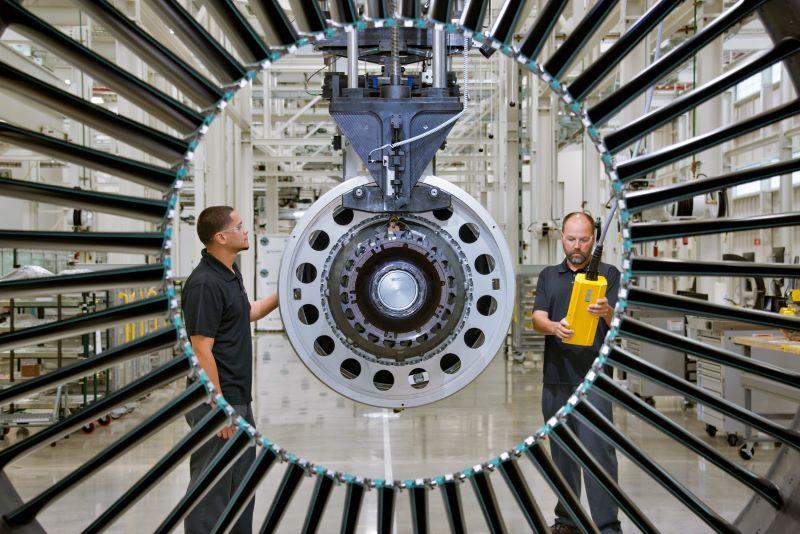
Credit: Pratt & Whitney
Pratt & Whitney is confident that its assumptions around PW1000G geared turbofan (GTF) production and expedited parts inspections for the in-service fleet remain accurate, putting the company on pace to meet demand for new aircraft and improve turnaround times on engines undergoing mandatory service...
Subscription Required
Pratt & Whitney: Parts-Production Ramp Easing GTF Pressure is published in Aviation Daily, an Aviation Week Intelligence Network (AWIN) Market Briefing and is included with your AWIN membership.
Already a member of AWIN or subscribe to Aviation Daily through your company? Login with your existing email and password
Not a member? Learn how to access the market intelligence and data you need to stay abreast of what's happening in the air transport community.