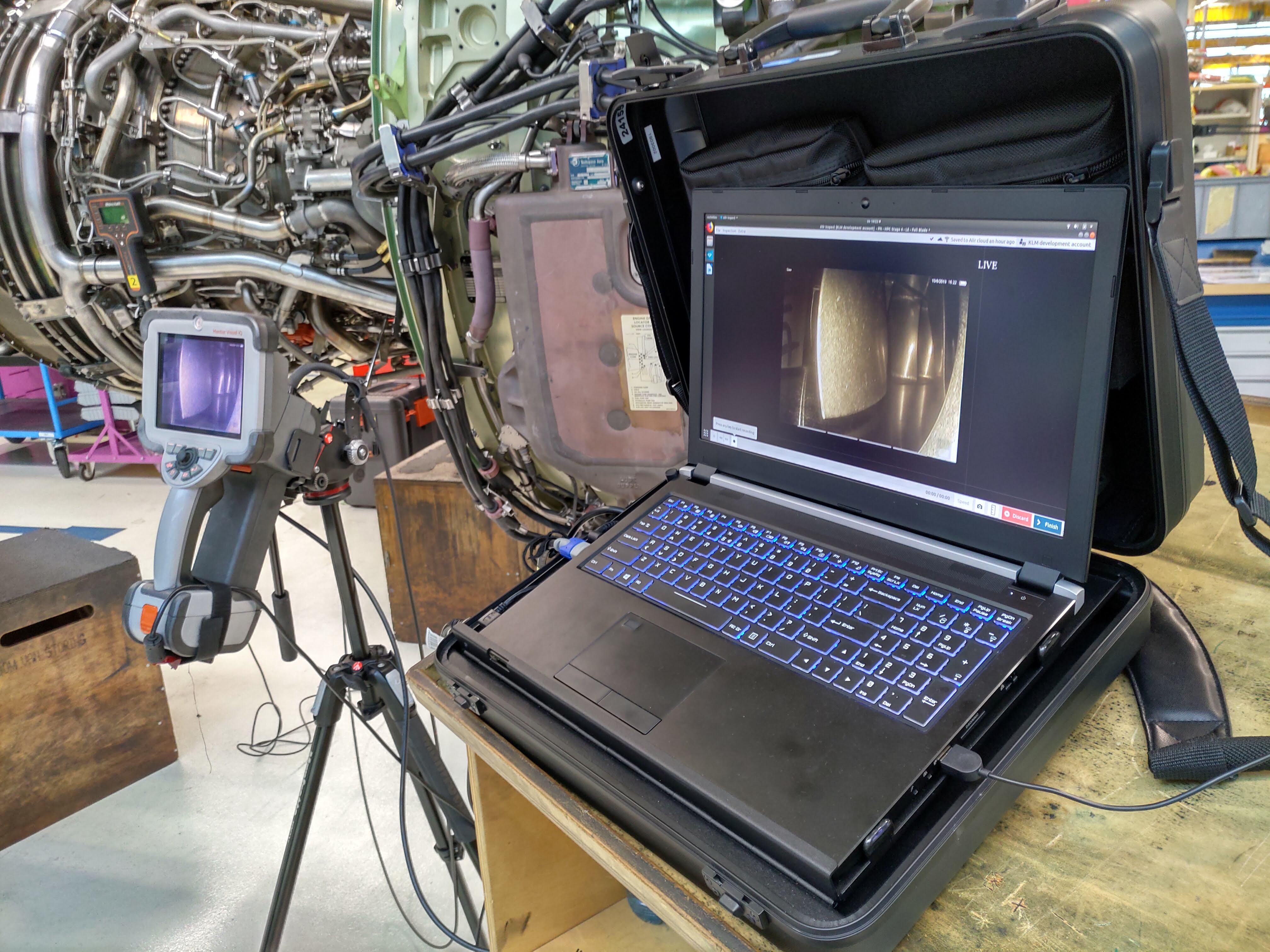
Travel restrictions imposed by the Covid-19 pandemic have forced aviation OEMs and maintenance providers to explore new processes for tasks normally undertaken with the customer present. For example, Airbus has pursued remote technical acceptance for new aircraft prior to their handover, while several engine shops have experimented with virtual engine inspections.
