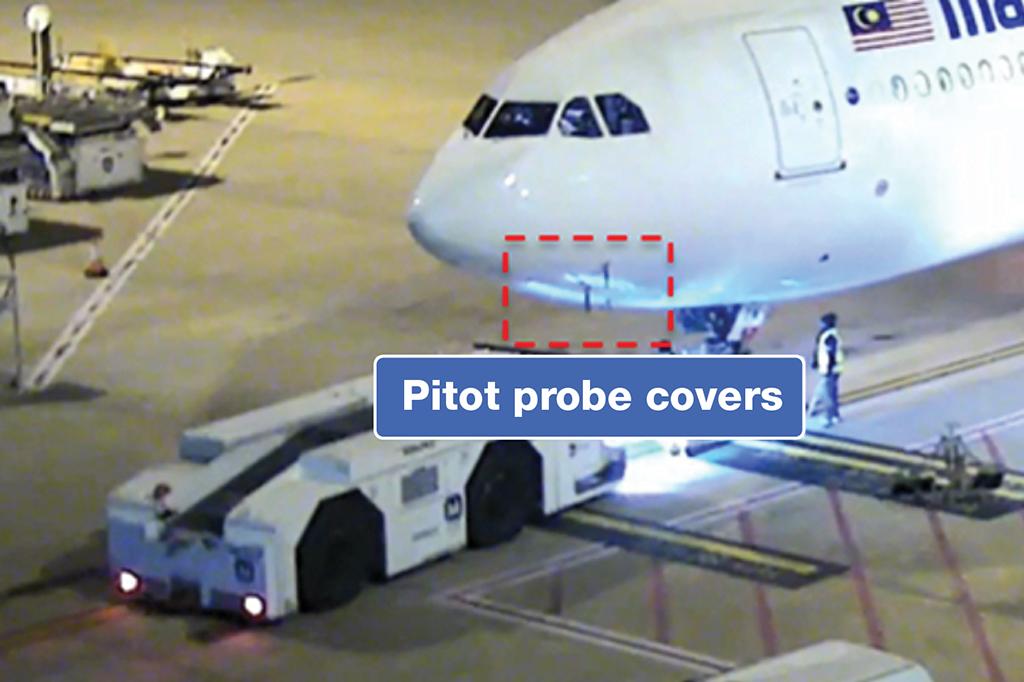
Sometimes you read an accident or incident report and when you’re done, you feel desperation for the operation’s safety hogan. This month’s Cause & Circumstance looks at two such events. Although the information is based on two preliminary reports, the lack of definitive causes at this point, I think, leads to more potential areas to explore as we try to understand what happened. In both cases, the crews performed in an exemplary fashion and returned broken airplanes with not a hair out of place on any of the passengers.
But how in the heck. . . .
On Oct. 27, 2017, at about 1900 Coordinated Universal Time, the crew of a Jetstar Airways Airbus A320 (VH-VGY) was going through normal preparation procedures for a scheduled passenger service from Auckland International Airport, New Zealand, to Sydney. The captain was designated as the pilot flying (PF) and the first officer was the pilot monitoring (PM).
It was an absolutely normal setup, a relatively short international flight, and a beautiful and modern machine in which to accomplish the task at hand. Back to the report.
