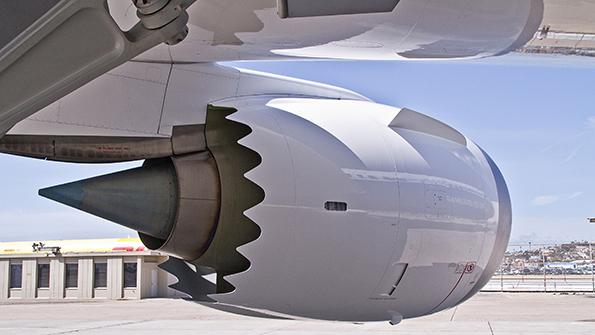
Like most modern commercial jets, the Boeing 787 uses a cascade-type thrust reverser.
Credit: Collins Aerospace
As sustainability goals push more systems toward electromechanical actuation solutions, weight savings and maintenance-efficient designs, thrust reversers are unsurprisingly trending in the same direction. “We expect aircraft entering service during the next cycle to be more electric, with the...
Thrust Reversers Go More Electric, Lighter Weight is part of our Aviation Week & Space Technology - Inside MRO and AWIN subscriptions.
Subscribe now to read this content, plus receive full coverage of what's next in technology from the experts trusted by the commercial aircraft MRO community.
Already a subscriber to AWST or an AWIN customer? Log in with your existing email and password.