Pratt & Whitney Makes Hypersonic Revival As Pentagon Pushes Reuse

As reusable hypersonic propulsion rises up the list of U.S. Defense Department priorities, Pratt & Whitney now confirms it is working on a secretive development program called Metacomet aimed at solving the problem of fielding high-speed, reusable propulsion systems at low cost.
Already at least two years old, Metacomet—a name linked to a 17th century Wampanoag chief, the namesake of a ridge overlooking a Pratt & Whitney research facility in Connecticut—marks the company’s return to Mach 3-plus propulsion nearly a decade after selling its scramjet pioneer Rocketdyne arm to the parent company of Aerojet in 2012.
- Metacomet leverages SR-71 engine architecture
- Pentagon strategizes for reusable hypersonic push
- NASA, commercial sectors offer new options
With the intellectual property of the former Rocketdyne off limits, Pratt & Whitney’s GatorWorks division—a prototyping unit formed in 2018—launched Metacomet to focus on low-cost alternatives to ramjet and scramjet propulsion for high-speed flight.
The effort draws on the company’s expertise with gas turbine combat engines, and in particular reaches back to decades-old experience with the unique J58 engine developed for the Mach 3-plus Lockheed SR-71. That aircraft achieved sustained flight above the Mach cutoff point of a normal turbojet by diverting inlet air from the compressor directly into the afterburner.
“The faster you go, the larger the propulsion system is relative to the vehicle and how much payload and fuel you can actually fit in,” says David Stagney, senior director of GatorWorks. “So, we have spent a lot of time going back to the fundamentals and thinking about how to solve that problem differently. We know the Air Force wants to go really fast. They also want to have some very low-cost solutions, and to be able to have a large quantity of vehicles.”
As a result, Stagney says Pratt & Whitney is tackling the problem from a new perspective. “We think that we can provide unique capabilities building on the legacy we have from the Mach 3 engine that we built [several] decades ago,” he says. “Those core skills are still there, and our goal in GatorWorks is to come up with a whole portfolio of different solutions for a range of high-Mach solutions.”
The engine-maker believes its design approach, which is thought to be tailored to higher speeds above Mach 3 but below Mach 5, is simpler and more affordable because it avoids the need for pure ramjet/scramjet cycles or the complexities of mode transition to and from turbine power.
“Obviously, there are trade-offs between speed, range, cost and the amount of payload that you can take and fit onto a vehicle that makes sense economically,” Stagney says.
Metacomet appears to blur the normal distinction between “high-supersonic” and “hypersonic” regimes. Describing hypersonic as anything that travels faster than Mach 5 is a widely accepted definition—albeit arbitrary. To air vehicle designers, a hypersonic condition refers to a range of aerodynamic and thermal effects that arise at different speeds above Mach 5. They vary depending on the vehicle design and flight profile of the vehicle. These effects strongly influence the materials and shaping of the airframe, as well as the type of propulsion that is possible.
Stagney’s remarks about Metacomet suggest the program is pursuing engine configurations that can approach or exceed the arbitrary speed definition of the hypersonic term, but fall short of encountering the special aerodynamic and thermal effects at a system level.
“We’ve come up with some really unique different solutions to that problem across the whole spectrum of speeds,” he adds. “We want to offer different solutions that aren’t being thought about right now and that are much lower cost per effect.”
The work is particularly focused on reusability and a scalable architecture that can be applied to suit varying mission priorities across a combination of different sizes, payloads, ranges and speeds.
Although the company declines to provide specifics of the Metacomet solution set, test plans or potential applications, Stagney says the Air Force Research Laboratory’s (AFRL) proposed Mayhem demonstrator vehicle for a hypersonic, air-breathing propulsion system “is definitely one of the programs that we’re looking at, for sure.”
The AFRL revealed plans for the Mayhem System Demonstrator on Aug. 13 as a “larger-scale, expendable, air-breathing, hypersonic, multimission” platform that can carry “larger payloads over distances further than current hypersonic capabilities allow,” according to a formal request for information that was released to industry.