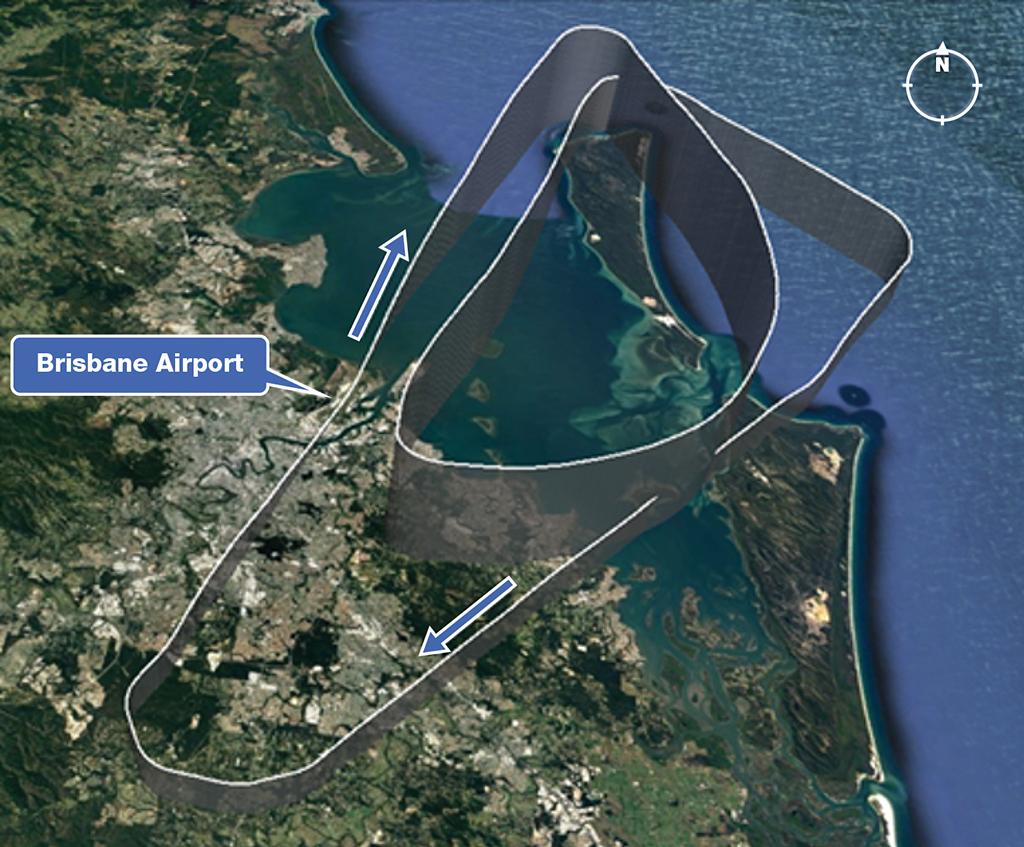
At about 1909, the so-called “leading hand” had finished loading the last container into the aircraft’s hold and was organizing his paperwork. It was raining, so he decided to put the clipboard in the right engine (No. 2) cowling to protect the papers, with the intention of retrieving them later. He went to the flight deck, gave some documents to the flight crew, and returned to the ground to organize the aircraft’s pushback.
“Leading hand” is not a term with which I was familiar. Doing research on Australian and New Zealand job positions I found that the person so designated typically performs all or some of the following duties: They supervise and train subordinate personnel — in this case, the ground personnel. They also sometimes supervise contractors and subcontractors, oversee the operation of vehicles and construction materials, set schedules, and monitor health and safety through quality assurance and environmental planning. In other words, this is the main person around the airplane while it’s on the ground.
At about 1919, the dispatcher cleared the ground and servicing equipment from the aircraft and conducted the “duty of care” walk-around. In so doing, she noticed the clipboard in the right engine and thought the leading hand would return for it, so she continued with the walk-around. Soon after, the engines reportedly started normally.
Minutes later, as the aircraft was taxiing, the leading hand realized his clipboard was missing and thought the dispatcher had the paperwork. When he asked her about it, she mentioned having seen it in the right engine. When the ground crew returned to where they had prepared the aircraft, they noticed paper debris on the ground and alerted operations to contact the pilots.
However, the Airbus had launched before word of the missing clipboard reached the crew. As they climbed through FL 150, the pilots received a radio call from Auckland Approach directing them to contact the surface movement controller. The captain handed control to the first officer and made the call. Only then was he advised the ground crew had lost their paperwork and it may have been placed on the engine. The captain asked whether the paper was on top of the engine or inside the inlet and was told the latter. Checking the engine instruments, the pilots saw no abnormal indications.
The captain then contacted his carrier’s engineer at the airport and asked whether the missing paperwork had been loose or held by a clipboard with a metal clip. The engineer advised there had been a clipboard and that a piece of sheared metal had been found. The flight crew decided to return to Auckland.
