Structural Integrity Factors Can Cause Premature Failure, Part 1
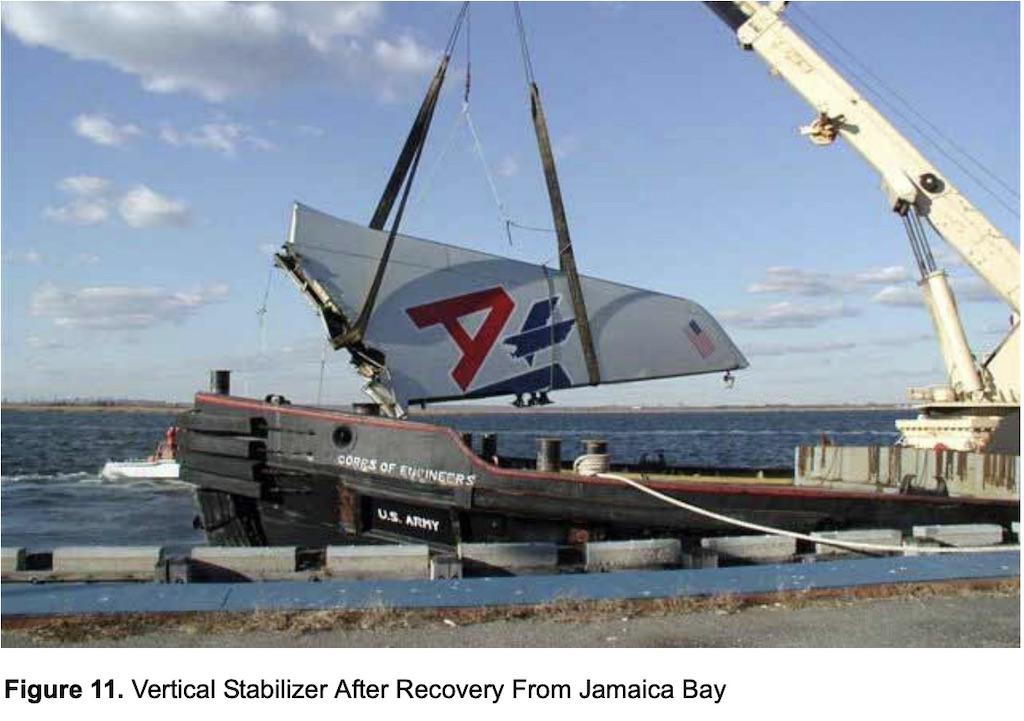
The probable cause of the American Airlines Flight 587 crash on Nov. 12, 2001, was "in-flight separation of the vertical stabilizer as a result of the loads beyond ultimate design that were created by the first officer’s unnecessary and excessive rudder pedal inputs," the NTSB said.
“We’re going to teach you how to turn and burn” were the exact words used by the founder and president of Aviation Safety Training, a company specialized in upset recovery training. The decorated Vietnam War veteran fighter pilot promised to immunize the pilots at my employer against loss-of-control accidents after completing his two-day training curriculum.
The sales pitch included descriptions of how to “yank and bank” and use large deflections of the rudder to roll the aircraft during recoveries from extreme, unusual attitudes. To an audience of pilots, this sounded like a lot of adrenalin-pumping fun.
At the conclusion of the sales presentation, the owner of Aviation Safety Training offered me a demonstration ride, hoping that I would write a full-length article hyping this training. Even though this could have been an article with plenty of eye-grabbing pictures, I declined for many reasons. First, the sales presentation did not provide independent evidence of the efficacy of this training. Second, his explanations on the uses of the rudder for upset recovery were contrary to the NTSB’s findings during the investigation of the American Airlines Flight 587 accident on Nov. 12, 2001. Third, I had grave concerns about the structural integrity of the aircraft used in such maneuvers, especially considering the NTSB findings of several closely related accidents.
The timing of the sales pitch was not long after the NTSB issued its findings about a fatal accident over Rydal, Georgia on April 19, 1999. The aircraft involved was a T-34A “Mentor” operated by Sky Warriors Flight Training.
During the simulated combat flight, the safety pilot instructed the client to turn harder and to bury the nose. While following the safety pilot’s instructions, the right-wing assembly separated from the airframe. The main airplane wreckage fell to the ground along the edge of a wooded area of a subdivision. The right-wing assembly was located approximately one-half mi. north of the main wreckage. Examination of the wreckage disclosed fatigue cracking in the spar material in the vicinity of wing spar fracture face.
The NTSB determined that the probable cause was the fracture of the wing spar as a result of fatigue cracking that occurred over an unknown number of flights and flight hours, with a wing-loading spectrum not anticipated during design of the airplane.
What is Loading Spectrum?
“Loading spectrum” is a formal engineering analysis of the structural loads that an aircraft is likely to experience from maneuvering and atmospheric turbulence during its lifetime. Structural engineering specialists use this information to predict the safe lifespan of an aircraft’s structure.
The Loading Spectrum will vary significantly based on an aircraft’s predicted usage. For instance, the standard for a mid-range transport might assume an average flight length of 2.5 hr., flying at an average altitude of 38,000 ft., and performing three flights in an average day. While cruising at 38,000 ft., based on historical trend data, it would encounter moderate atmospheric turbulence for a small portion of its cruising duration on some of those flights.
The engineers would also formulate a prediction of the number of pressurizations cycles on the fuselage and the amount of stress placed on the wings from atmospheric turbulence. A number of other important assumptions are made in these predictions, such as the average temperature, atmospheric humidity and salinity. All of these are critical factors that influence the growth of cracks.
Cracks may grow to catastrophic lengths prior to the component being removed from service when aircraft are used in a manner that falls outside of the original loading spectrum. The prime example of this was the Aloha Airlines Flight 243 accident on April 28, 1988, in which a portion of the fuselage shell failed catastrophically in flight.
These accidents should have raised elevated concerns among operators who provide upset recovery training, as well as any other aircraft operator who uses their aircraft in a manner that doesn’t fall within the original design criteria.
Asymmetric Loading
A second important point that continues to be poorly understood is the additional stress that occurs on an airframe when a pilot’s control inputs create asymmetric G loads. The original design G-load limits of the T-34 series of aircraft were 6.0 and -3.0. At face value, this would give pilots the impression that this was a tough airplane that could withstand plenty of G loading. But that is an overly simplified understanding of structural integrity.
Changing bank angle while simultaneously changing the G load creates a differential in the loading of one wing (or one stabilizer) relative to the other. The ascending wing is experiencing a higher load factor than the descending wing. This, in turn, applies a twisting force on the attach points that will be much more powerful than if the G load is applied symmetrically on the airframe. The G limits reduce to +4 / -2 Gs for “rolling” maneuvers.
In Part 2 of this article, we discuss the danger of operating outside of an aircraft’s G load limitations.