Despite its vintage, the J58, which was developed in the 1960s and retired when NASA ended test flights of the SR-71 in 1997, remains one of the most successful and ingeniously designed high-speed air-breathing engines.
While the engine’s close integration with the SR-71 airframe played a key role, the bulk of its success can be attributed to the aero-mechanical features of the J58 turbojet itself. These included axisymmetric mixed compression inlets and airframe-mounted, convergent-divergent blow-in door ejector nozzles—all aspects that could potentially be further developed for 21st-century applications.
The J58’s inlet spike, which translated longitudinally depending on Mach number, controlled the throat area and provided a stable shock structure across the speed range close to Mach 3.3. Above Mach 2.2 some airflow was bled from the compressor and fed through bypass ducts into the augmenter, transitioning the engine from a pure turbojet into a turbo-ramjet. At design cruise speed around 70-80% of the net propulsive force is derived from flow compression pressure on the spike.
However, as the turbine section was still partially interacting with the flow path, the maximum speed was governed by aerodynamic heating of the flow and the 800F temperature limit reached shortly after Mach 3.2. Aerodynamic analysis has indicated that the inlet design has the potential for operating at speeds up to and beyond Mach 5. Moreover, a configuration based on the J58 could go significantly faster than Mach 3.3 if modern materials and advanced cooling systems were incorporated to expand the temperature limits in the compressor.
Another potential area of improvement would be the modulation of the inlet flow and boundary layer. Other inlet controls in the J58 included the forward and aft bypass doors and the cowl and spike bleeds—which controlled boundary layer growth.
Later in service, including the final operational phase with NASA, the introduction of a digital automatic flight and inlet control system to orchestrate the position of the engine spikes and forward bypass doors had virtually eliminated the problem of inlet unstarts that hampered the aircraft in its early operation. Further improvement in control, and therefore performance, could be possible through the introduction of modern processors and faster actuators.
For additional performance growth, an updated J58 cycle could also conceivably provide a step toward higher Mach numbers. Options would include changes to the compressor design, materials improvements and adding supersonic combustion capability in the afterburner section. This radical redesign would also likely include fully closing off the turbine section for the maximum cruise condition.
Pratt & Whitney may also be dusting off J58 upgrade concepts studied in the late 1990s, when NASA evaluated boosting performance of the SR-71 to support its potential use in launching high-speed research vehicles and carrying captive experimental packages to higher speeds and altitudes. Some of these additional concepts involved increasing turbine exhaust temperature, raising compressor rotor speed, augmenting afterburner flow, and modifying compressor bleed and inlet guide vane schedules.