After landing at about 2048, the No. 2 engine was inspected by technicians, who discovered paper throughout. They also found minor damage to a fan blade and attrition liner.
Additional Notes
The leading hand later explained he had felt the need to shelter the paperwork from the wind and rain. Normally, staff use the pushback tractor for shelter during adverse weather and to prepare paperwork for the flight. There is a metal box on the loader to store the folder. However, as the pushback tractor was not yet present at the bay, he used the engine cowling. He recalled that he did not feel pressured to rush the departure.
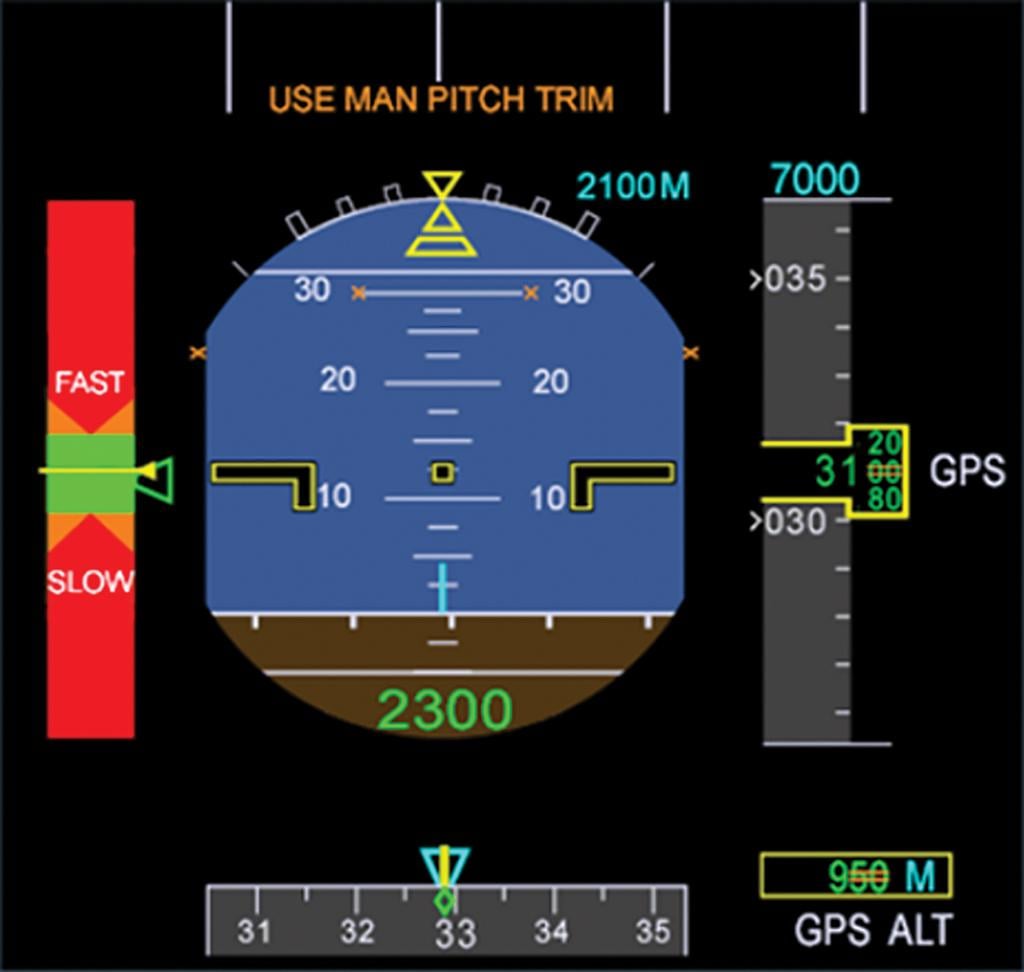
The dispatcher stated she did not view the clipboard as a foreign object damage (FOD) threat as it belonged to the leading hand and held the paperwork for the flight. She assumed he would retrieve it prior to engine start-up.
The captain stated that, to obtain more information about the incident, numerous calls were made to other agencies, which took considerable time. Further, due to poor communications, he was unable to contact the operator’s maintenance controller to discuss the engine’s status.