“Due to the COVID-19 pandemic and the resulting travel restrictions worldwide, there are an increasing number of instances when engine inspections are required, but it is extremely difficult to arrange for both MRO provider and customer to be where the engine and operator is,” says Remko Bruinsma, head of technical asset management for MTU Maintenance Lease Services.
“In turn, such virtual inspections have been a great way to assess the condition of the engine and enable customers to look inside, without physically having to be present,” he adds.
Mona-Caroline Stünckel, head of innovation management and product development, engine services, Lufthansa Technik, agrees, noting that “due to enduring travel restriction we see an increased demand from our customers for virtual engine inspections.”
Stünckel says the remote inspection process is similar to in-person inspections. “For the customer it offers the possibility to take part in the same process and see the same views as onsite. The decisions taken during the inspection are documented and permanently saved for both, the MRO and the customer. As always, our extensive inspection report is provided to the customer shortly after the engine inspection and contains a comprehensive visual presentation and explanation of the findings.”
Pros and Cons
Stünckel also notes that logging in remotely allows more people from the customer and technical sides to participate in an inspection, which “can speed up the process to arrive at the best technical decisions.” This is one reason why virtual inspections may persist even after travel restrictions have lifted, at least in certain circumstances.
“The use of the tools as replacement for an actual visit is highly individual,” notes Bruinsma.
“For some customers, it is helpful to see inside an engine without having the extra cost and effort of travelling to location. The videos, images and reports they receive afterwards are enough to satisfy their particular needs and they trust us to assess and take care of results. We expect such instances to continue post pandemic. For others, it is more a case of ‘needs must’ and a great tool in the pandemic, but they are likely to resume their own inspections once able to do so.”
Many engine MRO providers have not offered virtual inspections during the pandemic, while even enthusiasts for the technology such as Lufthansa Technik concede that face-to-face contact provides certain advantages.
“Before the crisis we were often able to combine the table inspection visit with the discussion of other topics, like contractual questions, invoice clarifications and engineering matters,” says Stünckel. “Of course we can do all this using communication technology, but lots of topics are easier discussed in person and face to face. Especially if different time zones, cultures and languages are involved.”
Although, end-of-lease checks are a good candidate for remote inspections, engine lessor Shannon Engine Support does not use the technology, preferring to rely on a network of trusted “housekeeper” MRO providers. “These housekeepers understand our processes and requirements, so we are satisfied that the inspections they perform on our engines are to the highest standards,” says Ivan Graydon, senior vice-president, technical, SES.
Technology
Remote inspections at Lufthansa Technik are provided via 5G datastreams and use in-house technology. The whole process is integrated into the company’s AVIATAR digital platform, which offers other fleet monitoring functions for the company’s customers.
When MTU carries out a borescope inspection at a customer location, it uploads the results to its specially designed portal, where they will be assessed by its technical asset managers and findings will be shared with the customer, who also has access to the portal. The company is also currently working on a livestream feature.
MTU is also looking at a further iteration of remote inspections via a collaboration with Dutch start-up Aiir Innovations. This uses artificial intelligence to analyze borescope inspection video footage and spot any degradation or damage. It also has a blade counting function.
“Such inspections are not intended to replace an actual engine check or borescope inspection,” says Bruinsma. “They are not certified by aviation authorities and are merely an additional support to the engineer at this time--both in terms of gaining insight when one is not physically present on location, but also to gain a comprehensive view of what is going on in an engine and aiding in removing the margin for human error in such checks.”
These and other technologies may advance the appeal of virtual inspections, although most MRO providers expect some return to physical inspections. However, with the remote genie out of the bottle, they also expect more customers to combine the virtual and the physical, to save on travel time and expense in cases where they do not deem it strictly necessary.
Virtual inspections may also be used more frequently in reverse, with MRO providers logging on to their customers’ video feeds to better prepare for an on-site visit.
“The digital inspection in combination with the portal can be used to better prepare the upcoming workscope and to gain a deeper understanding of the condition of the engine prior to physically seeing it,” says Bruinsma.