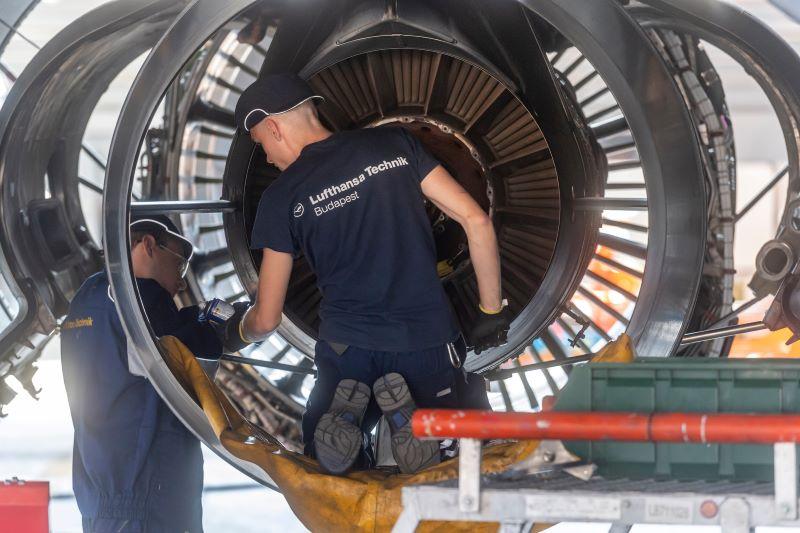
Credit: Lufthansa Technik
MIAMI—Engine manufacturers are leaning heavily on their approved overhaul shop networks shops to help meet unexpected demand on current generation engines, but restrictions on repairs and other licenses continue to create headwinds. “There used to be no issues on sharing information,” Delta TechOps...
Subscription Required
This content requires a subscription to one of the Aviation Week Intelligence Network (AWIN) bundles.
Schedule a demo today to find out how you can access this content and similar content related to your area of the global aviation industry.
Already an AWIN subscriber? Login
Did you know? Aviation Week has won top honors multiple times in the Jesse H. Neal National Business Journalism Awards, the business-to-business media equivalent of the Pulitzer Prizes.