Procedures
The internal investigation into the incident by the ground-handling operator noted the Jetstar Airways operational manual stated all staff operating near the aircraft were to be constantly observant for abnormalities and to report these to the leading hand or supervisor prior to the aircraft departing.
The investigation also noted there was no procedure for the ground crew to establish communications with the flight crew in the event of a non-normal or emergency situation, either prior to or after the aircraft’s departure. Further, there was no guidance on how paperwork was to be prepared and managed by ground crew during adverse weather conditions.
Safety Action
Both the airline and the ground-handling company issued a notice which outlines that FOD also includes items accidentally left behind. It further states engines are not to be touched or used for the placement of items, and emphasizes the responsibilities of ground crews to manage foreign object debris by clearing it and reporting its presence to other crewmembers.
As a result of this incident, Jetstar Airways released an updated aircraft dispatch procedure, which included:
A specific warning about not placing items in the engine cowling.
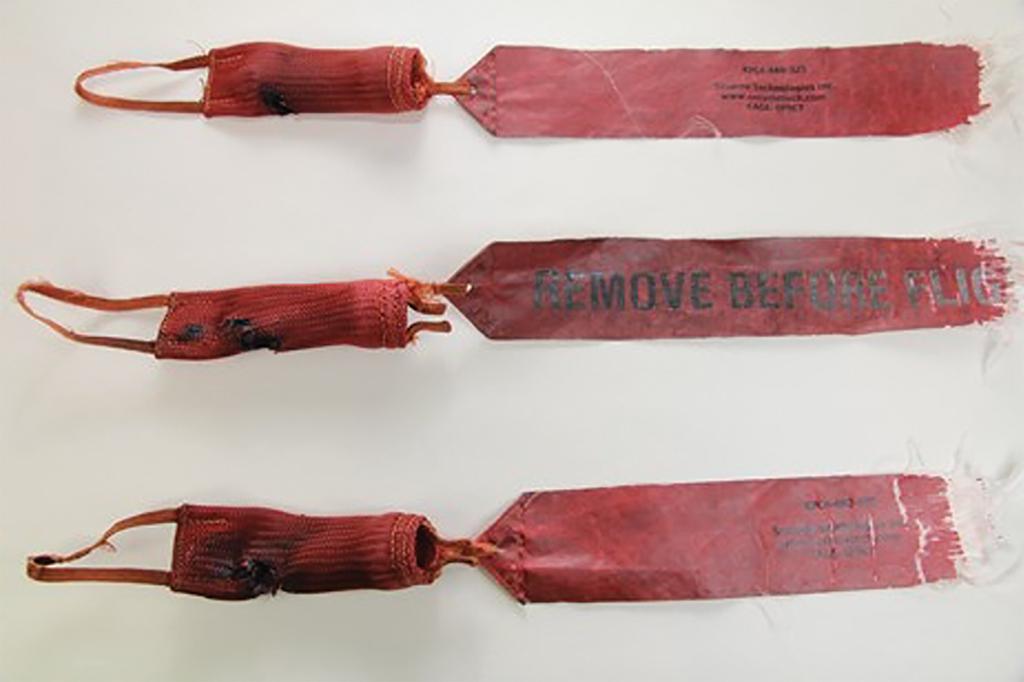
Improved detail around checks and responsibilities.
A section on emergency and non-normal procedures.
Detailed methods for reestablishing communications between ground crews and flight crews, such as visually gaining the attention of the flight or contacting them via radio.
We’ll discuss this further in the “Solid Ground Procedures” sidebar, but for now, let’s have a look at the second incident I wanted to review.
Here too, there are still too many unknown factors and operational considerations to assess blame. Nevertheless, someone missed a very simple, very important step. Without an operational airspeed indicator, the flight crew’s use of their aircraft’s angle-of-attack (AOA) indicators for speed information and GPS for altitude were exceptional. There can be no doubt about that. Nevertheless, we can all ask why such exemplary airmanship became necessary in the first place.
