Additive Moves Into Interior Structures, Dynamic Metal Parts Are Next
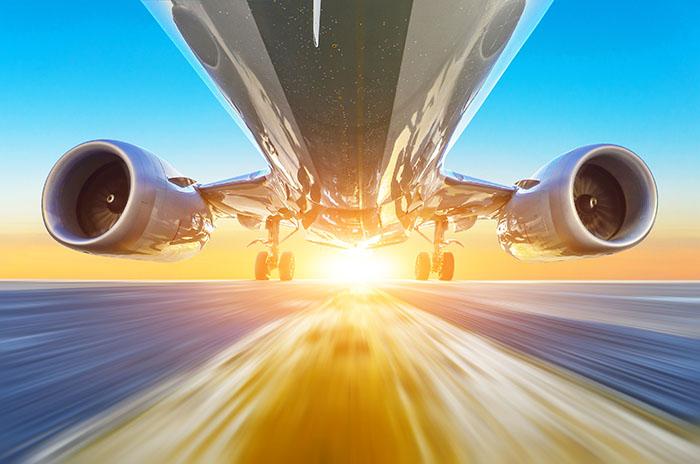
Additive manufacturing is quickly moving from the traditional polymers for seats and seat accessories to much more serious parts, both polymer and metal, of aircraft interiors, structures and major components. Collins Aerospace has set very ambitious goals for its own participation in the additive revolution.
On the horizon, one of the most advantageous applications of additively manufactured polymer parts will be interior structural parts that could replace metal or composite parts, predicts Paula Hay, vice president for advanced manufacturing engineering and technology at Collins.
“For example, interior structures with challenging geometries that today are manufactured with metal or composites could be lightened and produced more efficiently with polymers,” Hay notes.
The Collins exec also expects additively manufactured polymers to offer benefits over metal parts for fluid management systems.
Additive metal production is tougher because it usually involved flight-critical parts and requires rigorous certification processes.
Nevertheless, Hay says, “The aerospace industry is well on its way to flight-certifying many additively produced metal parts such as brackets, heat exchangers, and so forth.” She says the next challenge for additive metal production will be certifying parts that are dynamic or rotating.
And here it may be necessary to alter the nature of qualification processes. “Because the engineering requirements for dynamic parts are significantly more difficult and challenging, it will be crucial for industry to close the gap regarding use of model-based, or computational materials, processing for qualification.”
Longer term, additive manufacturing is going to disrupt aerospace supply chains in more ways than it has done currently.
Hay believes is it will even be feasible, at some point in the distant future, that all parts will be printed at the point of use. Supply chains could then consolidate at the location where aircraft undergo final assembly, and necessary parts could be produced on-demand.
When and if that happens, or happens even to a major extent, the impact of reductions in inventory and production time, coupled with the shift away from current production methods, will be too many is to accurately calculate today.
“Like many other technical revolutions, the ecosystem will undergo gradual changes that will evolve over time but, when compared over a span of decades, the differences will be quite significant.”
How realistic is 3D-printing at least all the metal and polymer parts of an entire airplane? A company named Relativity is already printing entire satellite-launch rockets, both engines and bodies. Rockets are or course simpler than passenger airplanes.
More important, perhaps, Relativity’s Terran 1 rocket will carry no humans, so safety standards need not be as high. But as experience is gained and certification methods improve, additive manufacturing of much of a commercial aircraft should become quite feasible.