Rolls, Pratt Pushing Hard On Additive Manufacturing For Future | ロールスロイスとプラット&ホイットニー、3Dプリント技術を強力に推進
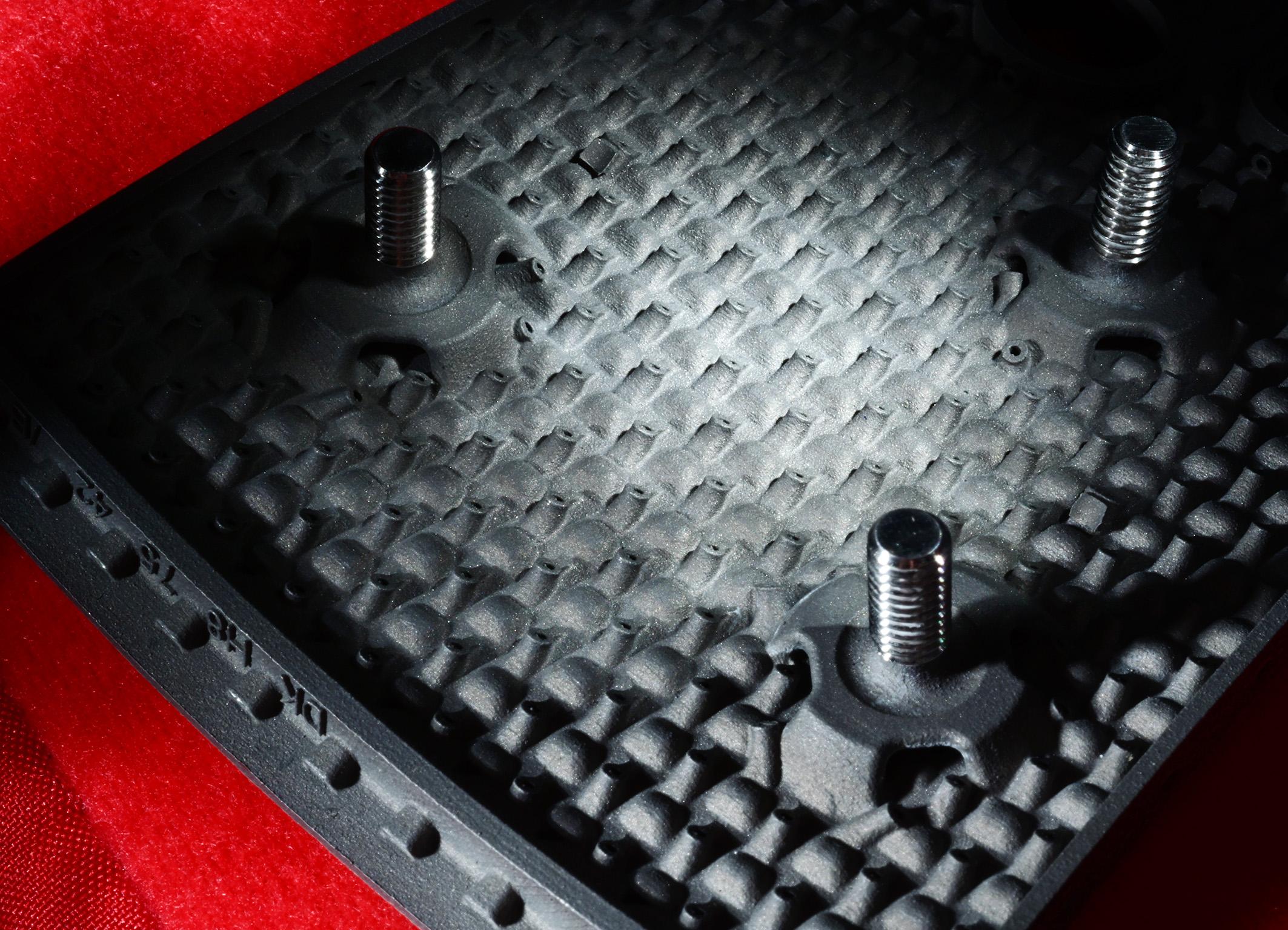
GE社が民間航空業界における積層造形技術(3Dプリント技術のひとつ)の普及を目指しているが、他のエンジンメーカーもこの新技術の新型エンジンへの応用を試みている。
ロールスロイス社では新型のビジネスジェット機向けエンジンで積層造形技術に取り組んでおり、将来的にはその知見をUltrafanや電動システムに応用することを検討している。プラット&ホイットニー社もまた、取り組みを始めたばかりではあるが、野心的な計画を持っている。
そして、本当に重要なのは将来の計画だ。完全新設計のエンジンが開発される時、積層造形技術を前提とした部品が本格的に普及する機会が訪れるだろう。大きな環境の変化にさらされている航空業界が向かっているのは、まさにそのような方向かもしれない。
ではなぜ、これほどまでに積層造形技術が注目を集めているのか?ロールスロイス社にとっては、その利点は明確だ。同社のイノベーションハブでディレクターを務め、8年間にわたり積層造形技術を用いた新規パーツ製作や修理を手がけてきたNeil Mantle氏は「他の方法では作れないような、新しい形状の部品を設計することができるからだ」と語る。
2015年には、ロールスロイス社は積層造形技術を用いて、1.5m級チタン製フロントベアリングハウジングをTrent XWB-97デモンストレーター向けに製造した。これは積層造形技術を用いて作られた部品としては民間航空史上最大のものだ。Mantle氏は「我々はそこから大きく前進した」と話す。
同社はイギリス・ロザラムに積層造形専用の施設を建設し、ダッソー・ファルコンに搭載される新エンジン・Pearl 10X用の燃焼器タイルなどを製造している。
燃焼器タイルは複数の穴が開いた複雑な形状をしており、積層造形技術なしに製造することは不可能だ。鋳造とレーザー加工の組み合わせでは、タイルの冷却性能が大きく低下してしまうだろう。
Pearl 10Xプログラムのシニアバイスプレジデントを務めるPhillip Zeller氏は、積層造形されたタイルは冷却用の気流を最適化し、冷却に用いられる空気が減ることで、より多くの空気を燃焼器に送り込むことができると説明する。
また、3Dプリントされたこのタイルはエンジンのホットスポットから生じる窒素酸化物を抑制し、燃焼器出口の制御を改善、これによりブレードやベーンが保護され、タービンの寿命向上につながる。Zellar氏によると、積層造形が実現した複雑な造形により、全体的なエンジンの冷却性能は20%向上したという。
XWBエンジン開発時に電子ビーム溶解から始まったロールスロイス社の積層造形技術はさらに熟成され、Pearlエンジンではレーザー粉末床融合(Laser Powder Bed Fusion)技術も用いられている。現在ロザラム工場で使用されている3Dプリント設備には生産性向上のために各4基のレーザーが搭載され、4セットのタイルを同時に加工することができる。そして、積層造形技術のもうひとつの利点はプログラム推進にあるとZeller氏は話す。
プロトタイプ機の試験により設計変更が必要になった際、次のプロトタイプに変更を反映するまでに必要な時間が、従来の製造プロセスと比較して実に75%も削減されるという。
積層造形技術がもたらす高度な造形能力と効率性は、ロールスロイス社が新たなマーケットに参入する上で不可欠なものになる。Mantle氏は「電力密度・重量・冷却性能などが重要な電動航空機において極めて重要だ」と強調する。同社では、航空エンジンに限らず、その他のエンジンについても積層造形技術の使用を広げている。