On July 18, 2018, a Malaysia Airlines Airbus A330-300 (9M-MTK) was scheduled to operate a passenger flight from Brisbane, Australia, to Kuala Lumpur, Malaysia. The scheduled departure time was 2320 local.
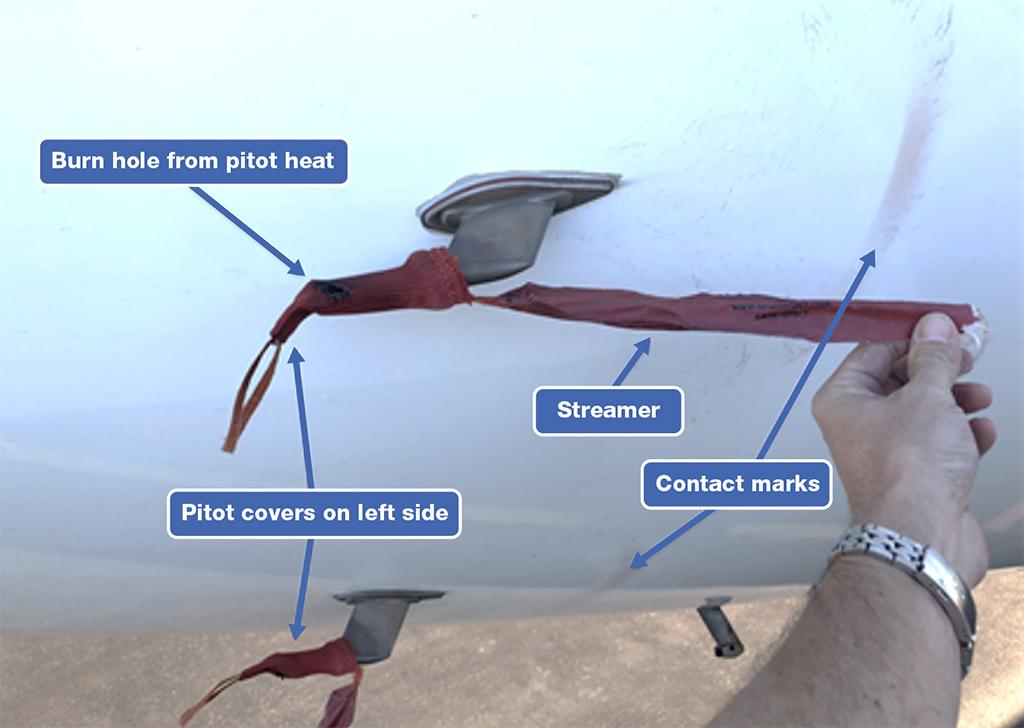
The aircraft had landed at Brisbane Airport at 2011, after a flight from Kuala Lumpur. The captain, first officer and certifying maintenance engineer from the previous night’s flight, who had been resting at a Brisbane hotel, arrived at the airport to begin their duties for the outbound flight.
Soon after the aircraft had landed, covers were placed on its three pitot probes. Subsequent inspections during the turnaround did not identify the presence of the covers and they were not removed prior to the aircraft’s departure. (See Figure 1 on the opposite page.)
The first officer was the PF and the captain was the PM. Prior to aircraft pushback, the two calculated the aircraft’s critical “V” speeds for the takeoff with V1 at 153 kt. and Vr at 160 kt. The airline’s standard operating procedures for takeoff required the PM to announce when the airspeed reached 100 kt. and for the PF to cross-check this airspeed indication.
The wind was calm and the sky was clear. At 2324, the flight crew began to taxi to Runway 1. They started their takeoff roll at 2331:05, and 33 sec. later the captain called “100 kt.” The PF initiated rotation at 2331:47; groundspeed at the time was 165 kt.
The flight crew recalled that they detected an airspeed anomaly during the takeoff roll, including red speed (SPD) flags on both primary flight displays (PFDs).
The SOPs stated the captain held responsibility for the decision to reject the takeoff or to continue. It noted rejecting a takeoff between 100 kt. and V1 was a serious matter, that a captain should be “go-minded,” and under those circumstances few situations justified rejecting the takeoff. There was no indication on the CVR that the pilots discussed rejecting the takeoff.
