Sierra LIFE Inflatable Habitat Burst-Tested With Representative Window
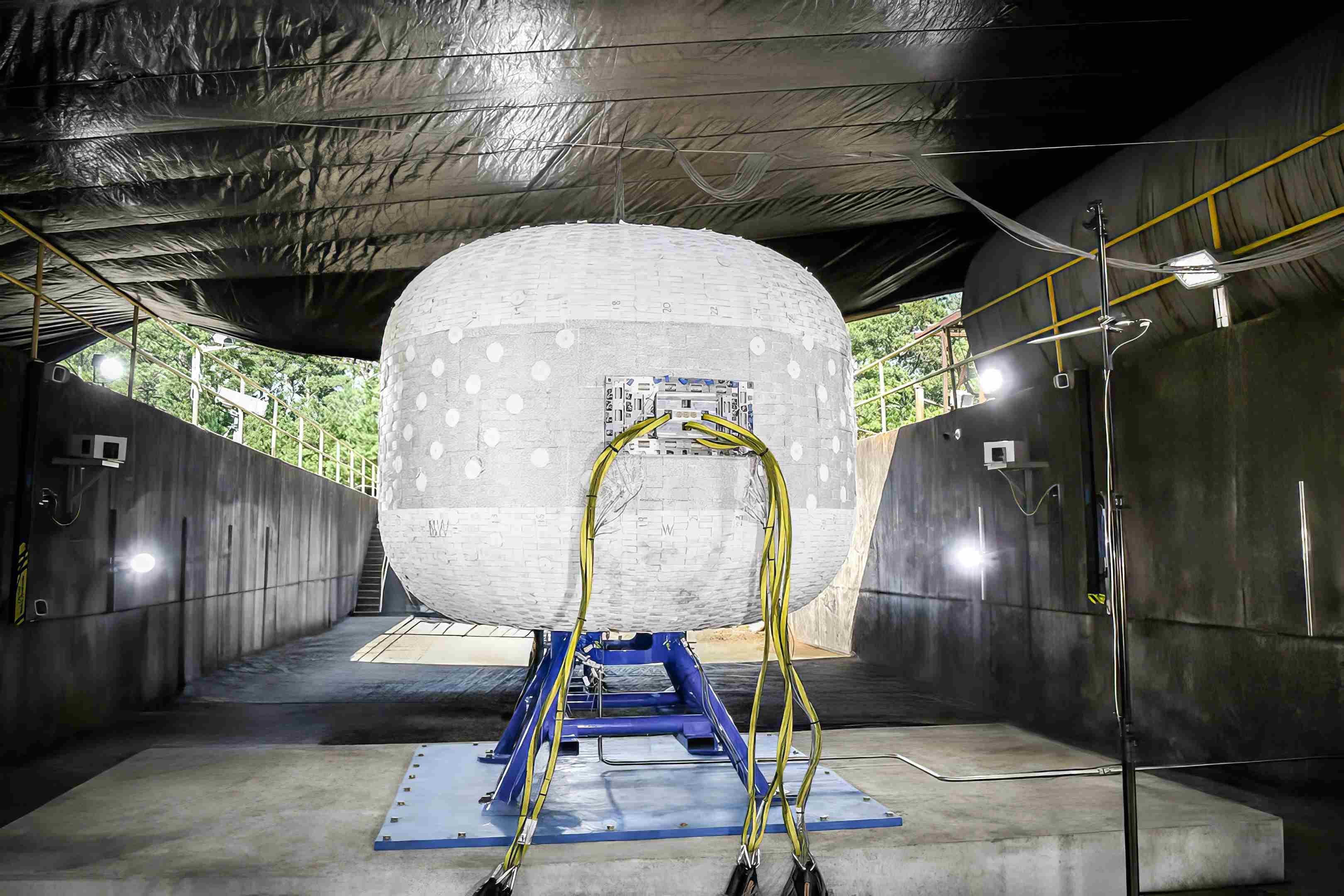
Sierra Space has been conducting tests on a sub-scale version of its LIFE inflatable habitat.
Credit: Sierra Space
COLORADO SPRINGS—Sierra Space has successfully completed a burst pressure test on a scaled version of its LIFE (large integrated flexible environment) inflatable habitat fitted for the first time with a metallic window structure. The test, conducted with soft goods partner ILC Dover and NASA at the...
Subscription Required
Sierra LIFE Inflatable Habitat Burst-Tested With Representative Window is published in Aerospace Daily & Defense Report, an Aviation Week Intelligence Network (AWIN) Market Briefing and is included with your AWIN membership.
Already a member of AWIN or subscribe to Aerospace Daily & Defense Report through your company? Login with your existing email and password.
Not a member? Learn how you can access the market intelligence and data you need to stay abreast of what's happening in the aerospace and defense community.