同社は6年間にわたりEASAやFAAと積層造形技術の認証に協力しており、今では一通りのプロセスを理解している。Mantle氏は「積層造形技術の認証は、ガスタービンの複雑な製造方法と比較すれば特別難しいものではない」としつつも、「設計・材料・製造法の理解が必要だ」と話す。
そして、これこそが修理部品を3Dプリントにより供給しようとする他社の参入障壁になる。なぜなら、前述の3つの要素に関するデータが不可欠だからだ。Mantle氏は、8年前には3Dプリンタを用いてエンジン部品を製造するサードパーティが数多く現れることを心配する声もあったと回想する。
今では、規制当局・部品メーカーともに3Dプリント部品の安全性を担保するためには厳しい認証要件を満たす必要があることを理解している。
いずれにせよ、ロールスロイス社は習得した積層造形技術をUltrafanや将来の民間機向けジェットエンジンに応用していく考えだ。
プラット&ホイットニー社は、GE・ロールスロイス両社に追い付くべく対応を進めている。積層造形技術担当フェローを務めるJesse Boyer氏によると、同社はレイセオンテクノロジーズ社が主導する「Industry 4.0」戦略に沿って、事業の近代化および変革に取り組んでいるという。「積層造形技術はこの戦略の重要な要素であり、パフォーマンスの向上、リードタイム短縮、効率化の実現につながる」と彼は話す。
実際に同社は新型コロナ対応にあたる医療従事者向けに3万個のプラスチック製フェイスシールドを3Dプリントで製造し、「短い準備期間で、当初想像していたよりもはるかに多く製造することができた」と同氏は振り返った。
彼は、2020年にプラット&ホイットニー社がレイセオン社と合併したことでシナジーが生まれ、レイセオンテクノロジーズ社のリサーチセンター内に設けられた「積層造形プロセス開発センター(Additive Manufacturing Process Capability Center)の活用なども可能になったと話す。
同社の小さなチームでは、小型ターボジェットエンジンの燃焼機といった、ホットセクション内の単一部品の試作品製造などに積層造形技術を活用している。「積層造形により、従来は12〜24ヶ月かかっていた初期コンセプトの開発からテストまでの期間が6〜8ヶ月に短縮された」と彼は述べた。
将来的には、同社は次世代型の熱交換器、アコースティックパネル、ベアリングサポート、アクチュエーター部品、燃焼機部品などに積層造形技術を活用していく考えだ。また、修理作業や生産用治具への応用にも注力している。積層造形の手法としては、粉末床融合、指向性エネルギー堆積法、バインダージェッティングなどを検討している。
「我々は、より安定したプロセス制御および効率をもたらす粉末床融合方式の開発を進めていく」とBoyer氏は話す。ただし、その一方で修理や持続可能性にも注力するという方針は、同社として指向性エナジー堆積法やバインダージェッティングも検討対象に含めることを意味している。
プラット&ホイットニー社のエンジンには、耐熱温度や疲労/引張強度の性能が低くても問題が少ない非金属材料の部品はあまり用いられていない。とはいえ、同社としては積層造形が可能な新たな複合材の出現に備えている。
Boyer氏は、同社における積層造形技術の活用法を4つのケースに分けて考えている。第1は既存部品の製造や代替だ。これは、既存品を鋳造や鍛造といった従来型の手法で製造するよりも、コストやリードタイムを小さくできる場合に積層造形を用いるという考え方だ。この場合は設計や材料に大きな変更は必要ない。
第2は、アフターマーケットにおける活用だ。これは交換部品や修理における活用で、設計変更なしにリードタイムを削減することができる。
第3は、複数の従来型部品を単一の積層造形部品にまとめる使い方だ。大きな設計変更、そして素材の変更も必要になる可能性があるが、材料・リードタイム・コストの削減と効率化につながるだろう。
