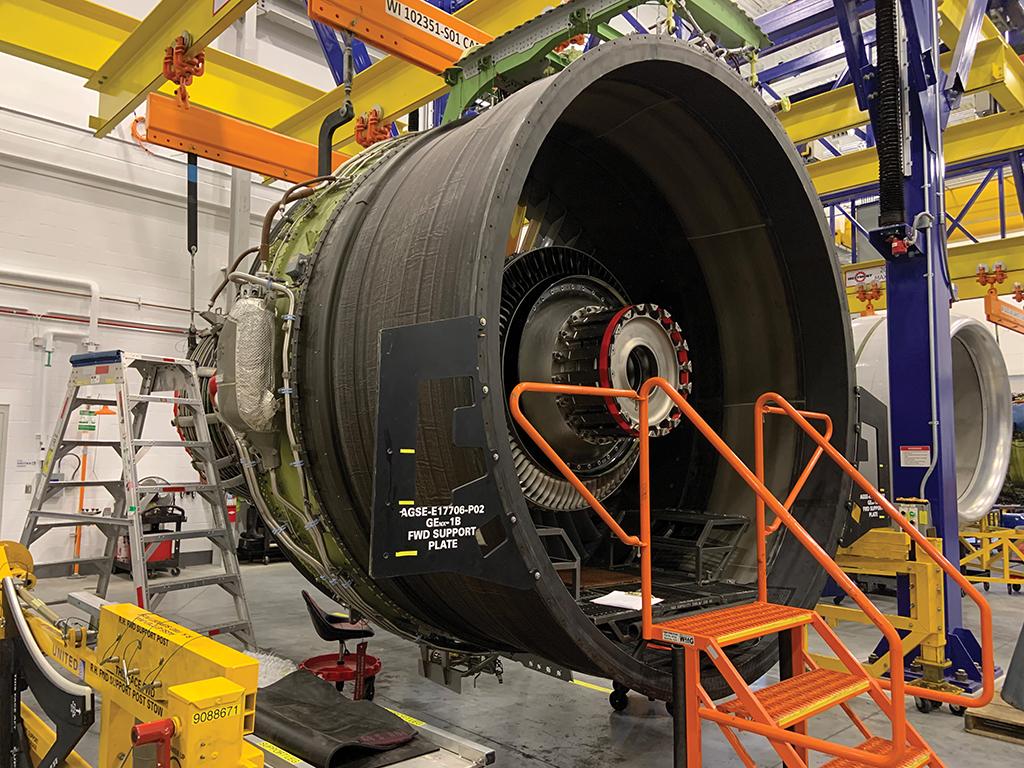
Designing the new tech ops facility, which is about 407,000 ft.2, or roughly the size of three American football fields, was an iterative process. There was a lot of back and forth between the FSB architects and the LAX tech ops staff about the flow of the operation and safety of the staff. The initial facility also had to shrink in size because “the FAA tower would not have had a clear view of the end of the runway, so we had to reorient the location of the hangar and lower the roof line to make it slightly smaller,” Maietta says.
Before demolishing the East building so construction could start in 2019, United had to figure out how to continue tech ops activities without disrupting day-to-day operations. That included not disturbing the movements in and out of its neighboring cargo facility, which became even busier during the pandemic.
Provisioning functions, from cleaning supplies to blankets, moved permanently from the East facility to United’s adjacent cargo facility.
“All of the [ground support equipment (GSE)] functions have been moved over [from the East] to the West facility in the interim,” says Armando Hernandez, United’s senior project manager of Western region corporate real estate planning. “We actually occupied one low-bay hangar bay on the West that we repurposed into a GSE facility. So one aircraft bay turned into multiple GSE bays.” United also moved a Quonset hut on the East side to support maintenance, and “any of the heavier workload was relocated to the West hangar where we could bring the aircraft inside and utilize the overhead cranes,” Maietta notes.
Before construction started, tech ops worked with United’s network operations center in Chicago to “let them know during the construction process to keep our flight activity at a level where it was manageable,” Maietta says.
“Let’s say we had 120 flights a day with 30 aircraft overnight,” he continues. “We may have downsized that during the construction process to 24 RON aircraft so we could concentrate on those 24 as opposed to 30 aircraft overnight.” Early in the pandemic, when flight activity decreased, that number declined as well. However, Maietta notes: “Aircraft that were stored long-term actually required a lot of man-hours of work to put them not only into storage, but to de-store them when the time came. We had to add a lot of man-hours.” At the peak of the crisis, United parked 23 aircraft at LAX, but on average it had 18, says Reza Asadifar, senior manager of United LAX technical operations. The one widebody parked was not there for long, because it was put into cargo service.
New Tech Ops
With the opening of the new complex, United’s LAX tech ops team is finally all working in one place.
The new hangar comprises two bays—each of which can support one widebody (Boeing 777 or 787) or three narrowbodies—for a total capacity of six narrowbodies or two wide-bodies or a combination thereof. While the number of aircraft spots in the hangar is the same as in the old West building, that is about all the two have in common.
The brand-new facility is organized for each task and includes more amenities for the staff. To meet the Leadership in Energy and Environmental Design Silver requirements, the complex includes features such as LED lighting, ceiling fans, provisions for electric GSE and facility monitoring systems.
The complex also houses a parts warehouse, 15-bay GSE shop, engine buildup shop, training facility for recurrent training, tooling shop, tool calibration and tool repair room, welding shop, and offices and conference rooms.
United has ramp space to park another 22 aircraft as well. On a typical night, that usually includes five or six widebodies plus some narrowbodies. That is about 45 fewer parking spots than what it had before, including both the East and West LAX facilities, Asadifar says.
United’s LAX technical operations center (TOC) is one of the airline’s primary 787-9 and -10 line stations, although it also can perform maintenance checks on the 737, 757, 767, 777 and occasionally Airbus aircraft. Overnight maintenance is mostly widebody and averages about 650 work-hours per night but that can ramp up to 800 or a little higher sometimes, says Maietta. He expects the RON work to increase for the 2022 summer flying schedule. (United’s Houston, Newark, Chicago and San Francisco facilities also have 787 capabilities.)
But LAX does most of the 787 engine changes for the system. “Our guys are just experts at it, and the 787 [GEnx-1B] motor has some fuel nozzle issues, so we’re also primarily taking care of those as well,” Maietta says. “Our inspection team has the latest and greatest experience, with GE’s assistance, in knowing what to look for.” The LAX tech ops team either changes the fuel nozzles or swaps the engine, depending on how many nozzles are affected.
A break room big enough to host the daily safety briefings at the start of each shift—instead of giving the briefing in four rooms—has helped get everyone on the same page. “There’s nothing lost in translation going from room to room,” Maietta says. Having everyone in one room has also been good for team-building and morale.
One of the big efficiencies is the ease of moving parts and people to the aircraft. “Before, about 95% of parts were in the West hangar, so if you’re doing an RON at the East facility, it could take up to 2 hr., worst-case scenario, so you lose efficiency. And if the new part doesn’t fix the problem, you’ve lost 2 hr. of troubleshooting,” Maietta explains.
Also, moving parts from the West facility to the terminal at peak hours took 20-30 min., which was a stressor during tight turnaround times.
Because of the improved proximity between the tech ops center and Terminals 7 and 8, “moving aircraft from the terminal to here now is a matter of minutes,” Asadifar says.