Probably one of the hardest decisions a pilot can make is a high-speed abort below V1. Every second of indecision adds more speed and eats up hundreds of feet more runway. Many serious incidents have occurred in this speed range. A few miraculous saves have been made when pilots aborted a takeoff above V1. Also, V1 may be predicated on a much shorter “balanced field” than the runway that is actually available. While heavier loads can be flown by unbalancing the field, and we did in the U.S. Air Force Airlift Command, this was not a standard procedure in my civilian experience. That means there can be a very large gray area involved. Is it wrong to abort a takeoff just before rotation and well-past V1 if the computed balanced field is 5,500 ft. and the flight is departing on a 13,000-ft. runway?
After takeoff, the flight crew carried out actions for unreliable airspeed indications and made a PAN call to air traffic control (ATC), advising they had unreliable airspeed indications.
The flight crew continued to climb above 10,000 ft. and maneuvered the aircraft to the northeast of Brisbane Airport where they carried out several checklists, troubleshooting and preparation for an approach and landing on Runway 1. (See Figure 2 on page 27.)
In accordance with published procedures, the pilots turned off the three air data reference systems (ADRs) at 1343. This activated the aircraft’s backup speed scale (BUSS), which provided a color-coded speed scale derived from AOA and other information, and altitude derived from GPS data. (See Figure 3.) The flight crew also obtained groundspeed information from ATC, and used the aircraft’s radar altimeter.
Normal landing-gear extension could not be accomplished with all three ADRs off. The flight crew performed a landing-gear gravity extension before conducting an overweight landing at 0033.
After landing, the pilots stopped the aircraft on the runway as nosewheel steering was unavailable following a landing-gear gravity extension. The main landing gear doors, which remain open following a gravity extension, had minor damage where they contacted the runway surface. The aircraft was towed to the gate, where the passengers and crew disembarked. There were no reported injuries during the flight.
A subsequent inspection identified that the pitot probe covers were still fitted to the aircraft’s three pitot probes after it landed.
Recorded Data
The Australian Transport Safety Bureau (ATSB) recovered and downloaded data from the aircraft’s CVR and FDR, and obtained data from its digital ACMS (aircraft condition and monitoring system) recorder (DAR), used for routine monitoring by the operator.
The data from the CVR and FDR contained all of the occurrence flight, while the DAR included all data up to 2348 and intermittent data after that time. At the time of publication, the ATSB had not fully validated the data and analysis was ongoing.
The aircraft had three sources of airspeed:
ADR1, processing data for the captain’s pitot probe on the left side of the airframe, and usually presented on the captain’s PFD.
ADR2, processing data from the first officer’s pitot probe on the right side of the airframe, and usually presented on the first officer’s PFD.
ADR3, processing data from the standby pitot probe on the left side of the airframe, and usually presented on the integrated standby instrument system to the right of the captain’s instruments.
Airspeed was not recorded or displayed to the flight crew when it had a calculated value below 30 kt.
The FDR recorded airspeed from ADR3 once per second, and additionally from any one of the three ADRs twice per second depending on flight crew selection and data validity. Data from the FDR showed ADR1 first sensed airspeed above 30 kt. at 2331:39. At rotation, the FDR recorded 38-kt. airspeed from ADR1 and the airspeed from ADR3 had not yet reached 30 kt. ADR3 first sensed airspeed above 30 kt. at 2331:54.
The DAR sampled airspeed once per second and preliminary analysis shows broadly similar values as the FDR.
The maximum recorded airspeeds after takeoff were 66 kt. on the FDR and 57 kt. on the DAR, prior to the ADRs being selected off when the data became invalid. These recorded airspeeds were consistent with the pitot probes being covered.
Preliminary analysis of the available groundspeed and AOA data indicated that the aircraft was flown within operational limits. However, determination of the airspeed indications and related warnings and cautions being displayed to the flight crew during the takeoff roll was not available for the initial report.
A lot of this recorded data left me confused. If the covers were still on, how was airspeed recorded at all? I included the data because I’m sure how and why the readings were obtained with the covers in place will be explained in the final report. Nevertheless, none of that is germane to the problem at hand. Specifically, why were the pitot covers not removed?