第4は、GE・ロールスロイス両社が取り組んでいるような、完全新設計のエンジンを開発する上で、積層造形を前提とした効率的な部品設計を行う活用法だ。
MRO Prospectorで契約情報を検索し、受注機会を発見しましょう
MRO Prospectorは民間機MRO(メンテナンス・修理・オーバーホール)契約の特定、予想される個別MRO案件の確認、将来の航空機およびエンジンのフリート規模を把握するのに役立つオンラインツールです。この製品は、航空会社やMRO事業者とのビジネスチャンスを追求するために、MROマーケットにどのような機会があるのかを知りたい方に向けて作られています。
GE has looked to edge forward its additive manufacturing capabilities in the commercial aviation industry. But other engine OEMs are moving to exploit the new techniques for their new engines.
Among these is Rolls-Royce, which is working on additive manufacturing for a new business-jet engine and will look to apply its expanded additive experience to the Ultrafan or to novel electric powerplants further in the future. Pratt & Whitney is much earlier in its additive journey, but has ambitious plans.
And it is future plans that really count. For the opportunities to design new additive parts expand dramatically when clean-sheet engine concepts are considered. That may be where aviation is headed under climate pressures.
Why all the interest in additive? For Rolls, the main advantage is clear. “It creates novel geometries, and we can design parts that we could not make by other means," says Neil Mantle, director of manufacturing at Rolls’s innovation hub who led the company's additive efforts for eight years as it developed both additive repairs and new part-printing capabilities.
In 2015, Rolls used the new technique to make the largest additive structure in civil aviation, a 1.5-meter titanium front bearing housing for a demonstrator of the Trent XWB-97. “We have moved on considerably since then,” he says.