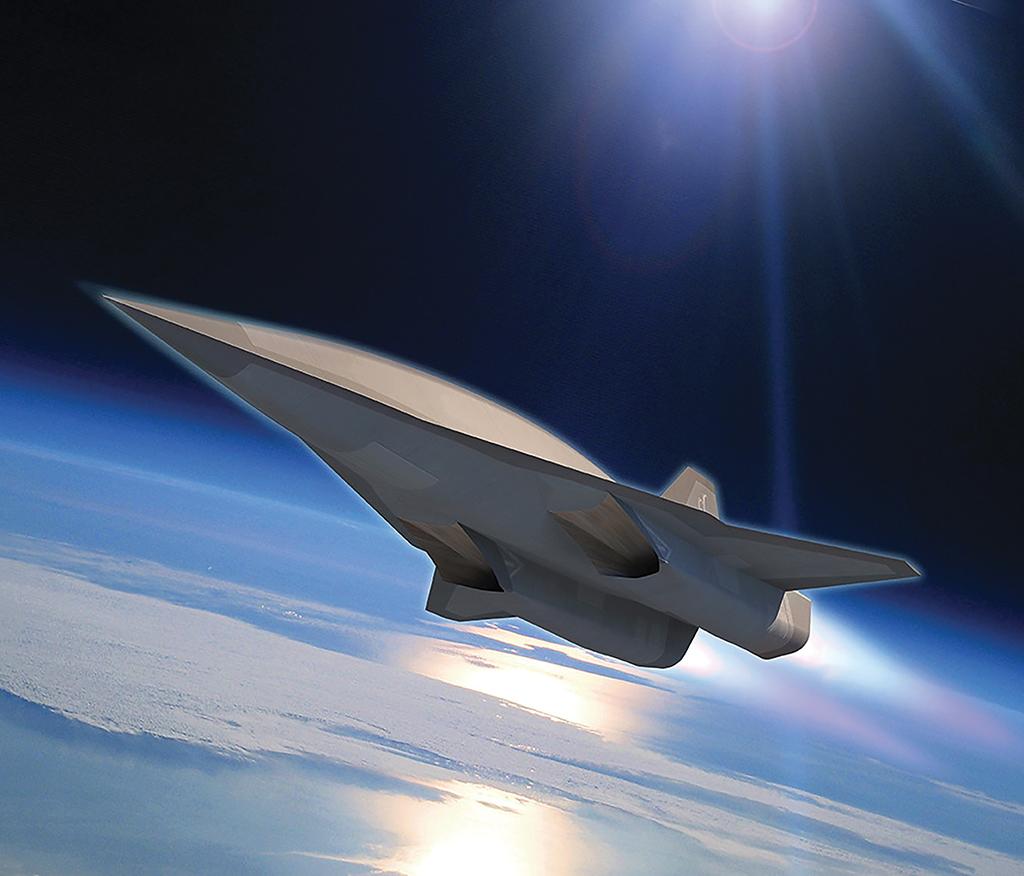
Pratt & Whitney’s pursuit of a reusable, high-speed propulsion system comes as the Defense Department’s Research and Engineering (R&E) branch starts to look beyond the initial rush to field multiple prototypes of offensive and defensive hypersonic weapon systems within this decade. If the push materializes into a new development program, the Defense Department could support the first reusable, operational system since the cancellation of the Lockheed Martin X-33 suborbital technology demonstrator in 2001.
The R&E branch is now developing a strategy to field reusable hypersonic systems to serve the strike and intelligence, surveillance and reconnaissance missions, as well as the first stage of a two-stage system for rapid access to orbital space, a Pentagon spokesman says.
The strategy document introduces the third element of the Pentagon’s wider plans for hypersonic technology.
Expendable missiles expected to be fielded within the next 2-5 years—such as the Lockheed Martin AGM-183 Air-Launched Rapid Response Weapon, the Army’s Long-Range Hypersonic Weapon, the Navy’s Intermediate-Range Conventional Prompt Strike and the Air Force’s Hypersonic Attack Cruise Missile-—comprise the first element. The Missile Defense Agency’s plans to deliver a terminal interceptor against hypersonic missiles in the mid-2020s, followed by a Glide Phase Interceptor in the late 2020s, represent the second element.
In addition to Mayhem and Pratt & Whitney’s offerings, the Defense Department also continues to develop a turbine-based combined-cycle engine. The Advanced Full-Range Engine, a project sponsored by DARPA and the Air Force, combines an off-the-shelf turbine engine—for flight up to Mach 2.5—with a dual-mode ramjet engine capable of supersonic combustion to reach speeds greater than Mach 5.
The path to reusable hypersonic propulsion also includes civil and commercial programs. NASA’s aeronautics research arm, for example, has launched the Hypersonic Technology project, which includes a special focus on reusable vehicle technologies for the airframe and propulsion system. The Air Force’s AFWerx innovation unit also is conducting market research on a proposal to provide financial and engineering support to commercial companies developing hypersonic passenger jets under the Vector Prime program.
The AFWerx effort could give a boost to several companies, including Reaction Engines and startup Hermeus.
“We are glad to see that initiative gaining momentum,” says Hermeus CEO AJ Piplica in an interview. “In our past lives, we’ve certainly been able to benefit from that kind of situation where the government opens up test facilities—whether it’s ground test or flight test—and then partners with commercial industry to generate data in new parts of the flight regime that we’ve never been in before.
“Being able to do that for supersonic and hypersonic flight could really provide some acceleration to both the industry and an Air Force road map for reusable hypersonic flight that is currently 15-20 years out,” Piplica adds. “So, if by partnering together with industry we’re able to shave 5-10 years off that road map, that would be a major win for the country.”
Comments