Buzzing at Brisbane
There have been multiple reports of insect activity disrupting aircraft systems at Brisbane Airport. These included blocked pitot probes, mainly from nests built by mud-dauber and other wasps, resulting in airspeed discrepancies and other effects.
A preliminary review of the ATSB database indicated that from 2008 to 2018 there were at least 15 incidents involving high-capacity transport aircraft departing from Brisbane in which one of the pitot probes had a partial or total blockage, at least four of which were identified as insect nests. These resulted in three rejected takeoffs, four aircraft returning to Brisbane after continuing the takeoff and one aircraft that continued to its
destination.
In May 2015, the Civil Aviation Safety Authority (CASA) issued Airworthiness Bulletin 02-052 Wasp Nest Infestation — Alert to “urgently advise operators, maintainers and pilots of the dangers associated with undetected wasp infestation in aircraft, and the circumstances under which they can occur.” It stated that wasps could build nests in aircraft that are stationary for more than 20 min. with uncovered pitot probes.
From November 2015 onward, the Airservices Australia-produced publication “En Route Supplement Australia” entry for Brisbane Airport included a note that stated:
“Significant mud wasp ACT WI AD VCY [activity within aerodrome vicinity] affecting pitot tubes [probes]. Pitot tube covers recommended.”
Similarly, the Jeppesen aeronautical information publication “Australia Airport Directory,” used primarily by international pilots operating into Australia, also had the following in the Brisbane Airport information section:
“Significant mud wasp activity within apt [airport] vicinity affecting pitot tubes. Pitot tube covers recommended.”
Some operators using Brisbane use pitot probe covers for routine turnarounds.
Ground Handling at Brisbane
On the day of the occurrence, aircraft turnaround duties were shared among:
A maintenance technician from the operator who was rostered to return to Kuala Lumpur as a passenger on the departing aircraft.
Two non-certifying technicians from the engineering support provider.
Four ground handlers from the ground-handling service provider.
The operator’s personnel and the ground handlers were both responsible for conducting pre-departure checks.
Use of Pitot Probe Covers
The pitot probe covers were fitted on the aircraft’s three pitot probes by one of the engineering support personnel, as it was his understanding this was normal practice. He later reported he advised the operator’s maintenance technician that pitot probe covers were fitted during a brief exchange discussing turnaround tasks, but the technician did not directly respond. The technician later reported he did not recall hearing the advice, and he did not make an entry in the aircraft’s technical log to record the covers had been fitted.
The presence of the pitot covers was not detected by the operator’s maintenance technician or captain during separate external aircraft inspections. The maintenance tech boarded the aircraft during turnaround, and the engineering support personnel left the bay to attend to other aircraft. The pitot covers were not detected by ground handlers during pushback.
The flight crew and operator’s maintenance tech later reported they would not routinely use pitot probe covers on a turnaround. They advised that the operator did not normally fly to airports where the use of pitot probe covers was standard. Security video recordings of the operator’s three previous turnarounds at Brisbane Airport showed pitot probe covers were not used.
Examination of the three covers fitted to the aircraft following the occurrence found each had a hole burned through where the cover folded around the probe in the airstream. The streamers were damaged by contact with the aircraft skin during the flight. (See Figure 4 on page 30 and Figure 5 on page 31.)
Proactive Safety Measures
Whether or not the ATSB identifies safety issues in the cours we of an investigation, relevant organizations may proactively take steps to reduce their safety risk. Indeed, the Safety Bureau has been advised of the following actions in response to this occurrence.
The operator notified all of its technicians and flight crews of the need for pitot covers to be fitted to aircraft at Brisbane Airport during turnarounds or when parked, as well as the required procedures for their removal.
The operator and maintenance support provider clarified and formalized more detailed service level arrangements.
The maintenance support provider improved its procedures for conducting turnarounds, including improved inspection, documentation and tool control.
The ground-handling service provider gave all employees a “read and sign” bulletin emphasizing its arrival and departure inspection procedures.