Rolls has now built a dedicated additive manufacturing facility in Rotherham, which will print combustor tiles and other parts for its new Pearl 10X engine that will power Dassault Falcons.
The combustor tiles are complexly shaped structures with multiple perforations that could not have been made without additive manufacturing. The alternative, casting plus laser drilling, would have made tiles with much less cooling ability.
Phillip Zeller, SVP of the Pearl 10X program, explains the additive tiles optimize cooling flows, thus using less air for cooling the engine and enabling more air to flow through to the combustor.
The printed tiles also control nitrogen oxide, which can come from engines hot spots, enable better control of the combustor’s outlet, protect blades and vanes and improve the turbine’s life. Overall, Zeller estimates the engine’s cooling will be 20% more efficient with the complex geometry enabled by additive.
The Pearl program has also expanded Rolls’s experience with additive, which started with electron beam melting used in XWB development and now includes laser powder bed fusion techniques used for Pearl. To increase productivity, each Rotherham machine now has four lasers which will enable four sets of tiles to be melted simultaneously. Zeller says another advantage of additive is at the program level.
Changes in design based on prototype tests can now be incorporated in the next prototype much more quickly, saving about 75% of the time required by traditional manufacturing processes.
The complexity and efficiency additive enables will be crucial as Rolls moves into new markets. “It will be important in electric flight, where power density, weight and cooling matter,” Mantle stresses. Rolls is now applying additive across its portfolio of aviation and non-aviation engines.
Rolls has worked with EASA and FAA for six years on certifying additive techniques, and now understands certain processes thoroughly. “Additive is no harder to certify than other difficult production methods on gas turbines,” Mantle notes. “You have to understand design, materials and fabrication.”
And that’s the barrier to entry for other companies that might seek to print replacement parts. They would have to obtain all the data on design, material and fabrication. Mantle says eight years ago, some worried that there would be many third parties that could additively manufacture engine components.
Today, both regulators and aftermarket companies understand the tough requirements necessary to ensure the integrity of printed parts.
In any case, Rolls is now looking forward to applying its additive skills lessons to the Ultrafan and any other future commercial jet engines.
Pratt & Whitney is working hard to catch up with GE and Rolls. The OEM is making a dedicated effort to modernize and transform its operations, in line with Raytheon Technologies’ Industry 4.0 strategy, according to additive manufacturing fellow Jesse Boyer. “Additive manufacturing is a key element of this strategy, improving performance, cutting lead times and driving efficiency,” Boyer says.
Pratt actually printed 30,000 plastic face shields to protect first responders during the pandemic, “much more than we initially thought possible in a short timeframe,” Boyer observes.
The Pratt fellow says his company’s merger with Raytheon in 2020 helps exploit synergies with its partner, including the Additive Manufacturing Process Capability Center at Raytheon Technologies’ Research Center.
The OEM’s small teams frequently use additive for prototyping, for example a single-piece static hot section, including combustor, for a small turbojet engine. “Additive manufacturing allowed the engine to develop from initial concept to test within 6-8 months, a process that usually takes 12-24 months.”
For the future, Pratt is focusing on additive advanced heat exchangers, acoustic panels, bearing supports, actuation system components and combustor components. And it is renewing an emphasis on additive repairs and production tooling. In terms of additive technologies, it is looking at powder bed fusion, directed energy deposition and binder jetting.
“We continue to develop powder bed fusion processes that result in more robust process control and process efficiency,” Boyer says. But the renewed focus on repairs and sustainment means Pratt is widening its interest to include directed energy deposition and binder jetting.
Pratt engines do not have many parts that have either the low maximum temperature, minimal fatigue or tensile requirements that would allow use of non-metallic components. Nevertheless, the OEM is monitoring the capability of newer composite-like materials that could be additively manufactured.
Boyer divides the potential of Pratt’s additive efforts into four use cases. First, additive may be used for part substitution or adaption. Here an existing part or component might be made additively because casting, forging or conventional manufacturing is encountering problems, and additive can reduce cost or lead time. There would be minimal changes in design and material.
Second, additive could be used for sustainment in the aftermarket. This is basically about replacement or repair of a fielded part. Lead times can be reduced with no design change.
Third, several parts may be combined into one additive component. Significant design and some material changes would help optimize supply chains and reduce material use, lead time and costs.
Fourth, additive could be used to optimize new part design the way GE and Rolls are doing, with a clean- sheet design for a specific engine-making purpose.